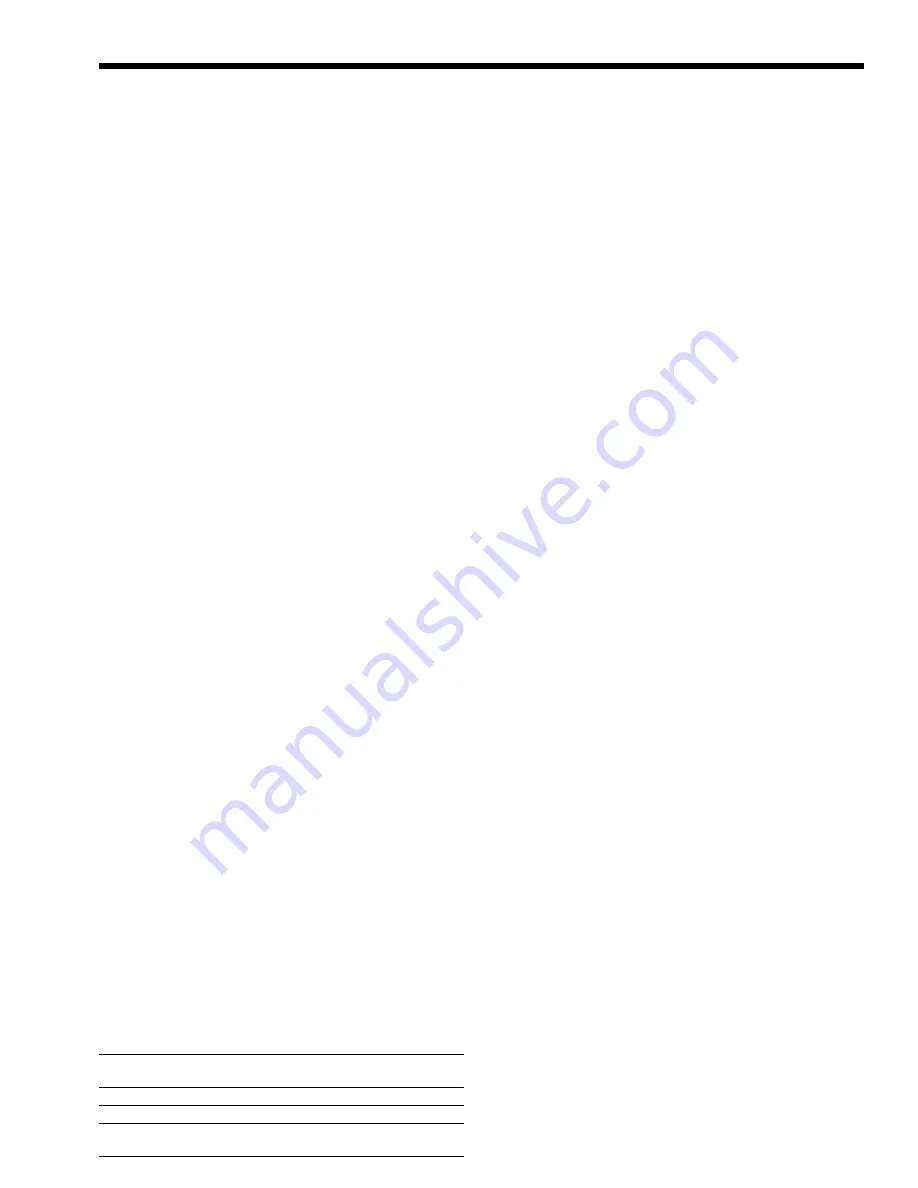
Pennant Pool Heater
Page 17
3.
Switch off the main electrical disconnect switch.
4.
Close all manual gas valves.
5.
If freezing is anticipated, drain the Pennant and
be sure to also protect piping connected to the
Pennant from freezing.
This step to be performed by a qualified service person.
6.5 Backwash Switch Operation
Pennant Pool Heaters are equipped with a filter
backwash switch, which is located above the main
power switch. The switch is intended to provide a
means by which the heater can be safely shut down for
pool filter service, without causing nuisance tripping
of the heater high limit.
This switch is internally wired in series with the
Other Interlocks terminals, and will interrupt the call
for heat signal when open. Please note that when the
backwash switch is active the heater “Service” light
will be illuminated.
To place the heater into backwash mode proceed
as follows:
1.
Turn the backwash switch down to the “Filter
Backwash Mode” position.
2.
Wait for the heater outlet temperature to drop
down to a temperature equal to the pool water
return temperature.
3.
Turn the main power switch off.
Pool filter servicing may now proceed normally.
After completion of the filter servicing, place the
heater back into service as follows:
1.
Turn the main power switch on.
2.
Allow time for the pump to turn on, and purge
air from the heater.
3.
Turn the backwash switch up to the “Normal”
position.
The service light will turn out, and the heater
will resume normal operation. Please note that if the
heater is equipped with a low water cut off there will
be a brief delay while the LWCO completes a self-
check.
6.6 Spring and Fall Operation
Stand-by Service
Turn the thermostat down to approximately 70°F
(21°C). This will prevent the pool and surrounding
ground from becoming chilled and permit the pool to
be raised to swimming temperature in a shorter length
of time.
Do Not Operate
below 60°F (16°C).
6.7 Winter Operation
Complete Shutdown
1.
See Section 6.4
2.
If the heater is not protected from freezing
temperatures, it should be
completely drained
before the first frost.
Drain the heater by
removing the plug at the end of the inlet/outlet
header casting. Also, remove the small plug at
the bottom of the pump housing. Do not replace
either plug until the time that refilling is desired.
The heater must be level for complete draining.
When compressed air is used to blow out lines, it
is still necessary to follow these directions.
Because of the potential for electrical power
failure or pump failure, freeze protection should
never be accomplished by operating the pool
heater and the filter pump. Either of those
failures will potentially allow a freeze up and
cause damage to the heater and the attached
system.
3.
Improper use of the heater:
The Laars PNCP
pool heater is not designed for continuous use as
a “anti-freezing” device for pools. Operating the
heater at low water temperatures will damage the
heat exchanger.
6.8 To Restart the Pennant
If drained, follow Section 6.2 in this manual for
proper filling and purging.
1.
Switch off the main electrical disconnect switch.
2.
Close all manual gas valves.
3.
WAIT FIVE (5) MINUTES.
4.
Set the pool aquastat to its lowest setting.
5.
Open all manual gas valves.
6.
Reset all safety switches.
7.
Set the temperature controller to the desired
temperature setting and switch on electrical
power.
8.
Burner will go through a prepurge period and
ignitor warm-up period, followed by ignition.
6.9 Therapeutic Pools (Spas)
Therapeutic pools or “spa” pools are usually
piped and controlled so that very warm or hot water,
often with air injection, is forced at high velocity into
a confined area of a swimming pool or into a small
separate pool. For the purposes of this manual, any
application in which the water temperature is
maintained above 85°F (30°C) is considered a
spa.
SPECIAL SET-UP AND OPERATING
PROCEDURES APPLY TO SPAS.
1.
Models PNCP1000 and larger should
not
be
used for spas due to their higher temperature
rises.
2.
To ensure that the spa inlet does not exceed 104°F
(40°C), the spa filter pump must circulate water
at the minimum flow rates shown in Table 9.
NOTE:
Maximum Spa Temperature Is Assumed To Be
100°F (38°C).
HEATER
MINIMUM FILTER
MODEL
PUMP FLOW RATE
PNCP 500
240 GPM
PNCP 750
360 GPM
Table 9. Minimum Filter Pump Flow Rates For Spas.
Summary of Contents for Pennant PNCP 1000
Page 28: ...LAARS Heating Systems Page 28 Figure 9 Sheet Metal Components...
Page 29: ...Pennant Pool Heater Page 29 Figure 10 Internal Components...
Page 32: ...LAARS Heating Systems Page 32 Figure 13 Pennant 1250 2000 Ladder Diagram...
Page 33: ...Pennant Pool Heater Page 33 Figure 14 Pennant 500 1000 Wiring Schematic...
Page 34: ...LAARS Heating Systems Page 34 Figure 15 Pennant 1250 2000 Wiring Schematic...
Page 35: ...Pennant Pool Heater Page 35 Figure 16 Field Wiring PNCP 500 1000...