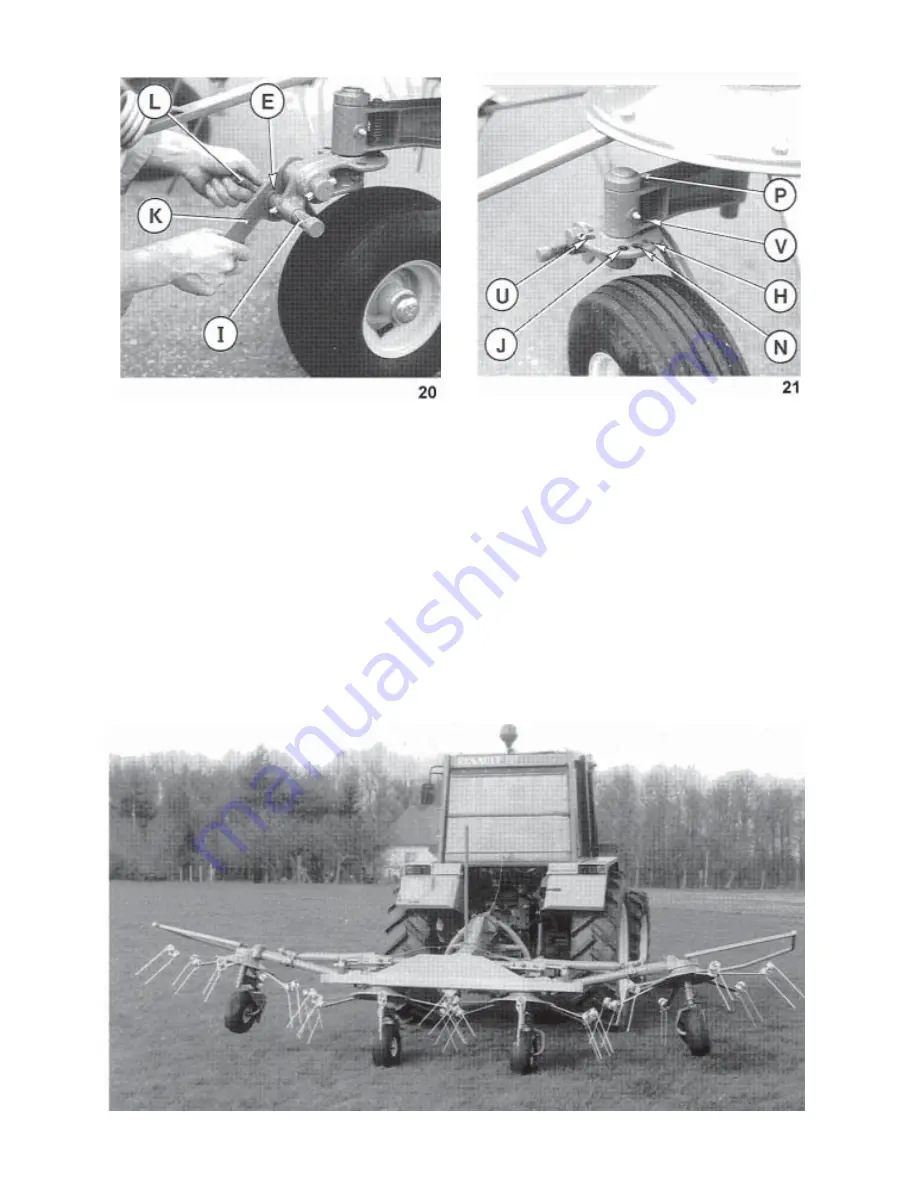
- 20 -
Adjustment of handle (L) with eccentric (E) (photo 20) is carried out as follows :
- Machine is attached to the tractor, stand in front of one of the rotors
- Pull eccentric (E) out of its housing and turn lever (L) 180° upwards or downwards
- Lift or lower handle (K) so that the eccentric (E) is in alignment with its housing and is re-engaged automatically
by return spring (I) (photo 20).
Proceed the same way on the remaining rotors.
Perfect rotor angle adjustment using tractor crank handle so that the tines lightly skim the ground at the front of
the machine.
When working along edges of fields, hedgerows, fences, etc., the oblique position is obtained by locking the
wheels in holes (H) to project the crop towards the left or holes (J) to project the crop towards the right (photo
21). Hole (N) corresponds to the regular work position (photo 21). Wheels are locked in the selected position by
means of locks (P) (photo 21). Positions (U) and (V) are never used on the
GF 5001 MHA
(photo 21).
If at the field ends the tractor does not lift the machine high enough to clear the outside rotors from the ground,
it is possible to lift the rotors slightly using the tractor hydraulic cylinders (see photo below).
Do not forget to put again the tractor 3 - point linkage in the free floating position.