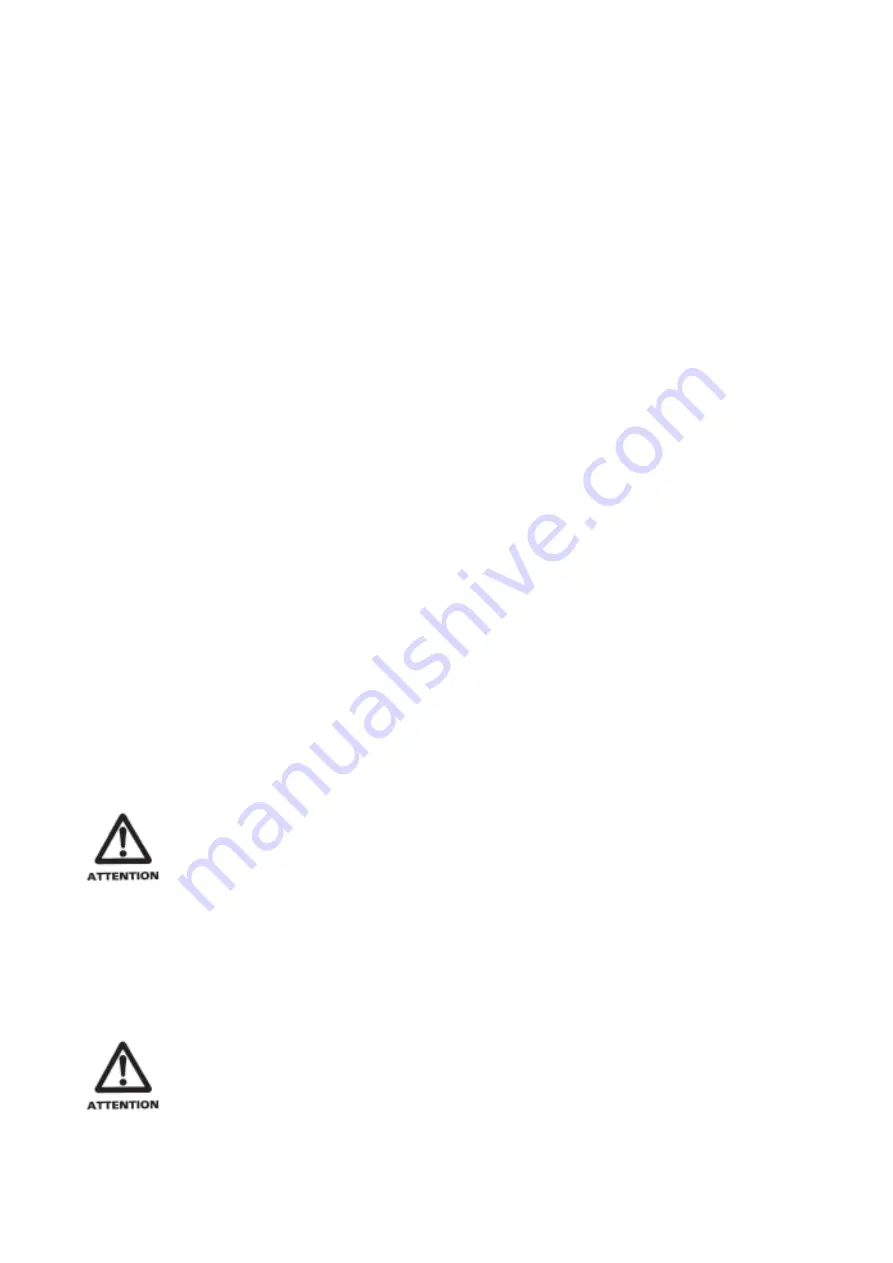
- 16 -
7. FITTING SWATH SCREEN
- Install the 4 plastic bushes (M) in both arm ends of the swath screen adjustment parallelogram (U) (photo 12).
- Fit the swath screen’s parallelogram adjustment (U) on the 2 pivot pins (V) using 2 roll pins (W) (diameter 6
x 40) and 2 flat washers (N) (diameter 30 x 40 x 1.5), inserting washers between the roll pins (W) and the
parallelogram arm (U) (photo 12).
- Install the counter nut
(I)
and the intermediary long connecting rod (J) onto the threaded rod (O), then slide the
short rod (L) into the long connecting rod (J) (photo 12A) and mount the short connecting rod yoke (L) on the rear
arm of the adjustment parallelogram (U) by means of a pin (H) and 2 roll pins (K) (diameter 5x20) (photo 12).
- Fit the swath screen (X) on the support (Y) in one of the vertical positions with 2 hexagonal screws (Z) (M 10 x
30), 2 self locking nuts (M 10) and 2 plain washers (diameter 10.4 x 24 x 4) (photo 13), the latter must be fitted
on the screws (Z) in order to be placed between the screen (X) and the support (Y).
- Now adjust the length of the connecting rod by proceeding as follows :
. make sure the machine is in transport position and the threaded insert (P) is located approx. in the middle
of the adjusting range of screw (Q) (photo 12 A),
. fold the swath screen (X) inwards (see arrow) until in contact with guard stop (R) (photo 13 A),
. rotate the intermediary long connecting rod (J) on the threaded rod (O) until mounting holes for lock pin (S)
line up. Install lock pin (S) and secure with R-clip (T) (photo 12 A),
. tighten the counter nut
(I)
(photo 12 A).
8. FITTING TINE ARMS AND TINES
- Fit tine arms (E) onto the oscillating shafts and attach using roll pins (F) (diameter 12 x 55 and diameter 7 x 55)
(photo 14). Fit the tine arms (E) onto the oscillating shafts making sure that the bent form of the arms faces
always forwards when looking in the direction of rotor rotation (see arrow on photo 14).
ATTENTION : Make sure that the roll pins are fitted 180° to each other and that the slots are facing the direction
of rotation (see drawing on photo 14).
Be sure that the mating surfaces of tine arms (E) and their shafts are clean and lightly coated
with a never seize compound.
- Fit tines (A) perpendicularly under tine arms (E) so that tines are slanting away from the direction of rotation
(see arrow on photo 14 A).
- The following items are needed to fit a tine : 1 screw (B) (M 12 x 80), 1 self-locking nut (G) (M 12) (torque
8.5 daNm / 6 ft.lbs), 1 flat washer (C) (diameter 13 x 35 x 7), 1 spring washer (F), 1 wedge (D).
Make sure all items are positioned correctly, as shown on photo 14 A.
Incorrect fitting of the tine arms and the tines can cause serious damage to the machine.
Summary of Contents for GA 6000
Page 1: ...ASSEMBLY OPERATOR S MANUAL GA 6000 GYRORAKE N 95313 E GB 10 2003...
Page 11: ...9 3 4 5 6 7 8...
Page 15: ...13 5 3 4 1 2...
Page 17: ...15 10 7 11 A 6...
Page 19: ...17 14 14A 13A R X 12A...
Page 21: ...19 16 15...
Page 23: ...21 18 20...
Page 25: ...23 22...
Page 27: ...25 24...
Page 29: ...27 29 27 G E B H T G T 32 31...
Page 31: ...29 34 33 33A 37...
Page 33: ...31 38 39 40...
Page 38: ...N O T E S...