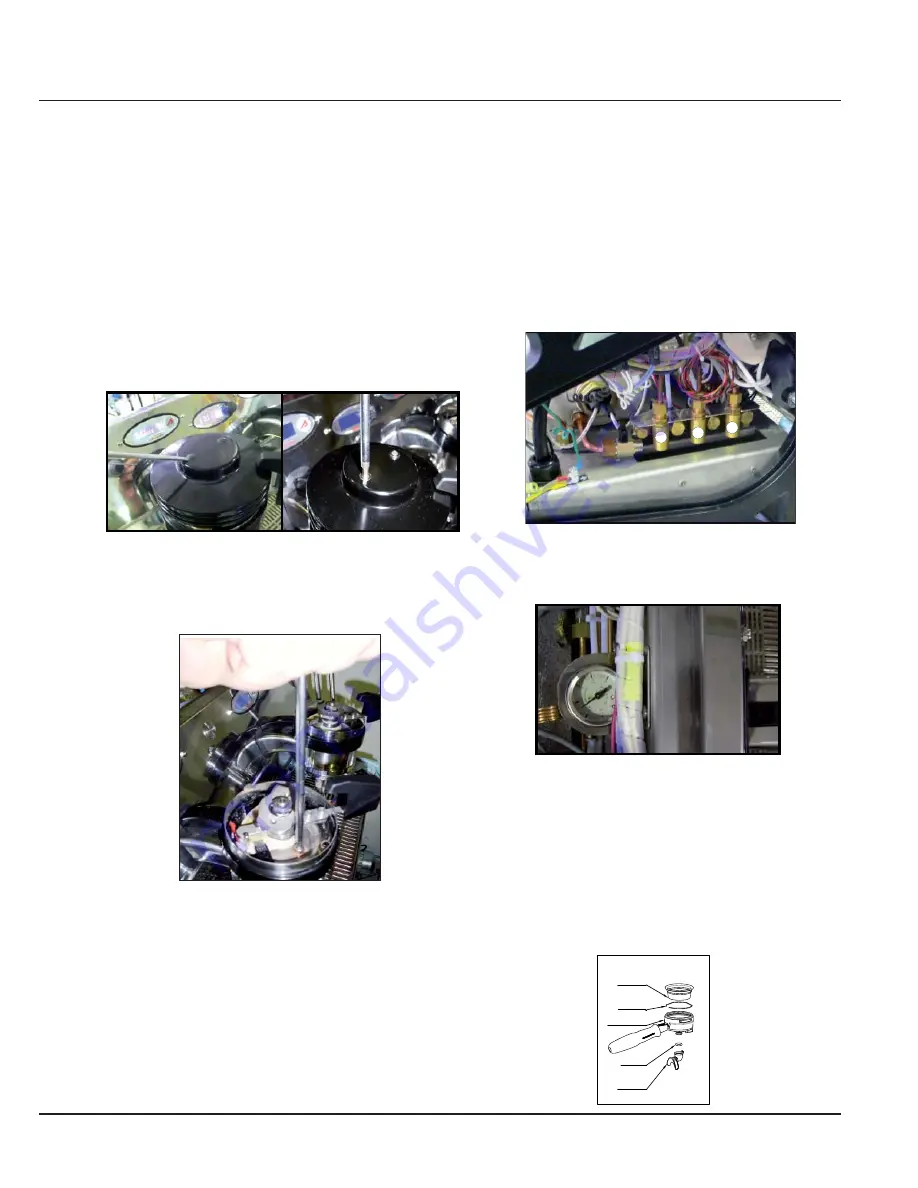
Strada EP
7
www.lamarzocco.com
V1.0
4. Operating the Espresso Machine and Preparing Coffee
1)
Starting the Espresso Machine
Filling the Boilers with Water:
Once the installation procedures have been completed, it is
necessary to
fi
ll the boiler tanks with water. Complete the
following procedure to properly
fi
ll the boiler tanks:
a) Coffee Boiler
The water
fl
ows inside the coffee boilers directly, as soon as the
water system and water
fi
lter/softener valves are opened.
Since the in
fl
ow of water will compress the air in the boiler, it
will be necessary to remove or “bleed” the air from the coffee
boilers. All air must be removed in order to completely “saturate”
the coffee boiler/group assemblies.
To remove the air from the boiler, or “bleed the groups”, it will be
necessary to remove the plastic cap and the handle from the top
of the group.
Loosen the bleed screws one at a time to allow air to escape until
water
fl
ows from below the screw head. Tighten the screw to stop
the water from
fl
owing. Over tightening can cause damage to the
sealing washer and the group cover. Repeat this procedure on
all groups.
b) Steam Boiler
Turn the main switch to position “1” or ON, then push the encoder
knob for three seconds and the automatic steam boiler level
function will be switched on, activating the auto-
fi
ll solenoid
valve and the motor pump. This will
fi
ll the steam boiler to a
predetermined level and will shut off when full.
Note:
Air inside the steam boiler may build up pressure (which
may be detected through the pressure gauge).
Once the pump stops, check the display, the message “Coffee
Boiler Filled?” should be displayed. Push the Encoder Knob to
con
fi
rm that the preceding procedures are complete.
The installation is now complete and the espresso machine
should be heating to operating temperatures.
2)
Waiting for the Espresso Machine to Heat to
Operating Temperature
During this time, it may happen that the pointer of the coffee
boiler pressure reaches as high as 14-15 bar. This may happen
anytime that the heating element is in the “on” condition. In
this case, it is necessary to adjust the expansion valve (see the
picture below about the three coffee boiler expasion valves) in
such a way that the pressure never exceeds 13.5bar.
In normal operating conditions, the coffee boiler pressure
transducer, while brewing, can read anywhere from 0-12 bar
when brewing.
GR1
GR1
GR2
GR2
GR3
GR3
The steam boiler pressure is visible through a pressure gauge
placed inside the machine, behind the control and the 1st group.
When the steam boiler reaches operating temperature, the light
on the Tea dispense button will switch on.
Filter
Basket
Basket
Spring
O-ring
Double
Spout
Portafilter
3)
Installing the Portafi lters
Install the porta
fi
lter(s) by inserting them into the group and rotate
the handle from left to right. When the porta
fi
lters are inserted
properly, you can press any of the brew buttons to start the
fl
ow
of water through the porta
fi
lter. ou should allow hot water to
pass through the porta
fi
lter(s) for a few seconds each time, in
order to pre-heat the porta
fi
lter.
Note:
It is important to leave the porta
fi
lters installed in the
espresso machine when not in use. The porta
fi
lter must remain
heated for the brew process to function correctly.