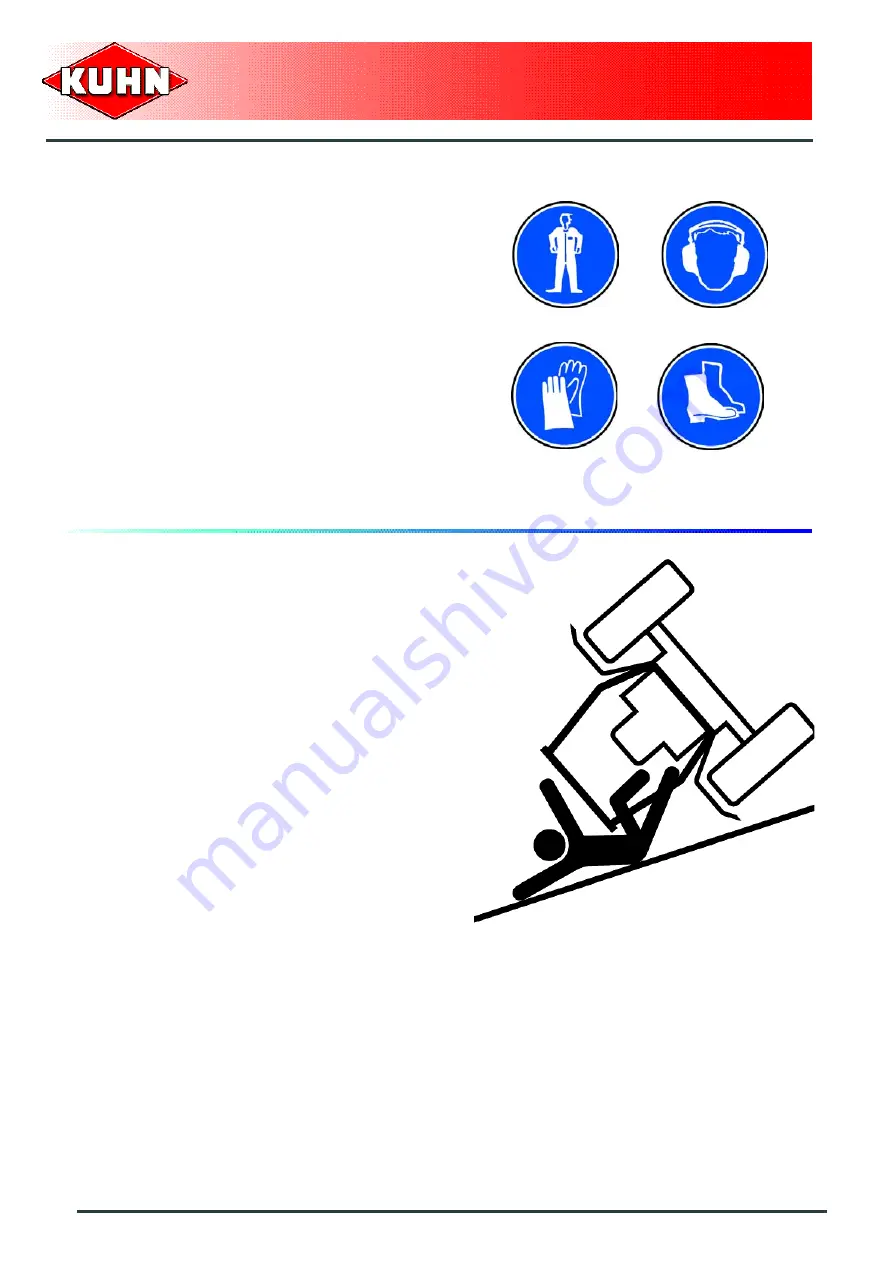
Disc mower
8
GMD883
Safety
Precautions to take before using the
machine
Do not wear loose clothing which could become caught
up in moving parts.
Wear the appropriate protective clothing for the work in
hand (gloves, shoes, goggles, helmet, ear-protectors,
etc.).
Make sure that all operating controls (ropes, cables,
rods, etc) are placed so that they cannot be set off
accidentally, risking accident or damage.
Before operating the machine, check tightness of nuts
and bolts, particularly on fixing elements (tines, forks,
blades, knives, etc). Retighten if necessary.
Before operating the machine, ensure that all the safety
guards are firmly in place and in good condition.
Immediately replace any worn or damaged guard.
Precautions when driving
Precision steering, tractor adherence, road holding and
efficient braking are influenced by the type of implement,
weight, ballast of front axle, ground or road conditions. It
is therefore of the utmost importance to be cautious in
every given situation.
Groundspeed must be adapted to ground conditions as
well as to roads and paths. Always avoid abrupt changes
of direction.
Be particularly cautious when turning corners, paying
attention to machine overhang, length, height and
weight.
Never use a narrow track tractor on very uneven or
steeply sloping ground.
Never leave the tractor seat while the machine is
operating.
Carrying people or animals on the machine when
working or in transport is strictly forbidden.
Summary of Contents for GMD883
Page 1: ...OPERATOR S MANUAL Disc mower GMD883 KN017CGB D English 03 2007...
Page 2: ......
Page 83: ...Limited warranty Disc mower GMD883 81 LIMITED WARRANTY...
Page 84: ...Disc mower 82 GMD883 Limited warranty...
Page 85: ......
Page 86: ......
Page 87: ......
Page 88: ......