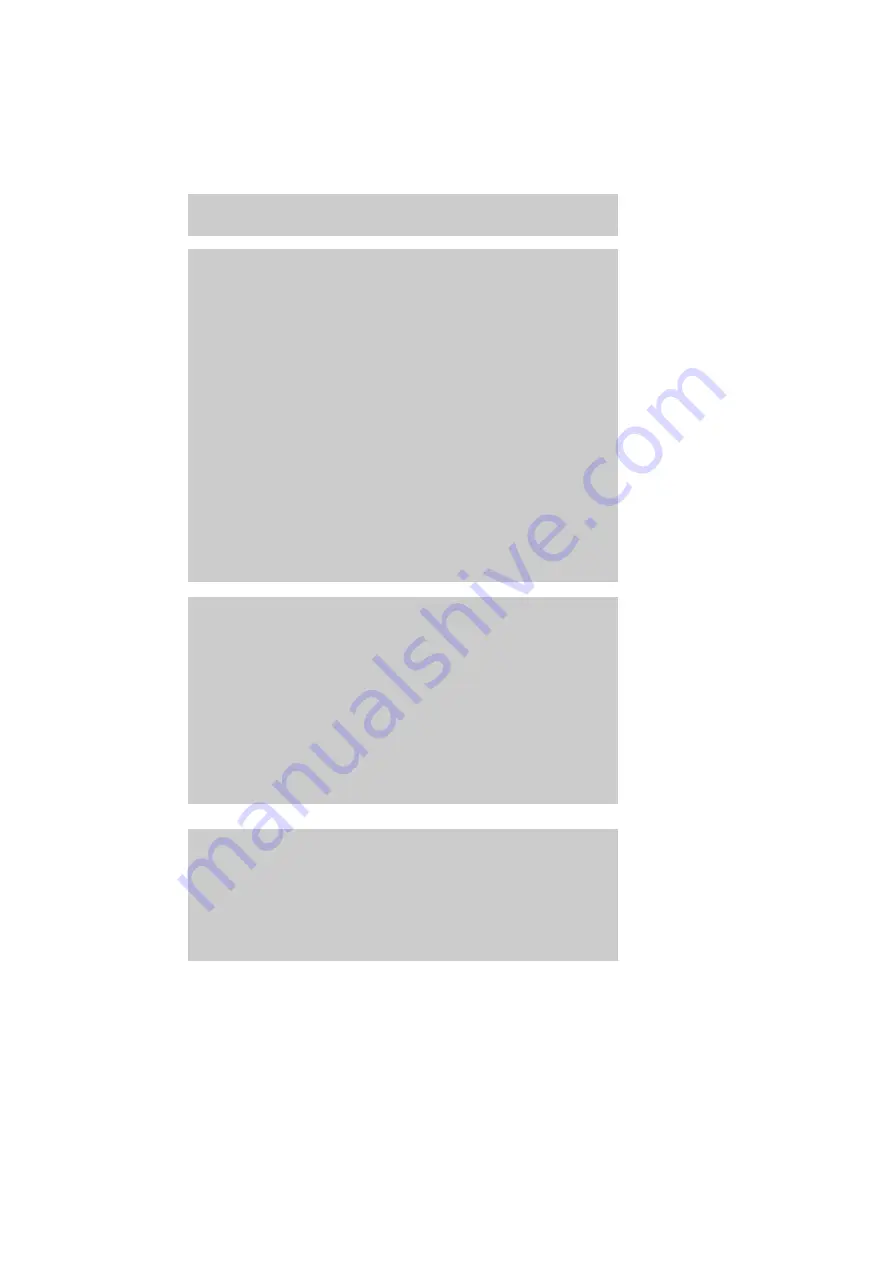
Identification of the machine
To support you as soon as possible your dealer requires several details of your machine.
Please enter the information here.
Designation
Information
plate
Dealer's
address
Manufacturer's
address
Kverneland Group Operations Norway AS retains all copyrights and rights of usage. The contents of this operating manual are subject to change
without notice. All rights reserved. The right to technical revision is reserved.
CLG-II
Kverneland Group Operations Norway AS
Kverneland Klepp
N-4355 Kvernaland
Norway
Phone
+47 5142 9000
www.kvernelandgroup.com