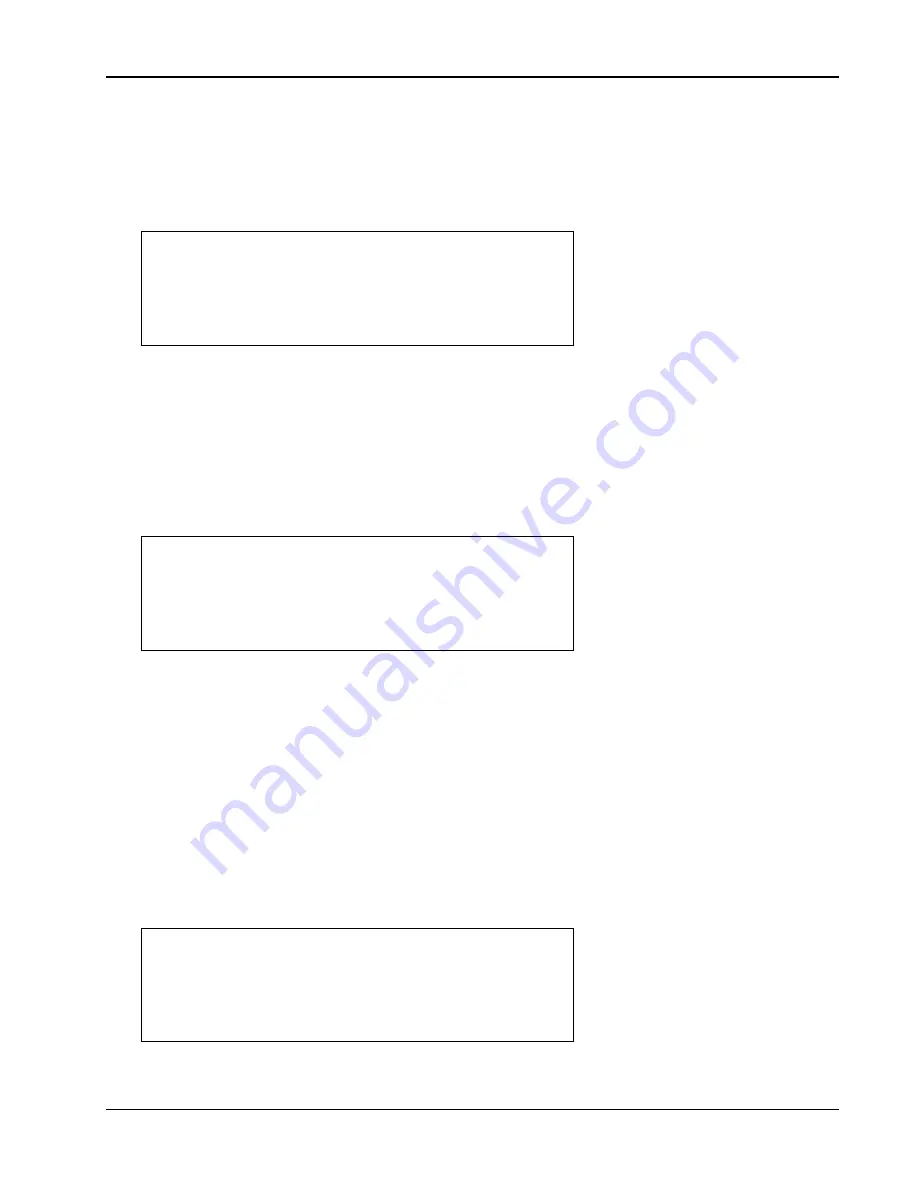
Lake Shore Model 370 AC Resistance Bridge User’s Manual
4.11.2.3 Setpoint
Units
Closed-loop temperature control will operate with a setpoint in resistance units for any input channel and a setpoint in
Kelvin for any channel that has a temperature response curve assigned to it. Setpoint units will default to ohms if no
curve is selected for the control channel. If the setpoint units are changed during control, the instrument will convert the
setpoint value to the new units when possible to minimize disturbance to the load.
The next control setup screen appears as a prompt for setpoint units.
Control Setup
Select With °®
Setpoint Units: Kelvin
Use the
s
or
t
key to select setpoint units of ohms or Kelvin. Press
Enter
to accept the new selection and continue to
the next setting screen. Press
Escape
to cancel the new selection and return to the normal display.
4.11.2.4
Setpoint Change Pause Time
The temperature control loop needs time to settle after any setpoint change. If temperature control is active while
scanning channels, the loop may not get enough time to settle into the new setpoint before the scanner moves away from
the control channel. The instrument can be forced to read only the control channel for a period of time after any setpoint
change to guarantee settling. This time period is set with the setpoint change pause parameter. Manually changing
scanner channel will override the pause and force a reading.
The next control setup screen appears as a prompt for the setpoint change pause time.
Control Setup
Enter A Value For
Setpoint Change Pause Time: 25 s
Use the data entry keys to enter a change pause time from 1 to 255 seconds. Press
Enter
to accept the new selection and
continue to the setpoint ramp feature, Paragraph 4.11.7. Press
Escape
to restart the setting sequence and enter a new
value. Press
Escape
again to cancel the sequence and return to the normal display.
4.11.2.5 Control
Filter
During normal operation the PID control algorithm uses the unfiltered input readings from the control channel as its
feedback. This method offers the best control stability and some noise immunity because of the natural averaging that
takes place in the integrator (I) part of the control equation. The control algorithm can be configured to use filtered
readings instead of unfiltered readings. This configuration can improve noise rejection but it is sometimes at the expense
of more difficult tuning or even control instability. The filter creates time lag that destabilizes the control loop. Control
uses the same firmware filter parameters set for the control input channel. Any control application should be tuned first
with the control filter off. Filter action should be added gradually, starting with a very short settling time, and
adjustments to P and I made be required along the way (most often P will decrease and I will increase). The filter time
constant should always remain shorter than the I setting in seconds.
The next control setup screen appears as a prompt for control filter On/Off.
Control Setup
Select With °®
Control Filter: Off
Use the
s
or
t
key to select control filter on or off. Press
Enter
to accept the new selection and continue to the next
setting screen. Press
Escape
to cancel the new selection and return to the normal display.
Operation
4-17