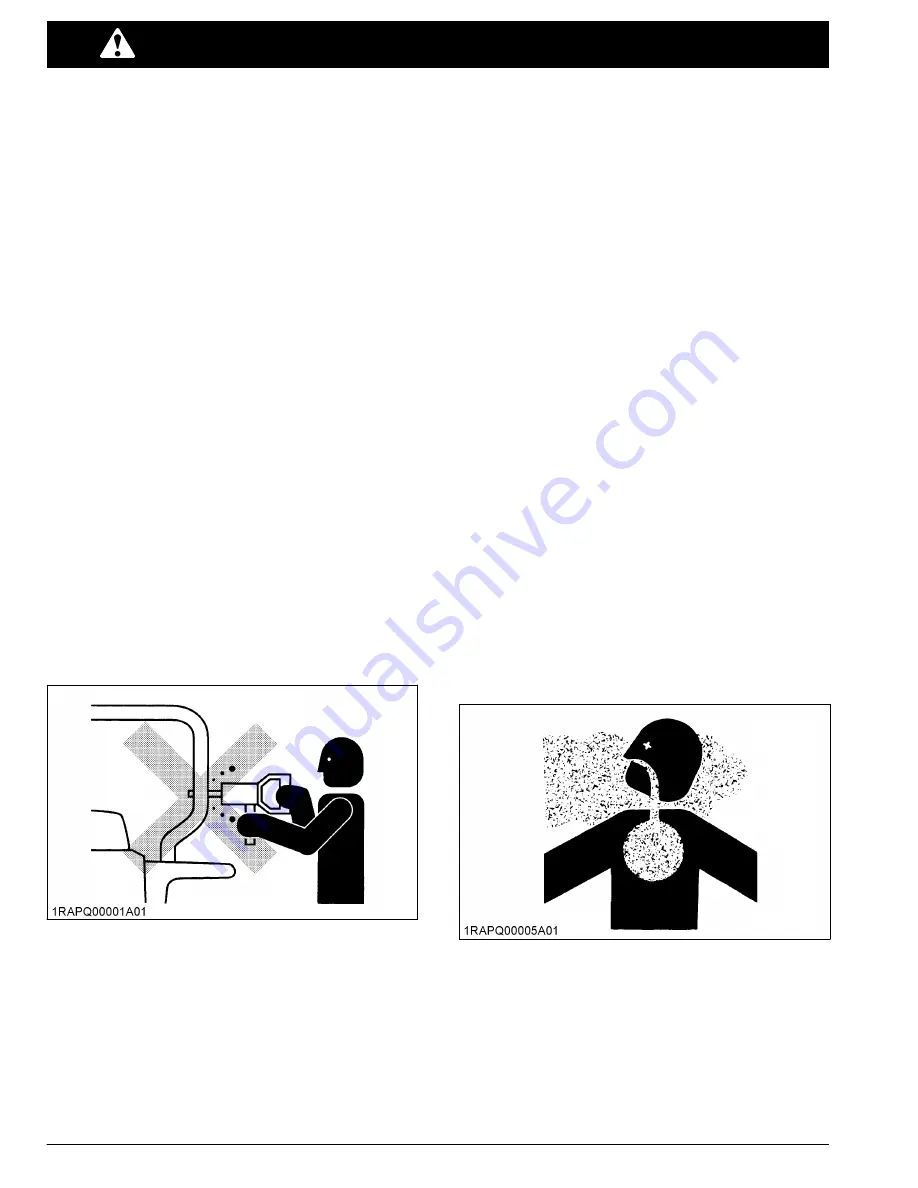
• Check the levers, pedals, and mechanical parts for
correct adjustments and wear. Replace worn or
damaged parts immediately. Check the nuts and
bolts regularly for correct torque.
• Keep your machine clean. Heavy soiling, grease,
dust, and grass can cause fires, accidents, or
injuries.
• Before starting the machine, be absolutely sure that
the machine has been filled with fuel, lubricated,
greased,
and
undergone
all
necessary
maintenance.
• Do not modify the machine, otherwise it could lead
to unforeseen safety problems.
• Make sure that the attachments, particularly those
utilizing quick-hitch, are securely mounted. Use
only attachments authorized by KUBOTA.
2. Precautions of ROPS and FOPS
Know your equipment and its limitations. Read and
understand this entire manual before starting and
operating the machine with the ROPS and FOPS.
• For your safety, KUBOTA installs a ROPS (roll-
over-protective-structure) and a FOPS (falling-
objects-protective-structure) with a seat belt.
Always use the seat belt when the machine is
equipped with the ROPS or the FOPS. Combination
of the seat belt and the ROPS or the FOPS will
reduce the risk of personal injury or death if the
machine is upset.
Do not modify structural members of the ROPS or
FOPS by welding, drilling, bending, grinding, or
cutting, as this may weaken the structure.
If any component is damaged, replace it. Do not
repair the component.
If the ROPS or FOPS is loosened or removed for
any reason, make sure that all parts are reinstalled
correctly. Tighten mounting bolts to proper torque.
• The ROPS and the FOPS structure complies with
ISO 3471, ISO 3449, and OSHA regulations.
PRECAUTIONS FOR
OPERATING THE MACHINE
• Mount and dismount the machine safely. Always
face the machine. Always use handrails and
available steps and keep yourself well balanced.
Do not grab or hold any of the control levers and
switches. Do not jump on or off the machine,
whether stationary or in motion.
• Start and control the machine only from the
operator's seat. The operator should not lean out of
his or her seat when the engine is running.
• Before starting the engine, make sure that the
armrests are in the raised position, the control
levers are in their neutral position, and the seat belt
is fastened correctly.
• Always thoroughly check the surrounding area for
any possible conditions that could create a
dangerous situation.
– Make sure that you read the operator's manual
to thoroughly understand the operating
conditions and limitations of the machine.
– To avoid damage and to prevent accidents,
always use the buddy system and have the
other person, check for clearances and other
possible dangers that may be obstructed from
view.
– Never allow people to approach the vicinity of
the turning radius of the machine.
– Be cognizant of blind spots to the rear and
always check behind you before backing up.
• Only operate the machine in well-ventilated area to
avoid poisoning from carbon monoxide, an
odorless, colorless gas that is deadly.
• Never remove any of the safety features on the
machine.
– Make sure that all safety features, including
guards, protective devices, doors, and cabin
are functioning normally, properly secured, and
in good condition.
Repair and replace any lost or damaged
protective features.
– Carefully read the operator's manual in order to
understand the proper use of safety features
SAFE OPERATION
8
SVL65-2
Summary of Contents for SVL65-2
Page 10: ...6 SVL65 2...
Page 20: ...SAFETY LABELS SAFE OPERATION 16 SVL65 2...
Page 21: ...SAFE OPERATION SVL65 2 17...
Page 22: ...SAFE OPERATION 18 SVL65 2...
Page 23: ...SAFE OPERATION SVL65 2 19...
Page 24: ...SAFE OPERATION 20 SVL65 2...
Page 25: ...SAFE OPERATION SVL65 2 21...
Page 26: ...SAFE OPERATION 22 SVL65 2...
Page 28: ...24 SVL65 2...