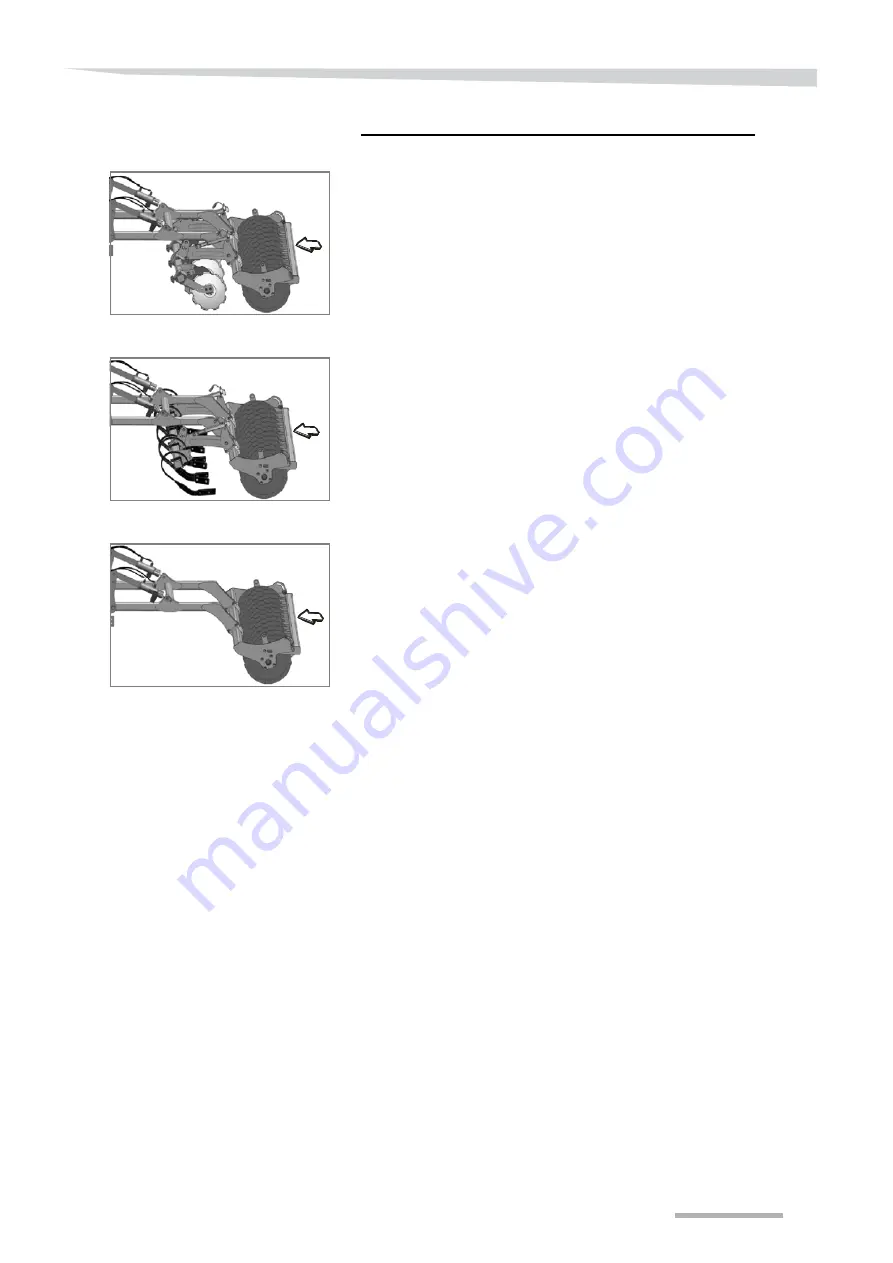
Presentation of the machine
19
There are three configurations mounted on roller arms:
Levelling discs + roller [+]
•
Working depth check by roller.
•
The levelling is performed by notched discs mounted on rubber
spring safety.
•
Compaction is performed by the rear roller.
Tines + roller [+]
•
Working depth check by roller.
•
The levelling is performed by tines on spring mounted safety
mechanisms.
•
Compaction is performed by the rear roller.
Roller only [+]
•
Working depth check and compaction by roller.