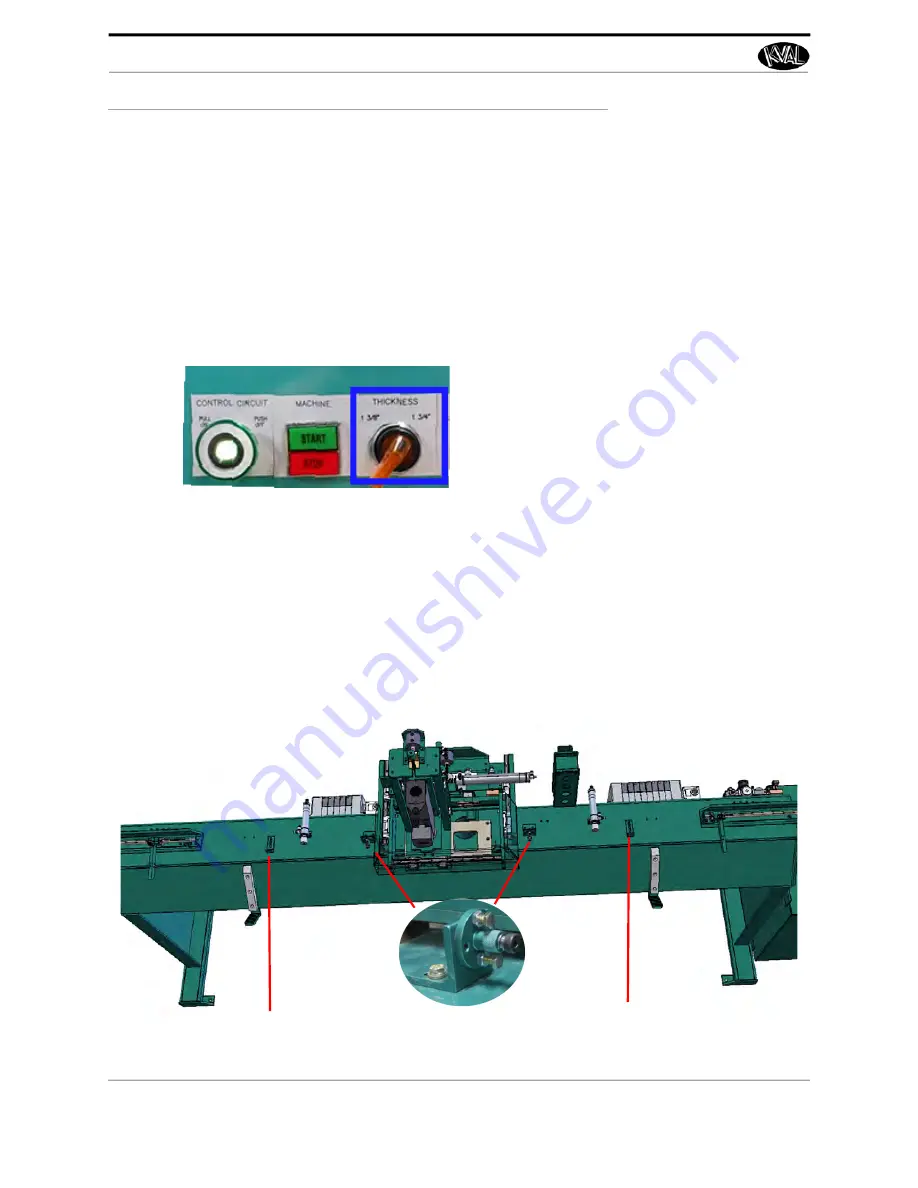
Presets for the 960-3
KVAL Operation/Service Manual
2-6
Presets for the 960-3
Before cutting a jamb, ensure the presets are completed.
Set the Thickness
The
Thickness Switch
is located on the machine
E-Box.
Set the switch the desired thickness. The
thickness values relate to an interior door or exterior door. After setting the thickness adjust the
backset.
• Interior Door equates to
1-3/8''
• Exterior Door equates to
1-3/4''
Set the Backset
After setting to the desired thickness, rotate the backset turrets and adjust stops.
• If thickness is set to
1-3/8'
', rotate both turrets to the longer bolts.
• If thickness is set to
1-3/4''
, rotate both turrets to the shorter bolts.
• If need, adjust both adjustable stops to align with the turret setting.
Tip:
Use a practice jamb placed against both turrets and adjust the two other stops to
fit tightly against the jamb.
Turrets
Adjustable Stop
Adjustable Stop
Summary of Contents for 960-3
Page 4: ...KVAL 960 3 Operation Service Manual ...
Page 28: ...Safety Sign Off Sheet 1 21 KVAL Operation Service Manual ...
Page 46: ...Description of the Light Tower KVAL Operation Service Manual 2 18 ...
Page 64: ...Appendix Collet Torque Values KVAL Operation Service Manual 3 18 ...
Page 65: ...Appendix Collet Torque Values 3 19 KVAL Operation Service Manual ...
Page 67: ...Notes ...