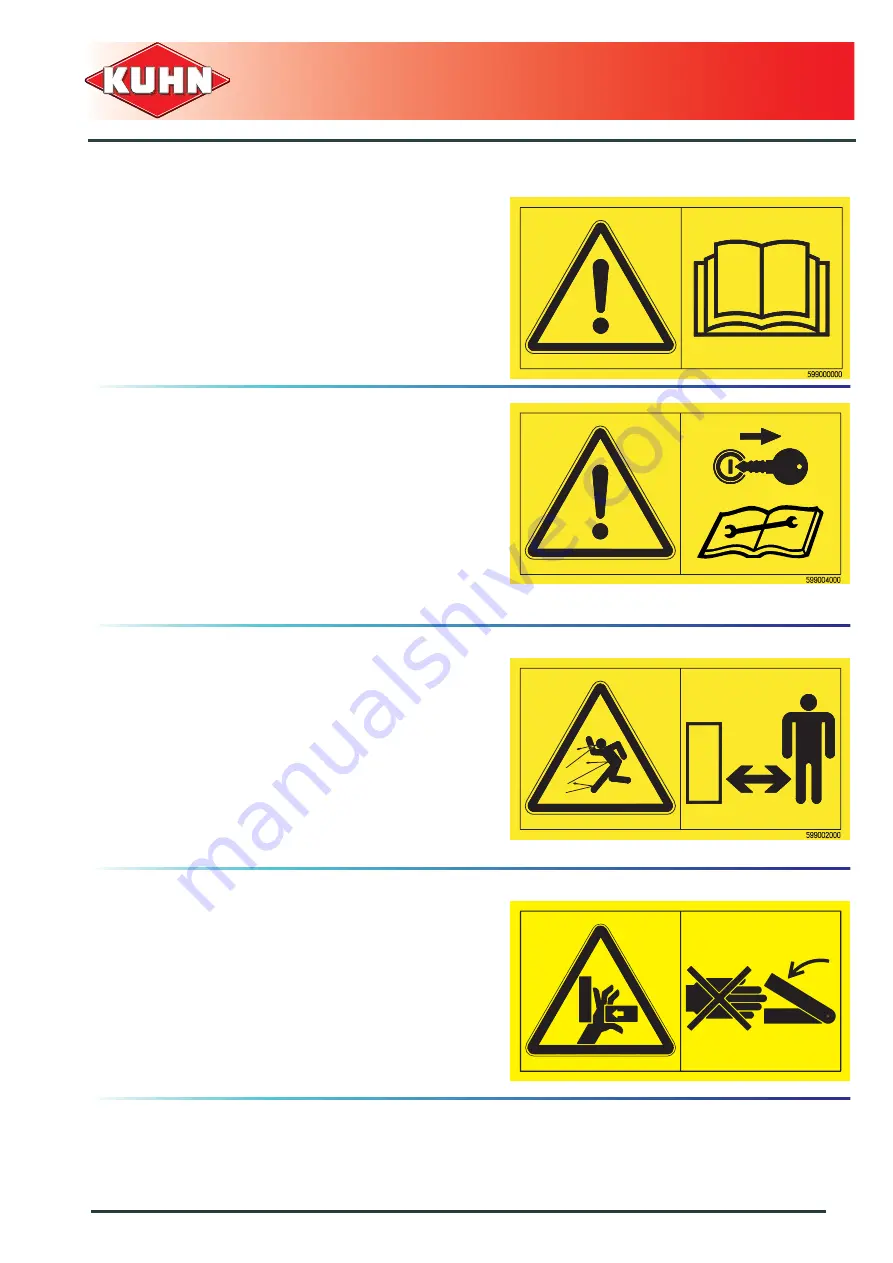
Safety
Disc mower
GMD3510-FF
21
Description of safety decals
Operating instructions (1)
The operators' manual contains all the information
necessary for using the machine safely. It is imperative
to read and comply with all instructions.
Working on the machine (2)
Before leaving the tractor or before adjusting,
maintaining or repairing the machine, disengage the
PTO drive, turn off the engine, remove ignition key and
wait until all moving parts have come to a complete stop
and apply park brake.
Projections (3)
Stones and other debris projected by the moving parts
can travel a long distance. The protection covers must
always be in position and in good condition. Always stay
at a safe distance from the machine.
Crushing area (4)
Never operate in an area where there is a crushing risk
before all moving parts have come to a complete stop.
59900300