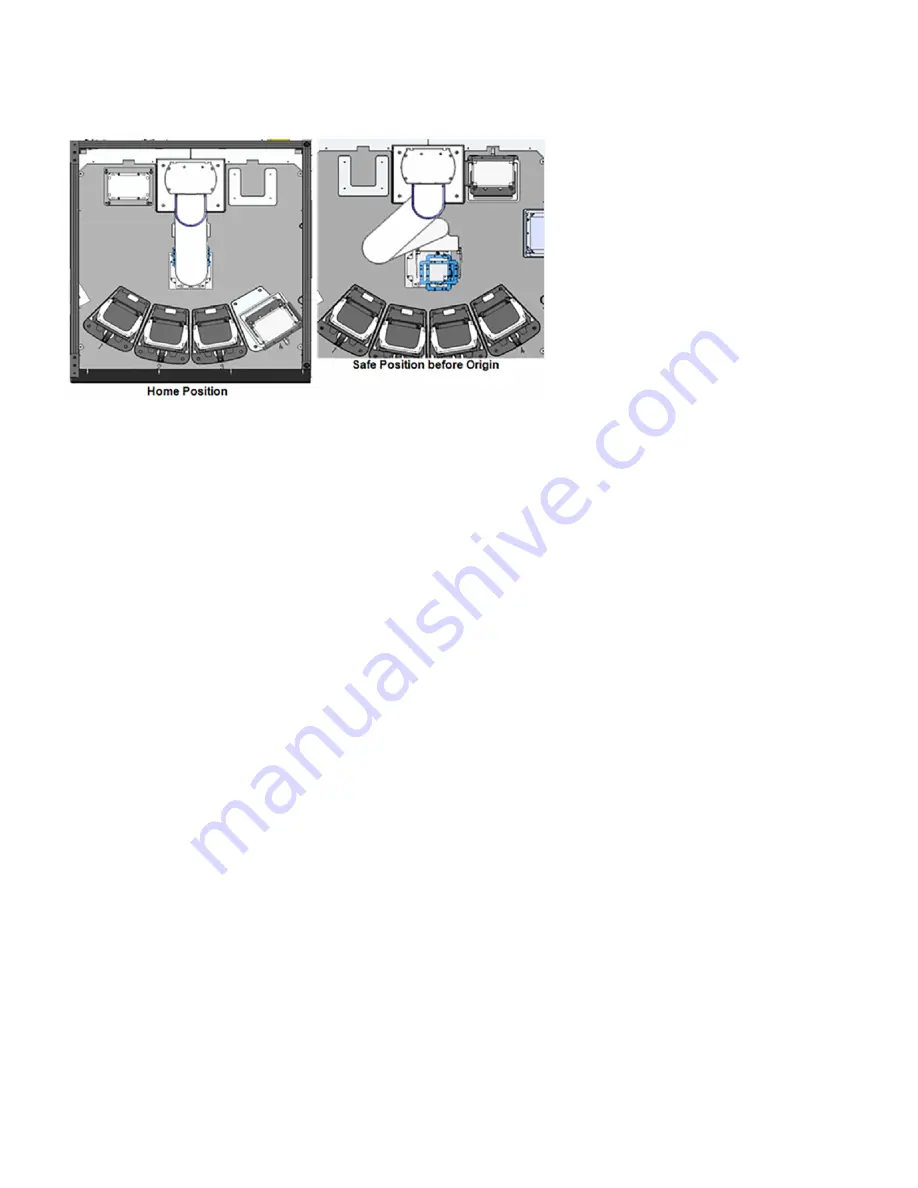
Figure 69: Move Robot/Gripper Arm To Safe Position
4. Make sure that all
ESTOP
buttons in the system are disengaged.
5. Return all components back to their locations and close all doors.
6. Reset the E-Stop safety relay by pressing the
Reset
button, which is located between the main
ESTOP
button and the
Run/Teach
key. This button changes to blue when it is active (in an E-Stop state).
7. Reinitialize all devices by clicking the
Initialize Devices
button on the Tempo Control Panel
Alarms
Tab.
8. Resolve error messages. There may be several error messages that result from pressing the
ESTOP
button or from the
original problem that required the emergency stop. The Possible Actions are:
a.
Reset errors and restart the job
- Clears any errors associated with the current job (scheduled task) and reissues
the job. You can use this to retry a scheduled action.
b.
Mark job as complete and continue
- Clears any errors associated with the current job, marks the job as completed,
and initiates the next scheduled action. You can use this to ignore an error and continue on with the remainder of a
protocol.
c.
Mark job as error and continue
- Saves error to the Run Time Errors LIst and intiates the next scheduled action. You
can use this to flag a specific job error for follow-up and continue with the remainder of the protocol.
d.
Mark job as error and stop
- Saves the error to the Run Time Errors List, archives all plates that are ot in their
original or final locations, and stops the protocol. You can resume the protocol from this point without editing (for
example, remapping plates, editing pick lists), and restarting.
e.
Mark job as error and abort
- Saves error to the Run Time Errors List, archives all plates that are not in their original
or final locations, and executes an emergency shutdown. You can resume the protocol from this point without
reinitializing the system, editing, and restarting.
70
PN | 001-15357
USER GUIDE | Access™ Dual Robot System
Recovering From An Emergency Shutdown