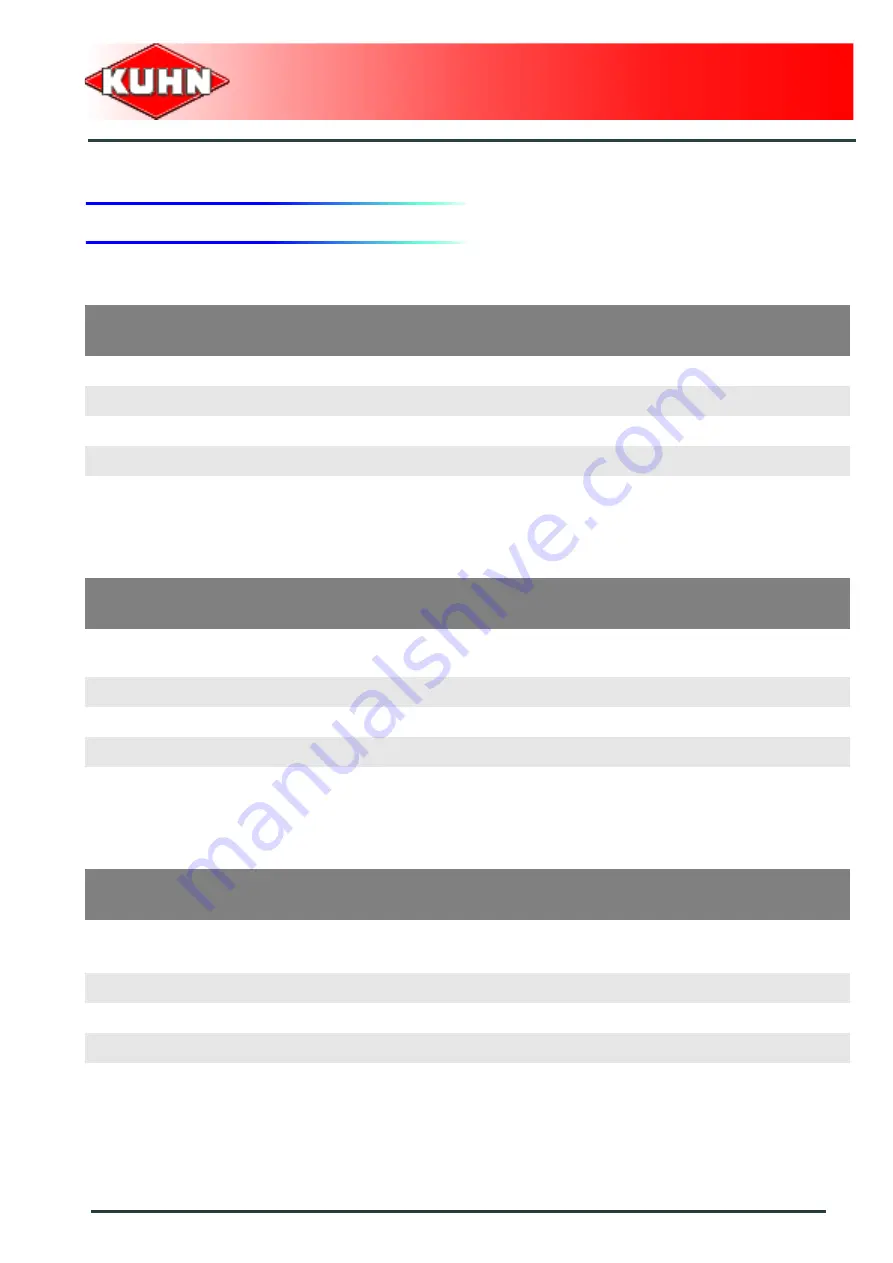
Machine specifications
Precision Seed Drills
MAXIMA 2 M
29
3. Technical specifications per model
4 row configuration
5 row configuration
6 row configuration
Distance between sowing components
70 - 75 - 80 - 90 cm ( 2’4’’ - 2’6’’ - 2’8’’ - 3’)
Width in transport position
3.45 m (11’04’’) (Maximum)
Length in transport position
2.37 m (7’9’’)
Height in transport position
2.52 m (8’3’’)
Weight
825 to 1440 kg (1819 - 3175 lb)
Distance between sowing components
55 - 60 - 65 -70 - 75 - 80 cm (1’9’’ - 2’ - 2’1’’ - 2’4’’ - 2’6’’
- 2’8’’)
Width in transport position
3.45 m (11’04’’) (Maximum)
Length in transport position
2.37 m (7’9’’)
Height in transport position
2.52 m (8’3’’)
Weight
825 to 1440 kg (1819 - 3175 lb)
Distance between sowing components
45 - 50 - 55 - 60 - 65 -70 - 75 - 80 - 95 cm
(1’6’’ - 1’8’’ - 1’9’’ - 2’ - 2’1’’ - 2’4’’ - 2’6’’ - 2’8’’ - 3’1’’)
Width in transport position
4.40 m (14’05’’) (Maximum)
Length in transport position
2.37 m (7’9’’)
Height in transport position
2.52 m (8’3’’)
Weight
825 to 1440 kg (1819 - 3175 lb)
Summary of Contents for MAXIMA 2 M
Page 2: ......
Page 212: ...Precision Seed Drills 210 MAXIMA 2 M Appendix T Axle loads Tractor only...
Page 214: ...Precision Seed Drills 212 MAXIMA 2 M Limited warranty Limited warranty...
Page 215: ...Limited warranty Precision Seed Drills MAXIMA 2 M 213...
Page 216: ......
Page 217: ......
Page 218: ......
Page 219: ......
Page 220: ......