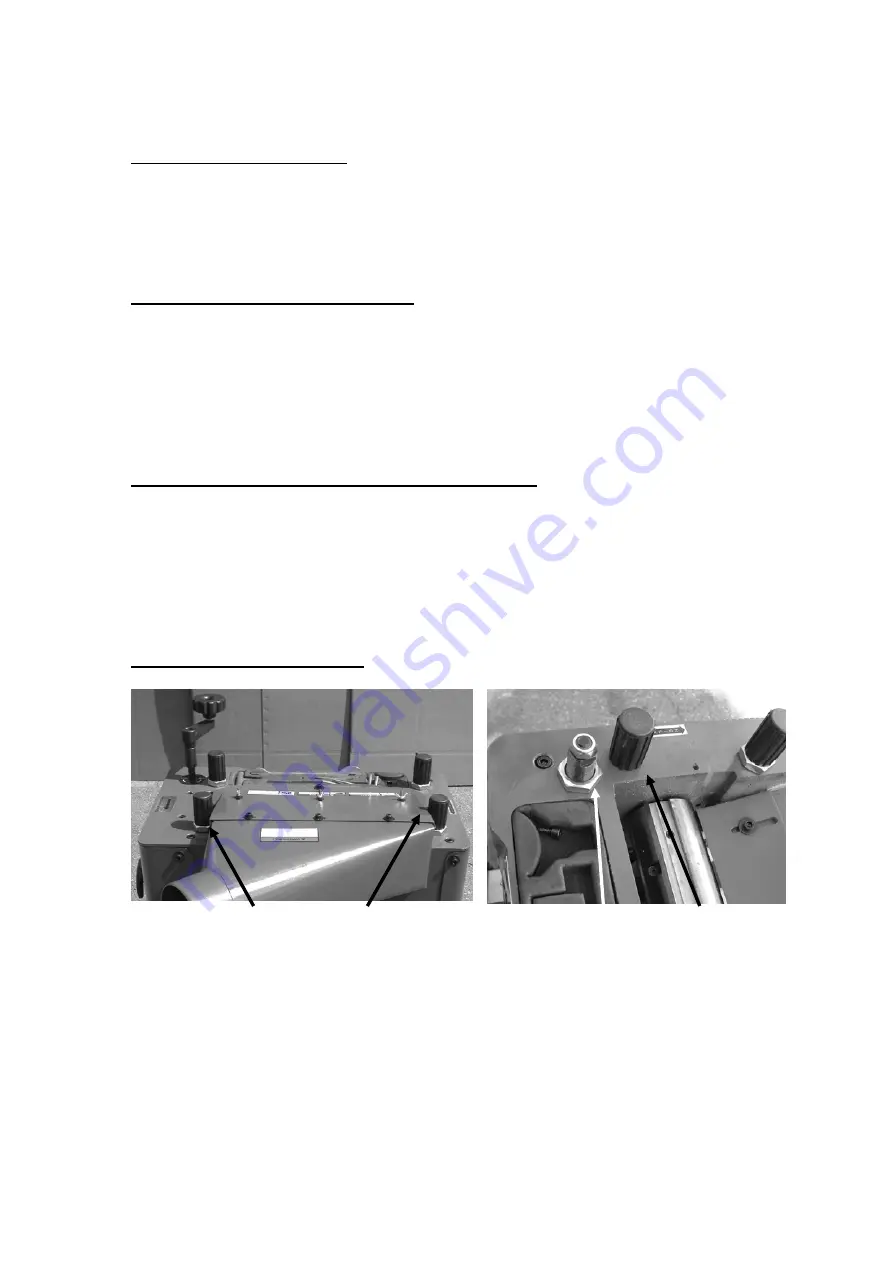
21
Adjusting the feed rollers.
The table rollers come factory set 1/8" below the cutter head to suit the planer
function. When moulding, the feed rollers have to be adjusted to suit the job. It is not
possible to be accurate in determining the feed roller height, as this will depend on
the profile that is being used. A good rule of thumb is to set the rollers 1/4" below the
cutter head and fine tune as required.
Checking the height of the rollers.
1.
Place a piece of hardwood on the table.
2.
Bring the table up until it just touches the in- and out-feed rollers. Note the height
reading.
3.
Bring the table up until it just touches the cutter blade (the rollers are spring
loaded and will move up). Note the height.
4.
The difference between the two readings is the distance the rollers are lower than
the cutter blade.
Checking that the rollers are parallel to the table.
1.
Place a piece of parallel hardwood approximately 1-inch wide on the table under
the in-feed roller at one end.
2.
Bring the table up until the wood just touches the roller.
3.
Move the wood to the other side under the same roller and check that it just
touches the roller.
4.
If there is a difference, the roller height should be adjusted.
5.
Repeat for the other roller.
Adjusting the roller heights.
Roller height adjusters
Lock nut Cap
1.
Unscrew the caps and remove.
2.
Loosen the lock nut.
3.
The threaded shaft has flats to suit the wrench supplied. Adjust the shaft to suit
the adjustment required.
4.
Tighten the lock nut and replace the cap.
Note.
There is a nut on the top of the threaded shaft. Do not loosen the nut, as this
adjusts the spring pressure and is factory set.
Summary of Contents for MPL1301-0130
Page 2: ......
Page 9: ...9 Parts of the planer moulder 6 7 1 2 3 4 5 9 8 10 11 12...
Page 27: ...27 Electrical drawing...
Page 28: ...28 Exploded view drawings...
Page 29: ...29...
Page 30: ...30...