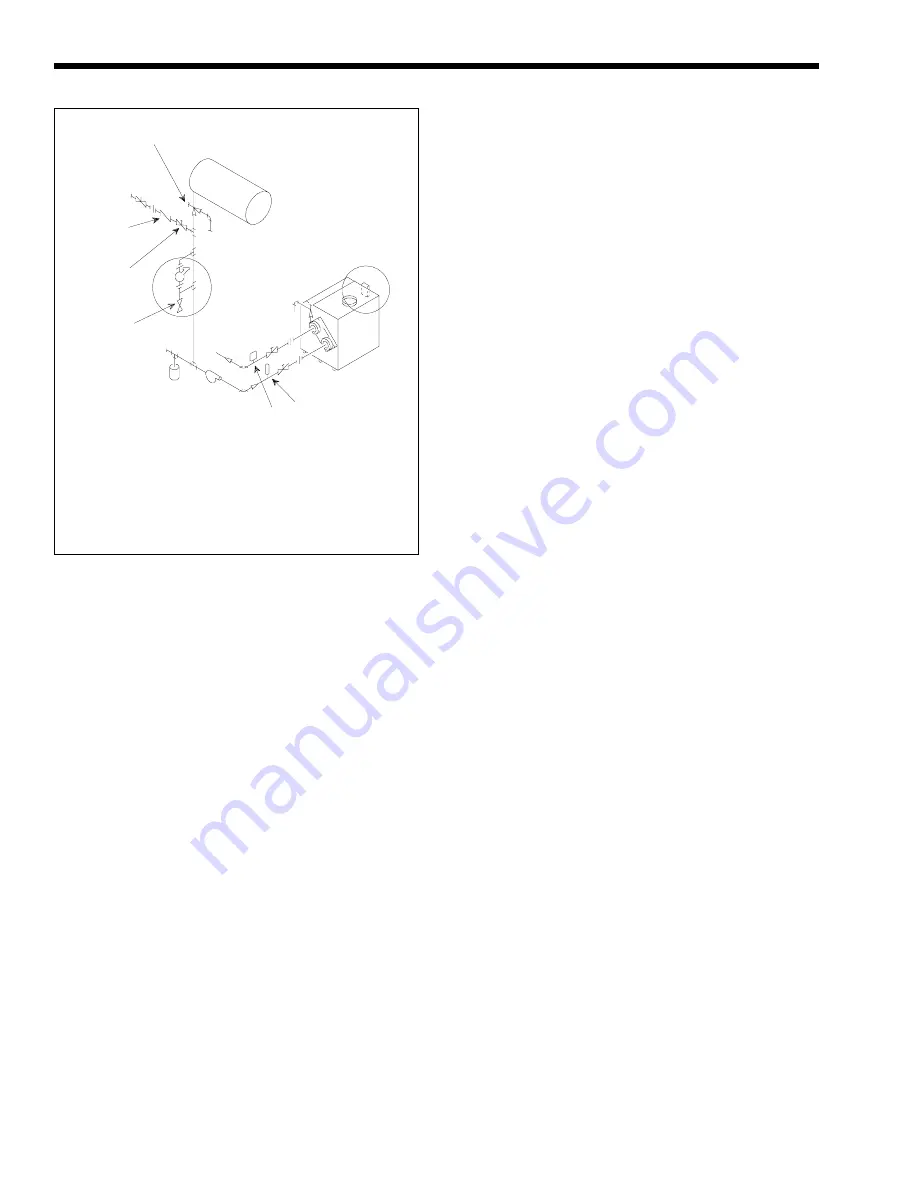
Page 10
LAARS HEATING SYSTEMS
3.
Provide a boiler installed above radiation level
with a low water cutoff device either as part of
the boiler or at the time of boiler installation (see
Figure 7).
4.
Install manual and/or automatic bleeding devices
at high points in the system to eliminate air.
Install a correctly sized expansion or
compression tank with suitable air charger and
tank drainer, as appropriate.
5.
Support the weight of all water and gas piping by
suitable hangers or floor stands.
6.
Check piping diagrams with local applicable
plumbing, heating and building safety codes.
2I. Filling The System
1.
Ensure the system is fully connected. Close all
bleeding devices and open make-up water valve.
Allow system to fill slowly.
2.
If make-up water pump is employed, adjust
pressure switch on pumping system to provide a
minimum of 12 psi (81.8 kPa) at the highest
point in the heating loop.
3.
If a water pressure regulator is provided on the
make-up water line, adjust the pressure regulator
to provide at least 12 psi (81.8 kPa) at the
highest point in the heating loop.
4.
Open bleeding devices on all radiation units at
the high points in the piping throughout the
system, unless automatic air bleeders are
provided at such points.
5.
Run system circulating pump for a minimum of
30 minutes with the boiler shut off.
6.
Open all strainers in the circulating system,
check flow switch operation, and check for
debris.
7.
Recheck all air bleeders as described in Step 4
above.
8.
Check liquid level in expansion tank. With the
system full of water and under normal operating
pressure, the level of water in the expansion tank
should not exceed 1/4 of the total, with the
balance filled with air.
9.
Start up boiler according to procedure described
in Section 3A. Operate the entire system,
including the pump, boiler, and radiation units
for one (1) hour.
10.
Recheck the water level in the expansion tank. If
the water level exceeds 1/4 of the volume of the
expansion tank, open the tank drainer and drain
to that level.
11.
Shut down the entire system and vent all
radiation units and high points in the system
piping as described in Step 4 above.
12.
Close make-up water valve and check strainer in
pressure reducing valve for sediment or debris
from the make-up water line. Reopen make-up
water valve.
13.
Check gauge for correct water pressure and also
check water level in the system. If the height
indicated above the boiler insures that water is at
the highest point in the circulating loop, then the
system is ready for operation.
14.
Within three (3) days of start-up, recheck all air
bleeders and the expansion tank as described in
Steps 4 and 8 above.
IMPORTANT:
The installer is responsible for identifying to the
owner/operator the location of all emergency
shutoff devices.
2J. Venting and Combustion Air
Information
Provisions for venting and supply of air for
venting and combustion must be done in accordance
with these instructions and applicable requirements of
the latest edition of ANSI Z223.1/NFPA 54. In
Canada, installation must be in accordance with CAN/
CGA B149.1 or .2, and applicable local codes.
There are a variety of ways to provide venting
and combustion air for the boiler (see Figure 8).
Make-Up
Water
Supply
Check
Valve
Pressure
Reducing
Valve
Blow Down
Valve
Expansion
Tank
To Drain
Method 1
To
Drain
Method 2
To
System
Strainer
Pump
Thermometer
Temperature
and Pressure
Gauge
NOTES: Select Method 1 or 2 when using low water cutoff accessory:
1. Under Method 1, the low water cutoff is furnished by Laars and shipped
as a separate item for fieldinstallation.
2. Under Method 2, electronic low water cutoff isinstalled, wired and tested
on boiler in Laars factory.
3. Preferred locaiton of system pump is shown. Compression tank must
always be on suction side of pump.
Figure 7. Boiler Piping.
Air Changer
and Tank
Drainer