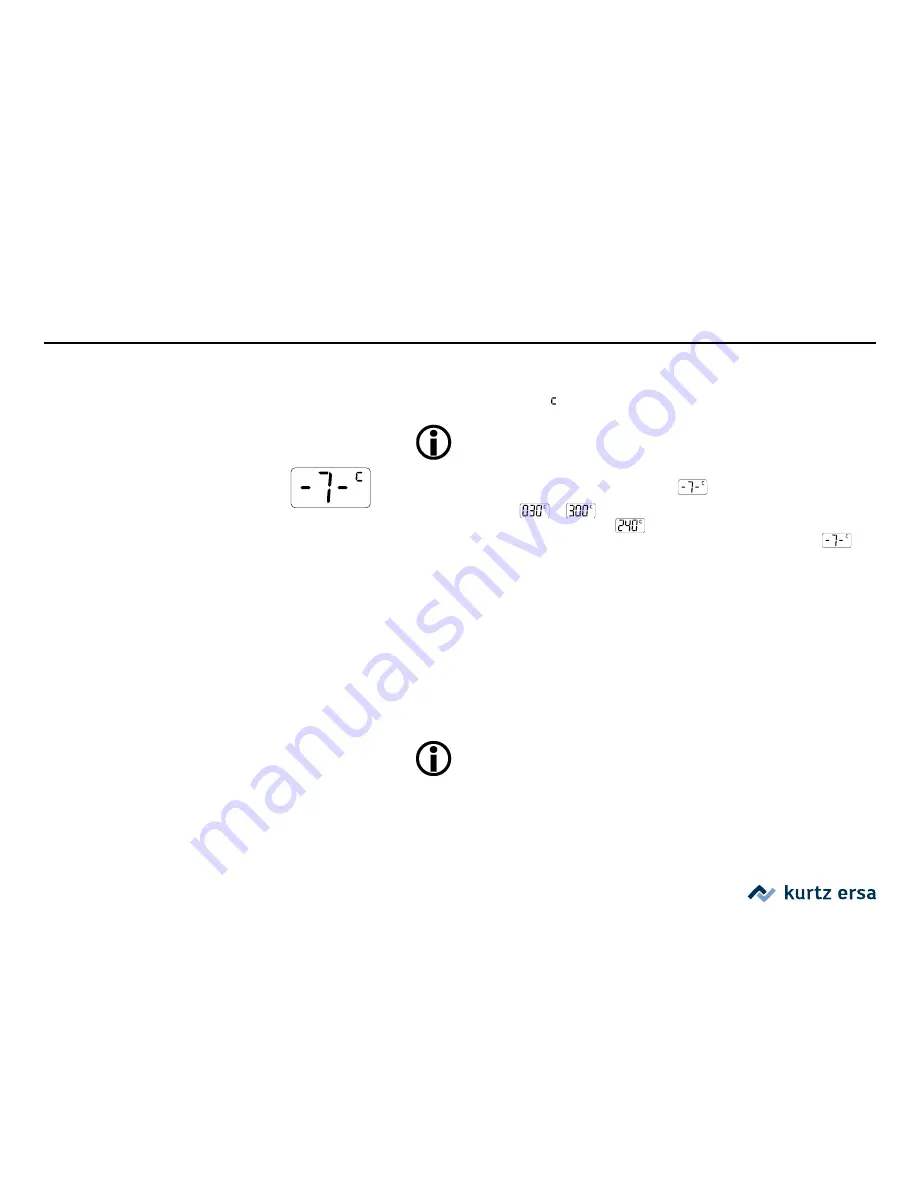
3BA00174 • 2014-02-06 • Rev. 5
HR 100 1 / 32
6.
Description of function
6.1.4.7 Temperature monitoring Hybrid Tool
Parameter [End temperature]
This function is only possible when thermocouple or IR sensor are connected,
otherwise this level cannot be accessed.
■
In this level you can set the temperature monitoring of the Hybrid Tool. Press the rotary
encoder to open the parameter [End temperature]
:
■
The setting range is
to
. Turn the rotary encoder clockwise or anti-clockwise,
until the desired value is displayed, e.g.
. Then press the rotary encoder to save the
adjusted value and to exit the parameter [End temperature]. The display shows
again.
Temperature monitoring includes two functions:
• Pure monitoring of the process temperature
• Control of the [Ramp] function
Temperature monitoring:
The thermocouple/IR sensor detects the process temperature.
If the adjusted value is exceeded, a bleep sound is emitted. When the temperature drops below
the set temperature again, another bleep will sound.
Control of the [Ramp] function:
The thermocouple/IR sensor detects the process
temperature and supplies the actual temperature value to control this function.
Special function
of the rotary encoder during the heating phase: When
the rotary encoder is pressed, the display shows the measured temperature
of the connected temperature sensor. Pressing again changes back to the
display of the heating time.