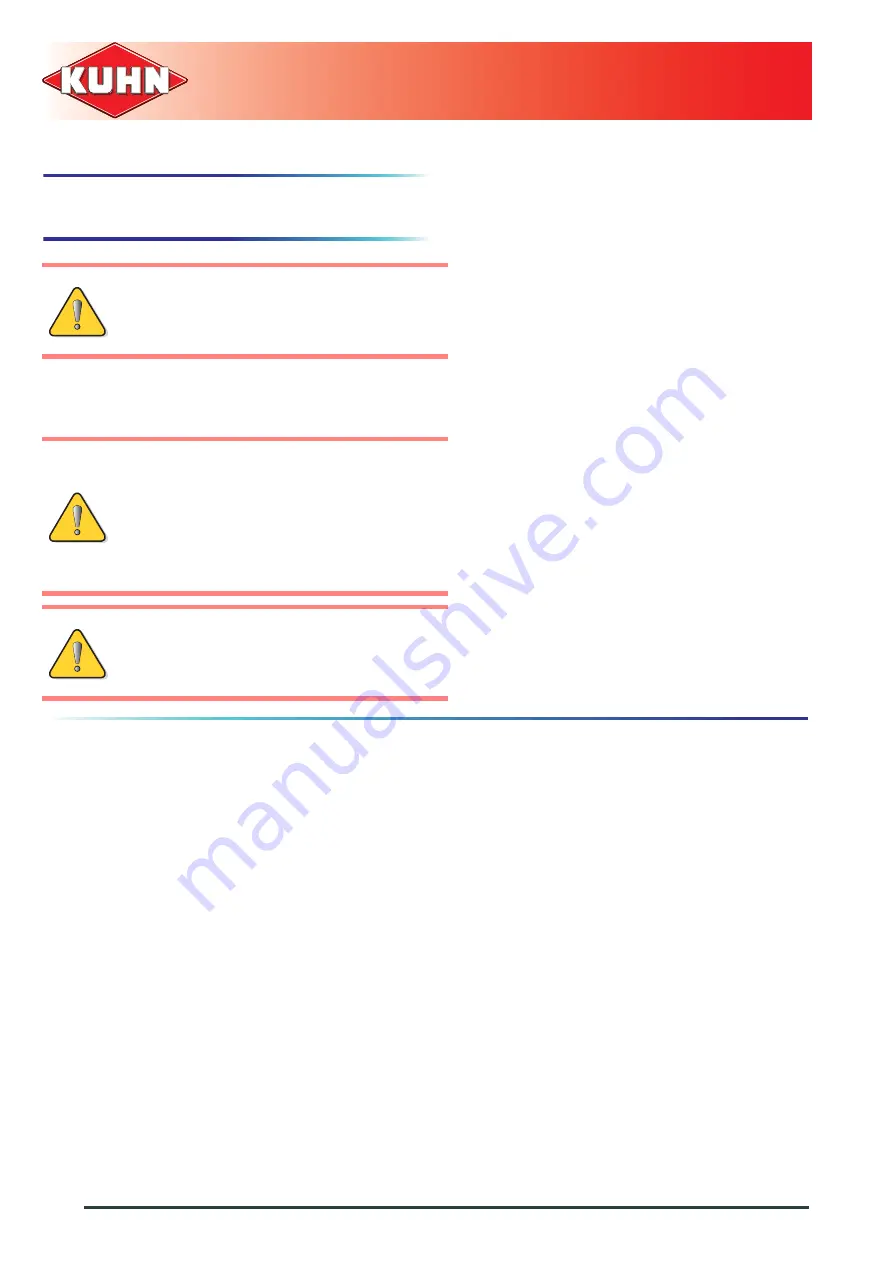
SR300
30
7. - Instructions for transport
7N021EUS_A
Wheel Rake
7.2
Conformity with the road
regulations
Check that the reflectors are clean and that the
lighting equipment is working properly before
transporting on public roads.
Before driving the machine on public roads,
ensure that the machine complies with
current highway code regulations.
Before going on public roads:
- Make sure the rake wheels and arms are
locked in the transport position.
- Make sure that the safety chain is properly
installed.
- Make sure the hitch pin is installed and
secured to prevent unexpected detaching.
Immediately replace any worn or damaged
reflectors or lights.