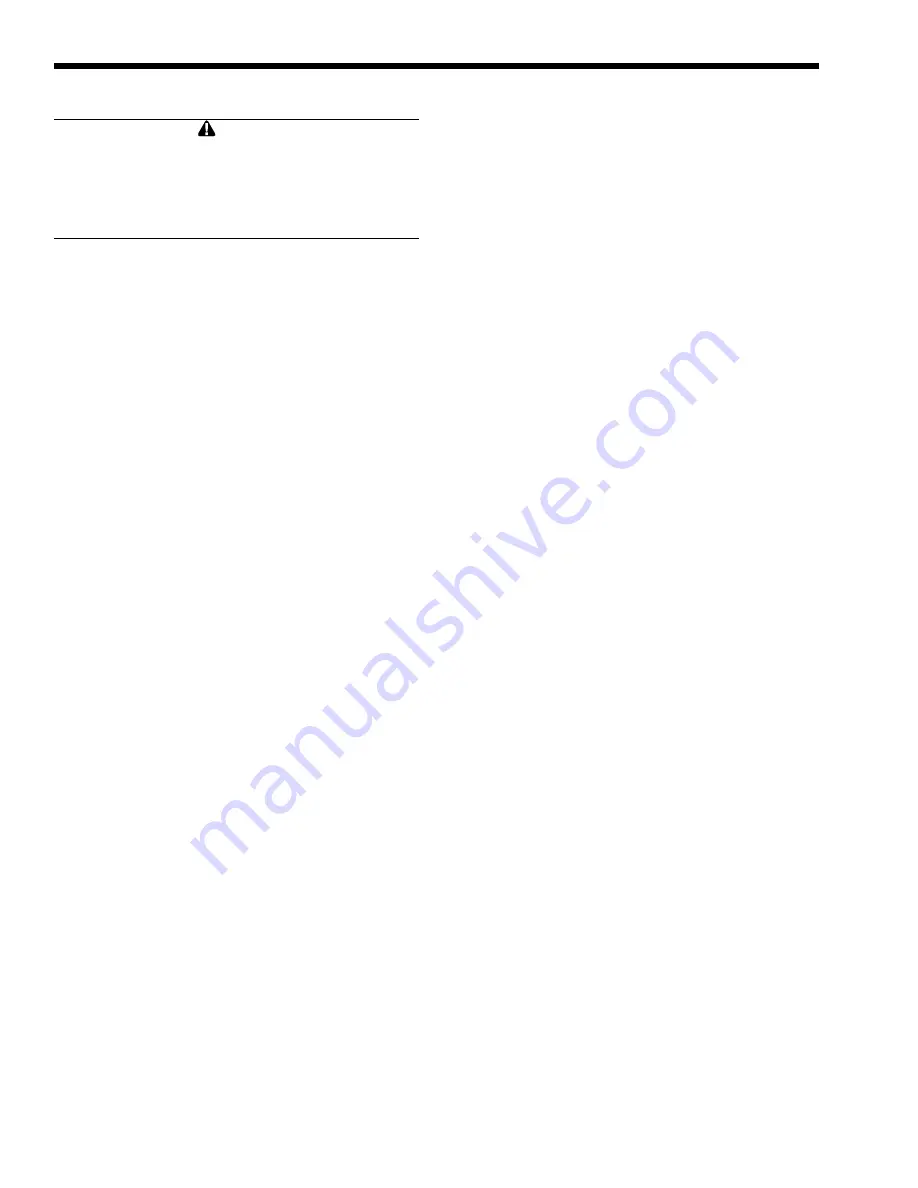
LAARS Heating Systems
Page 20
9.
NOTE: While the heat exchanger is out of the
unit, inspect the firewall refractory insulation.
Replace if necessary.
10.
Inspect the inside of the copper tubes for scale
buildup. Scale can build up on the inner surface
of the heat exchanger tubes, which can restrict
water flow. If the tubes show signs of scaling,
clean the internal surface. Laars offers a tube
cleaning kit part number R0010000.
11.
Reassemble in the reverse order, and check
appliance operation after start-up.
NOTE: The Warranty does not cover damage
caused by lack of required maintenance, lack of
water flow, or improper operating practices.
SECTION 8.
Trouble Shooting
8.1 Resolving Lockouts
There are many causes of lockouts. The three
most common causes are: (1) inadequate gas supply,
(2) poor combustion, (3) ignitor failure.
1.
Inadequate gas supply: Before proceeding,
ensure that the gas supply has not been shutoff or
the LP tank (LP boilers) is not empty. Then,
restart the boiler and observe the operational
cycle. After a 15-second fan pre-purge, the
ignitor will heat up for 20 seconds, and then the
unit will light. If it does not, check the gas
supply pressure to the appliance, after resetting
the appliance and attempting another start-up.
The gas pressure to the appliance must be above
5" W.C. (1.2kPa) throughout the entire start-up
cycle. If it is not, correct the supply problem
(check gas valves or supply piping). If the supply
pressure is adequate, consult the factory for
assistance.
2.
Poor Combustion: Poor combustion should be
suspected if there is a strong flue gas odor. The
odor may result from an improper gas/air ratio
(high or low O
2
or CO
2
). Pennant appliances
operate best with 45% excess air (8% CO
2
on
natural gas, 9.2% CO
2
on LP). Check the CO
2
of
the appliance and adjust if necessary.
3.
Ignitor failure: If the boiler goes through a
normal start cycle but combustion does not
occur, and the gas pressure is at least 5" w.c.,
ignitor failure may be the cause. Check the
ignitor by unplugging it, allowing it to cool to
room temperature, and measuring the ignitor
resistance. It should be 50-80 ohms. If the
resistance is not 50-80 ohms, replace the ignitor.
If the resistance is correct, reset the boiler and
check for 120 VAC at the ignitor plug during the
start cycle. If there is no voltage, replace the
faulty ignitor wire harness or the ignition control.
7.2.13 Heat Exchanger Coil
Caution
Black carbon soot buildup on a dirty heat exchanger
can be ignited by a random spark or flame. To
prevent this from happening, dampen the soot
deposits with a wet brush or fine water spray before
servicing the heat exchanger.
The Pennant has a pre-mixed burner system.
These systems provide the burners with sufficient air
for complete combustion, and black carbon sooting is
seldom experienced. If sooting is suspected, view
ports for inspection of the heat exchanger are provided
on both sides of the heater. They are located below the
headers, and are accessed by opening the small round
cover that is attached by one screw. In the unlikely
event that there is a buildup of black carbon soot or
other debris on the heat exchanger, clean per the
following:
1.
Disconnect the electrical supply to the unit.
2.
Turn off the gas supply by closing the manual
gas valve on the heater.
3.
Disconnect and remove the wires, conduit and
sensors from all components that are attached to
the inlet/outlet header.
4.
Isolate the heat exchanger from the water supply.
5.
Disconnect the header flanges from the inlet and
outlet.
6.
Allow the heat exchanger to drain. Remove the
front cover(s). Remove the venting and remove the
top, by removing the screws that attach the top to
the side panels. Remove the side panels. Remove
the front lower panels sealing the combustion area.
To remove the gas train, disconnect the unions
located above the intermediate pan and the field
installed union located outside the cabinet, and pull
up, bringing the union end connectors through the
grommets in the intermediate pan. To remove the
intermediate pan, remove the slide out control
assembly and blower(s) to reveal the screws.
Remove the screws holding the intermediate pan,
and lift up to remove it. The heat exchanger has
integral metal sections attached, which connect to
the frame of the boiler. Locate and remove the
screws along the front, rear and bottom of the
integral metal sections, and remove the heat
exchanger and metal sections by lifting up. On the
larger appliances, a center heat exchanger support
must be unbolted before it can be removed.
7.
Remove the heat exchanger from the unit.
NOTE:
The heat exchangers are heavy and will
require two people to remove to avoid personal injury.
8.
Clean the heat exchanger: A light accumulation
of soot or corrosion on the outside of the heat
exchanger can be easily removed. Use a wire
brush to remove loose soot and scale from the
heat exchanger. Do not use water or compressed
air for cleaning.
Summary of Contents for Pennant PNCP 1000
Page 28: ...LAARS Heating Systems Page 28 Figure 9 Sheet Metal Components...
Page 29: ...Pennant Pool Heater Page 29 Figure 10 Internal Components...
Page 32: ...LAARS Heating Systems Page 32 Figure 13 Pennant 1250 2000 Ladder Diagram...
Page 33: ...Pennant Pool Heater Page 33 Figure 14 Pennant 500 1000 Wiring Schematic...
Page 34: ...LAARS Heating Systems Page 34 Figure 15 Pennant 1250 2000 Wiring Schematic...
Page 35: ...Pennant Pool Heater Page 35 Figure 16 Field Wiring PNCP 500 1000...