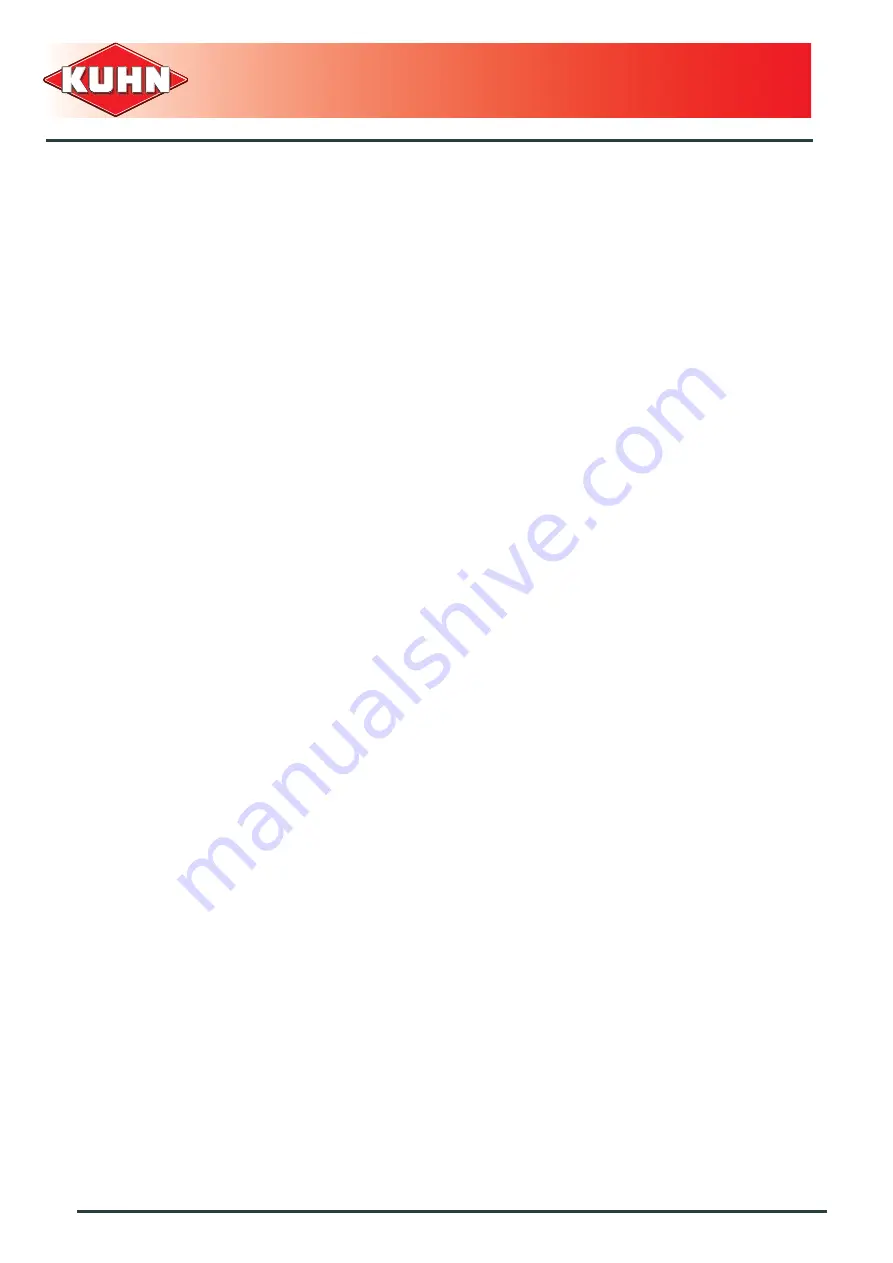
Disc mower
58
GMD602 GII
Limited warranty
■ The Limited Warranty is dependent on the strict observance of the following
conditions:
- The machine has been put in service by the dealer according to our instructions.
- The warranty/product registration form has been correctly completed by the dealer and the retail purchaser,
dated, signed by the dealer and the retail purchaser and returned to the address indicated on the
warranty/product registration form as soon as the machine had been put in service.
- The warranty claim is submitted on a KUHN warranty claim form, and is sent to the Company (preferably via
extranet - www.kuhnsa.com) within one month after the date of failure or the date of problem becoming
apparent.
- The claim must be filled in legibly by the dealer and following information must be mentioned.
● Dealer’s name and address
● Name and address of retail purchaser
● Exact type of machine
● Machine serial number
● Date of delivery to the retail purchaser
● Date of failure
● Number of hours of use or area (hectares, acres) worked
● Power of tractor used
● PTO speed (if applicable)
● Detailed description and estimated cause of the failure
● Quantity, reference number and name of the damaged parts
● Invoice number and invoicing date for replacement parts.
- The dealer has stored the damaged parts safely and labelled them clearly so that they can be recognised and
returned to the Company if requested. They must be retained until a credit note has been issued to cover the
parts. Carriage charges for the return of said parts are borne by the sender.
- The machine has been used and maintained according to the instructions in the operator’s manual. The quality
and quantity of lubricants used must always be in accordance with Company specifications.
- The safety measures mentioned in the Operator’s manual and on the machine itself have been followed, and
all the guards and protective elements, of whatever nature, have been inspected regularly and maintained in
perfect working order.
- The judgment of the Company in all case of claims under this Limited Warranty shall be final and conclusive
and the retail purchaser agrees to accept its decisions.
- If damaged parts have been returned to the Company and Warranty is refused , the dealer is allowed a period
of 1 month from the date of receiving our letter of decision to request the return of the damaged parts to the
dealer site.
■ Further conditions: limits of application and responsibility
- This Limited Warranty can not be assigned or transferred to anyone without the prior written consent of the
Company.
- Authorized KUHN Dealers have no right or authority to assume any obligation or take any decision on the
Company’s behalf, whether expressly or tacitly.
- Technical assistance given by the Company or its agents for repairing or operating equipment does not lead
to any responsibility on the Company’s behalf and cannot under any circumstances bring novation or
derogation to the conditions of the present Limited Warranty.
- The Company reserves the right to incorporate changes in its machines without prior notice and without
obligation to apply these changes to machines previously manufactured.
- Moreover, because of the constant progress in technology, no guarantee is given to the descriptions of
equipment published in any document by the Company.
- The present Limited Warranty excludes any other responsibility, whether legal or conventional, express or
implied, and there are no warranties extending beyond those defined herein.
Summary of Contents for GMD602 GII
Page 1: ...OPERATOR S MANUAL Disc mower GMD602 GII KN011FGB F English 01 2007...
Page 2: ......
Page 61: ......
Page 62: ......
Page 63: ......