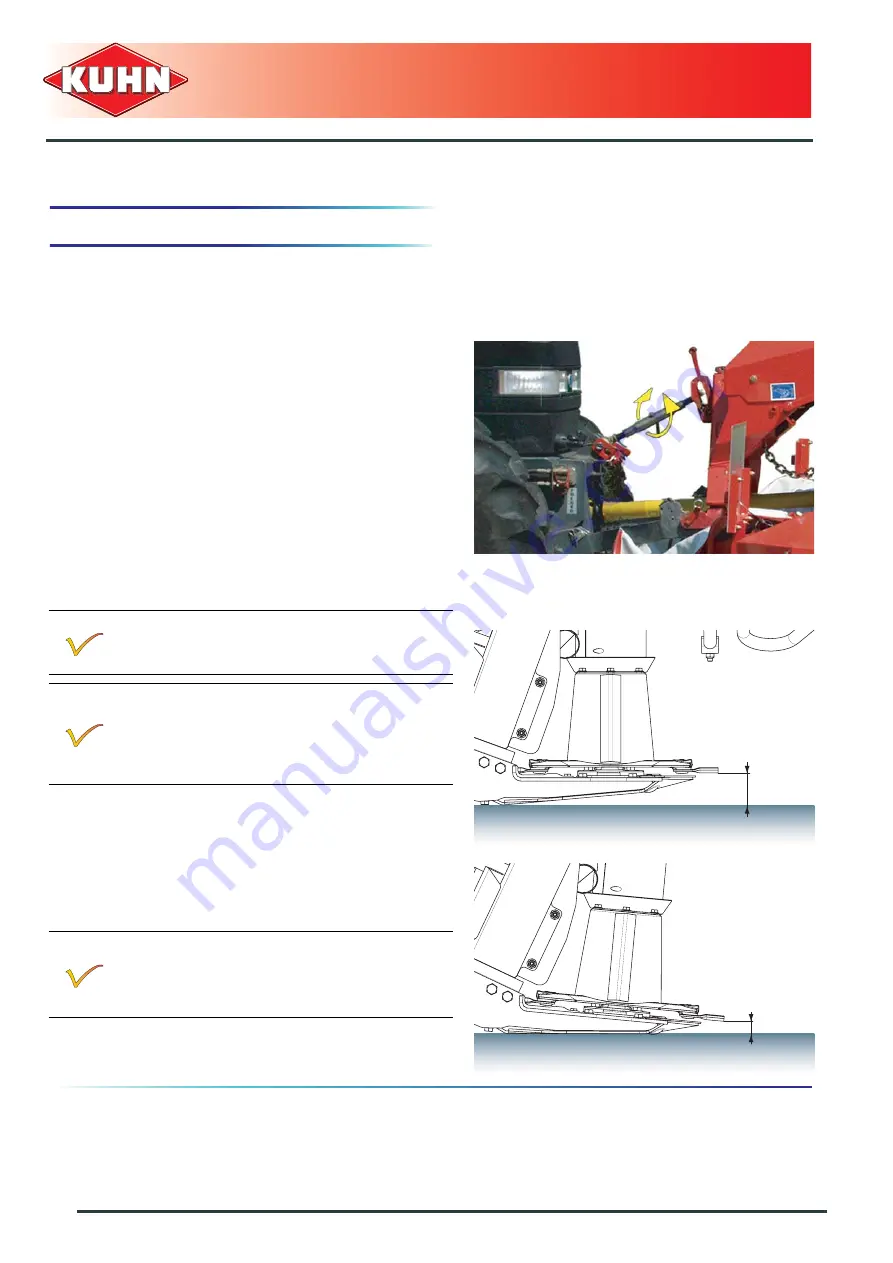
Mower conditioner
38
FC313 RF
Instructions for work
2. Adjustments in working position
Cutting height
The desired cutting height is obtained directly by
adjusting the top link length. The height can be adjusted
between 30 and 80 mm (1.1’’ - 3.1’’) depending on the
tractors.
To obtain a different cutting height:
- Place the machine in parking position.
- Remove check chains on tractor side.
- Release and lower parking stands.
- Lower tractor front linkage until frame rests on its
parking stands and the machine rests on the ground.
- Modify the top link length to alter the machine tilt
angle.
- Place the machine in working position to check cutting
height.
-
If the tractor is fitted with a hydraulic top link, the
machine tilt angle can be adjusted in working
position.
The maximum cutting height (L1 = 80 mm (3.1’’))
is obtained when the discs are parallel to the
ground.
The minimum cutting height must not be below
(L2 = 30 mm (1.1’’)).
Too low a cutting height can lead to:
- Excessive disc and knife wear.
- Crop being contaminated by soil.
-
Delay in regrowth
.
L1
L2