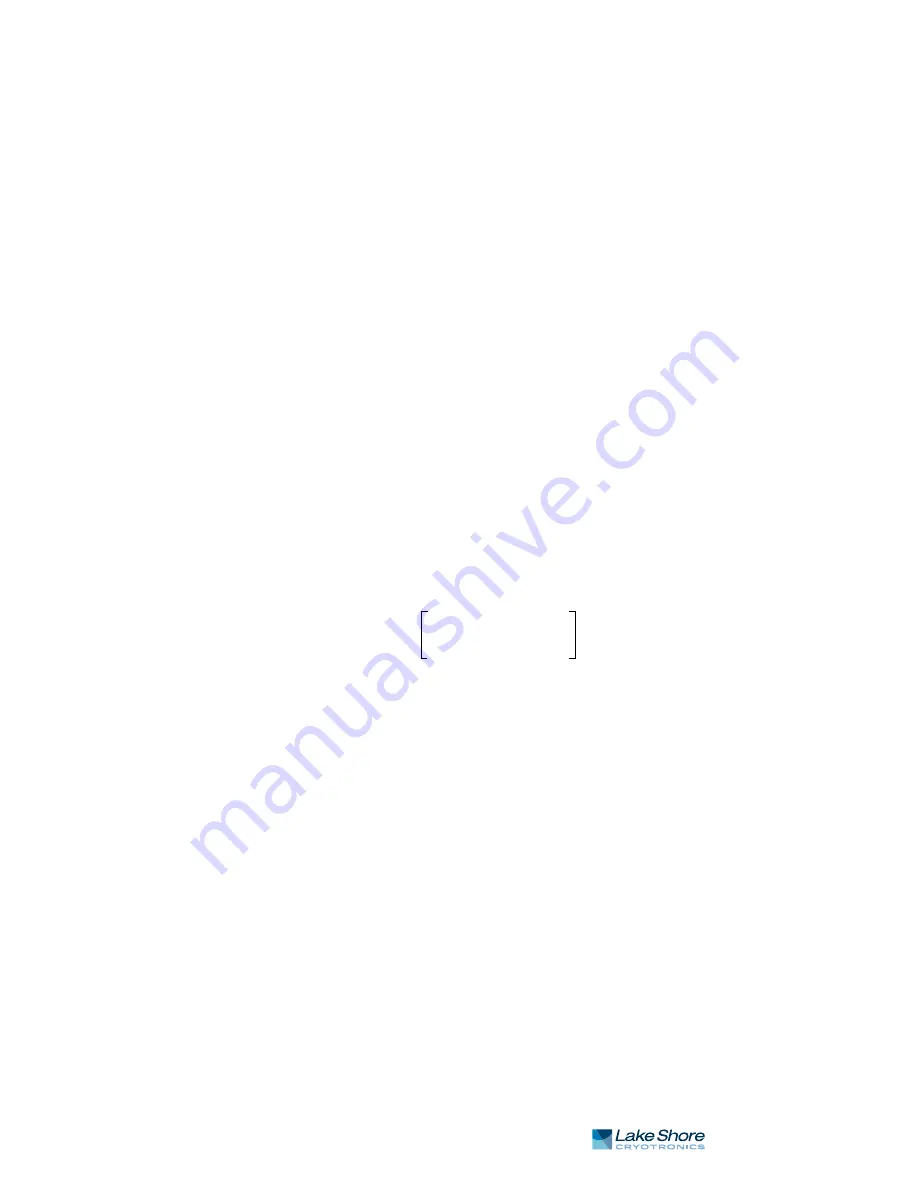
2.12.5 System Non-Linearity
37
|
www.lakeshore.com
2.12.5 System
Non-Linearity
Because of nonlinearities, a system controlling well at one temperature may not con-
trol well at another temperature. While nonlinearities exist in all temperature control
systems, they are most evident at cryogenic temperatures. When the operating tem-
perature changes the behavior of the control loop, the controller must be retuned. As
an example, a thermal mass acts differently at different temperatures. The specific
heat of the load material is a major factor in thermal mass. The specific heat of
materials like copper change as much as three orders of magnitude when cooled from
100 K to 10 K. Changes in cooling power and sensor sensitivity are also sources
of nonlinearity.
The cooling power of most cooling sources also changes with load temperature. This
is very important when operating at temperatures near the highest or lowest tem-
perature that a system can reach. Nonlinearities within a few degrees of these high
and low temperatures make it very difficult to configure them for stable control. If dif-
ficulty is encountered, it is recommended to gain experience with the system at tem-
peratures several degrees away from the limit and gradually approach it in small
steps.
Keep an eye on temperature sensitivity. Sensitivity not only affects control stability,
but it also contributes to the overall control system gain. The large changes in sensi-
tivity that make some sensors so useful may make it necessary to retune the control
loop more often.
2.13 PID Control
For closed-loop operation, the Model 350 temperature controller uses an algorithm
called PID control. The control equation for the PID algorithm has three variable
terms: proportional (P), integral (I), and derivative (D). See FIGURE 2-4. Changing
these variables for best control of a system is called tuning. The PID equation in the
Model 350 is:
Heater Output =
P e I e
+
dt D
+
de
dt
------
where the error (e) is defined as: e = Setpoint – Feedback Reading.
Proportional is discussed in section 2.13.1. Integral is discussed in section 2.13.2.
Derivative is discussed in section 2.13.3. Finally, the manual heater output is dis-
cussed in section 2.13.4.
2.13.1 Proportional (P)
The Proportional term, also called gain, must have a value greater than 0 for the con-
trol loop to operate. The value of the proportional term is multiplied by the error (e)
which is defined as the difference between the setpoint and feedback temperatures,
to generate the proportional contribution to the output: Output (P) = Pe. If propor-
tional is acting alone, with no integral, there must always be an error or the output
will go to 0. A great deal must be known about the load, sensor, and controller to com-
pute a proportional setting (P). Most often, the proportional setting is determined by
trial and error. The proportional setting is part of the overall control loop gain, and so
are the heater range and cooling power. The proportional setting will need to change
if either of these change.
2.13.2 Integral (I)
In the control loop, the integral term, also called reset, looks at error over time to build
the integral contribution to the output:
Output (I) =
PI e
t
d
Summary of Contents for 350
Page 4: ...Model 350 Temperature Controller ...
Page 6: ......
Page 14: ...Model 350 Temperature Controller ...
Page 28: ...14 cHAPTER 1 Introduction Model 350 Temperature Controller ...
Page 53: ...Examples of PID control 2 13 4 ManualOutput 39 www lakeshore com FIGURE 2 4 ...
Page 58: ...44 cHAPTER 2 Cooling System Design and Temperature Control Model 350 Temperature Controller ...
Page 118: ...104 cHAPTER 5 Advanced Operation Model 350 Temperature Controller ...
Page 178: ...164 cHAPTER 7 Options and Accessories Model 350 Temperature Controller ...
Page 192: ...178 cHAPTER 8 Service Model 350 Temperature Controller ...