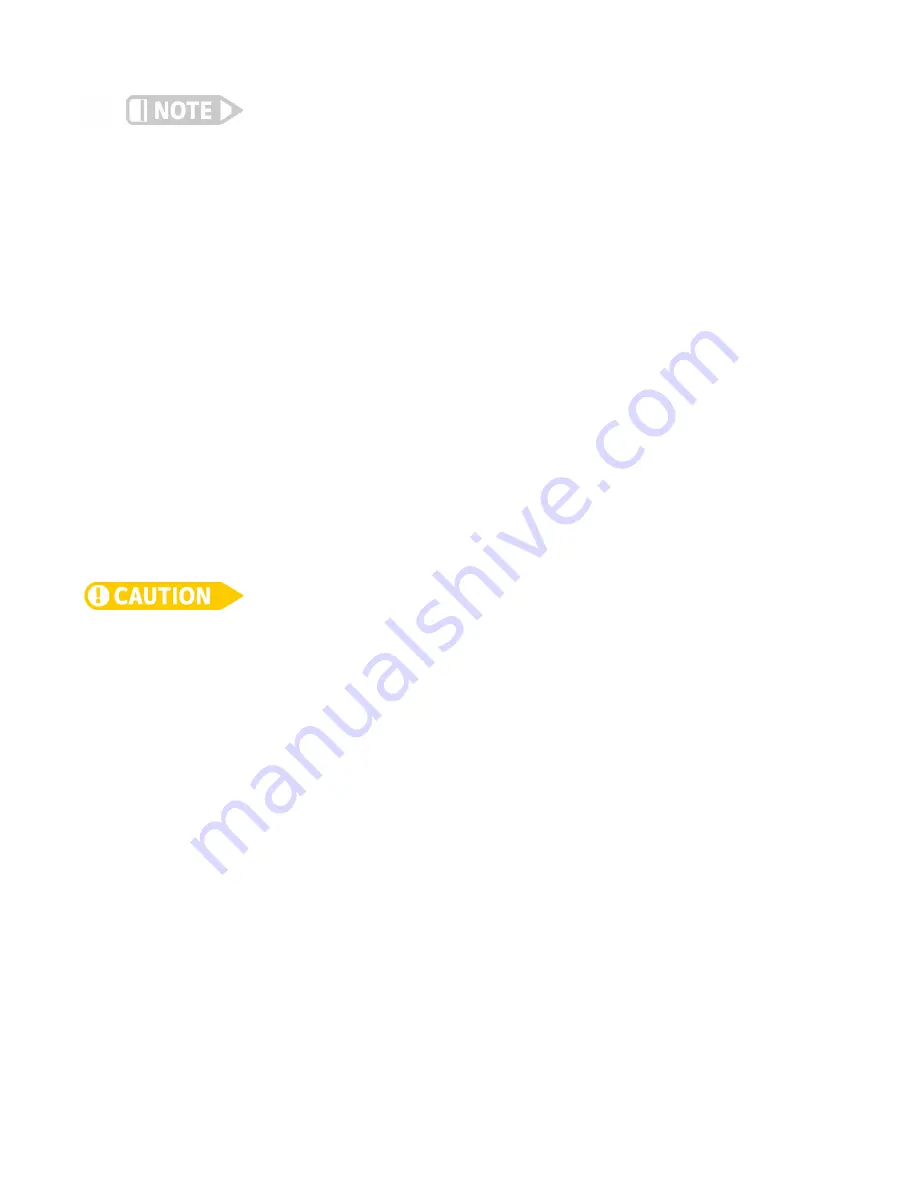
78
c
HAPTER
4:
Operation
Model 350 Temperature Controller
If desired, the control parameters can be changed manually, just like Closed Loop PID
mode, but they will be automatically updated once the setpoint crosses a zone boundary.
The control algorithm used for each zone is identical to that used in Closed Loop PID
mode. The Zone feature is useful by itself, but it is even more powerful when used
with other features. We recommend using zone mode with setpoint ramping (section
4.5.1.5.7). Refer to section 5.3 for details on setting up zones. Refer to section 2.13 for
a detailed discussion of PID control.
Menu Navigation:
Output Setup
Q
Output
(1, 2, 3, or 4)
Q
Output Mode
Q
Zone
4.5.1.4.3 Open Loop Mode
Open Loop output mode allows you to directly set the output using only the
Manual Output and Range parameters. This guarantees constant current to the load,
but it does not actively control temperature. Any change in the characteristics of the
load will cause a change in temperature.
You can configure any output to Open Loop mode. When an output is configured in
this mode, the Manual Output and Heater Range parameters become available in the
Output Setup menu for setting the output. For convenience, the Control Input param-
eter can be used to assign a sensor input, which then allows the output to be dis-
played on the front panel when using that sensor input’s display mode. When
displayed on the front panel, the Manual Output and Heater Range direct operation
keys can be used for one touch access to these settings. Refer to section 4.3.1 for
details on configuring display modes.
Since there is no sensor feedback in open loop mode, there is nothing to prevent the sys-
tem from being overheated. We recommend using the Temperature Limit feature to help
protect the system from overheating. Refer to section 4.4.11 for temperature limits.
Menu Navigation:
Output Setup
Q
Output
(1, 2, 3, or 4)
Q
Output Mode
Q
Open Loop
4.5.1.5 Control Parameters
Once the output mode is chosen, the control parameters can be used to begin con-
trolling temperature. Control Input is used to create a control loop. The P, I, and D
parameters provide fine tuning of the control algorithm. Manual Output provides a
baseline output power about which to control. Setpoint is used to set the desired tar-
get temperature, and Heater Range is used to turn on the control output, as well as to
set the power range of the output. These parameters are described in detail in section
4.5.1.5.1 to section 4.5.1.5.8.
4.5.1.5.1 Control Input
For closed loop control (Closed Loop PID, Zone, Warm Up Supply) a control loop must
be created. A control loop consists of a control output for controlling the temperature,
and an input for feedback into the control algorithm. Use the Control Input parame-
ter to assign the control input sensor to the desired output.
In the Monitor Out mode the Control Input parameter is used to determine the source
of the output voltage. In the Open Loop mode, the Control Input parameter can be set
simply for convenience in order to easily access the associated output’s Manual Out-
put and Heater Range parameters using the Direct Operation keys. Refer to
section 4.2.1.1 for details on Direct Operation keys.
Summary of Contents for 350
Page 4: ...Model 350 Temperature Controller ...
Page 6: ......
Page 14: ...Model 350 Temperature Controller ...
Page 28: ...14 cHAPTER 1 Introduction Model 350 Temperature Controller ...
Page 53: ...Examples of PID control 2 13 4 ManualOutput 39 www lakeshore com FIGURE 2 4 ...
Page 58: ...44 cHAPTER 2 Cooling System Design and Temperature Control Model 350 Temperature Controller ...
Page 118: ...104 cHAPTER 5 Advanced Operation Model 350 Temperature Controller ...
Page 178: ...164 cHAPTER 7 Options and Accessories Model 350 Temperature Controller ...
Page 192: ...178 cHAPTER 8 Service Model 350 Temperature Controller ...