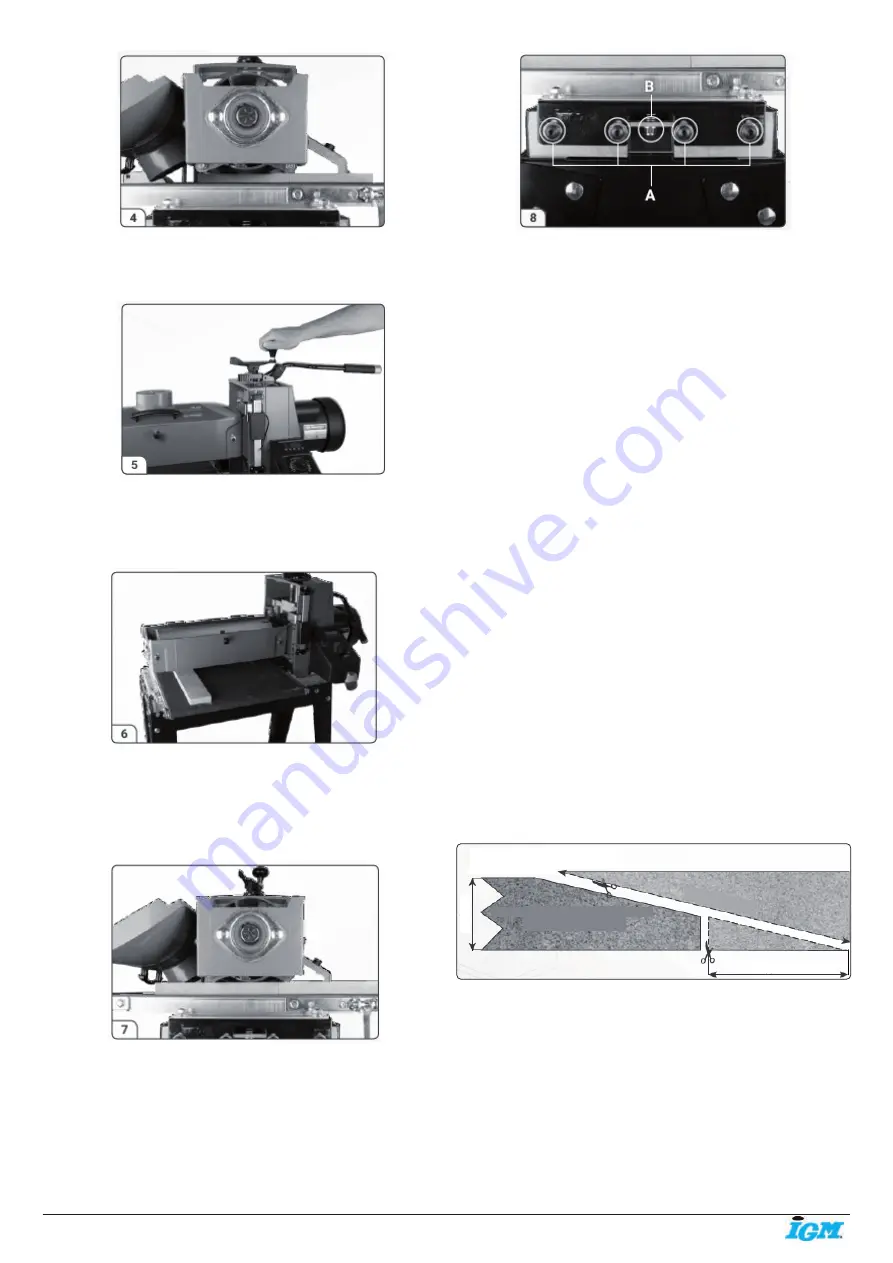
-7-
www.igmtools.com
5. Raise the head of the sander by rotating the height adjustment handle up
exactly one full turn.
6. After the height has been adjusted move the piece of wood over to the
outboard side (left) and lower the head by turning the handle down exactly
one full turn until the DRO thickness matches the noted thickness from
step #4.
7. Check the height of the drum in relation to the piece of wood. It the
drum is aligned it will just make contact with the wood as it did on the
inboard side. If you cannot turn the handle one full turn, or if there is a
gap between the drum and the wood, proceed to the following alignment
procedure
8. If the drum is not parallel, loosen the 4 socket head screws (A) along
the outboard (left) side of the conveyor belt and raise or lower the
conveyor with the adjustment nut (B) to achieve parallel alignment. Then
tighten the 4 socket head screws.
Connecting Dust Collection
Dust collection is necessary for the drum sander. The sander comes
equipped with a 100 mm (4”) diameter dust exhaust port at the top of
the cover. Make sure that the minimum dust requirements are sufficient.
To attach to your collection system, install 100 mm (4”) hose from your
collector. The minimum recommended dust collector capacities is 1000
m³/h. For best results, follow the recommendations of the manufacturer
of your dust collector. When connecting dust collector straight pipe is
preferred because it is the least restrictive for airflow. If straight pipe is not
possible Y’s and elbows are preferred because they are less restrictive to
airflow than T’s.
Note:
Some applications will require more dust collection than the
recommended minimum.
Power and Electrical Safety
11. Make sure that your power supply is adequate (230 V, circuit breaker
16 A, rating C (16/1/C))). After the dust collection system is in place and
the drum alignment is checked your machine is ready to be powered up
and operated.
Abrasive Selection Guide
To attach the abrasive to the drum, follow the procedure below.
Grit Common Application
36 GRIT - Abrasive planing, surfacing rough-sawn boards, maximum
stock or glue removal
60 GRIT - Surfacing and dimensioning boards, trueing warped boards
80 GRIT - Light dimensioning, removal of planer ripples
100 GRIT - Light surfacing, removal of planer ripples
120 GRIT - Light surfacing, minimal stock removal
150 GRIT - Finish sanding, minimal stock removal
180 - GRIT Finish sanding only, not for stock removal
220 GRIT - Finish sanding only, not for stock removal
6.2 Installing and Wrapping Abrasives
Accurate attachment of the abrasive to the drum is critical to achieving
the machine top performance. Abrasive strips do not have to be pre-
measured. The end of the roll is first tapered and attached to the outboard
(left) side of the drum. Then the strip is wrapped around the drum. The
second taper is made for attachment to the inboard (right) side of the
drum.
Note:
Pre-cut abrasives have been factory tapered to the specific width of
your drum. If you are cutting your own abrasive, use the wrap that came
on the drum as a template (abrasive side up).
Installing and Wrapping Abrasives (continued)
UNPLUG THE MACHINE FROM THE POWER SOURCE!
1. Start on the left (outboard) side of the drum. Squeeze the clip lever and
insert the tapered end of the paper into the fastener so that it uses most of
the width of the slot. Release the clip lever to securely hold the abrasive.
Drum width: 406 mm (16“)
Tip-to-tip: 2 463 mm (97“)
Abrasive ready to install: 2 311 mm (91“)
Approximately 76 mm (3“)
76 mm (3“)
400 mm (15-3/4“)
TAPERED END OF THE
ABRASIVE