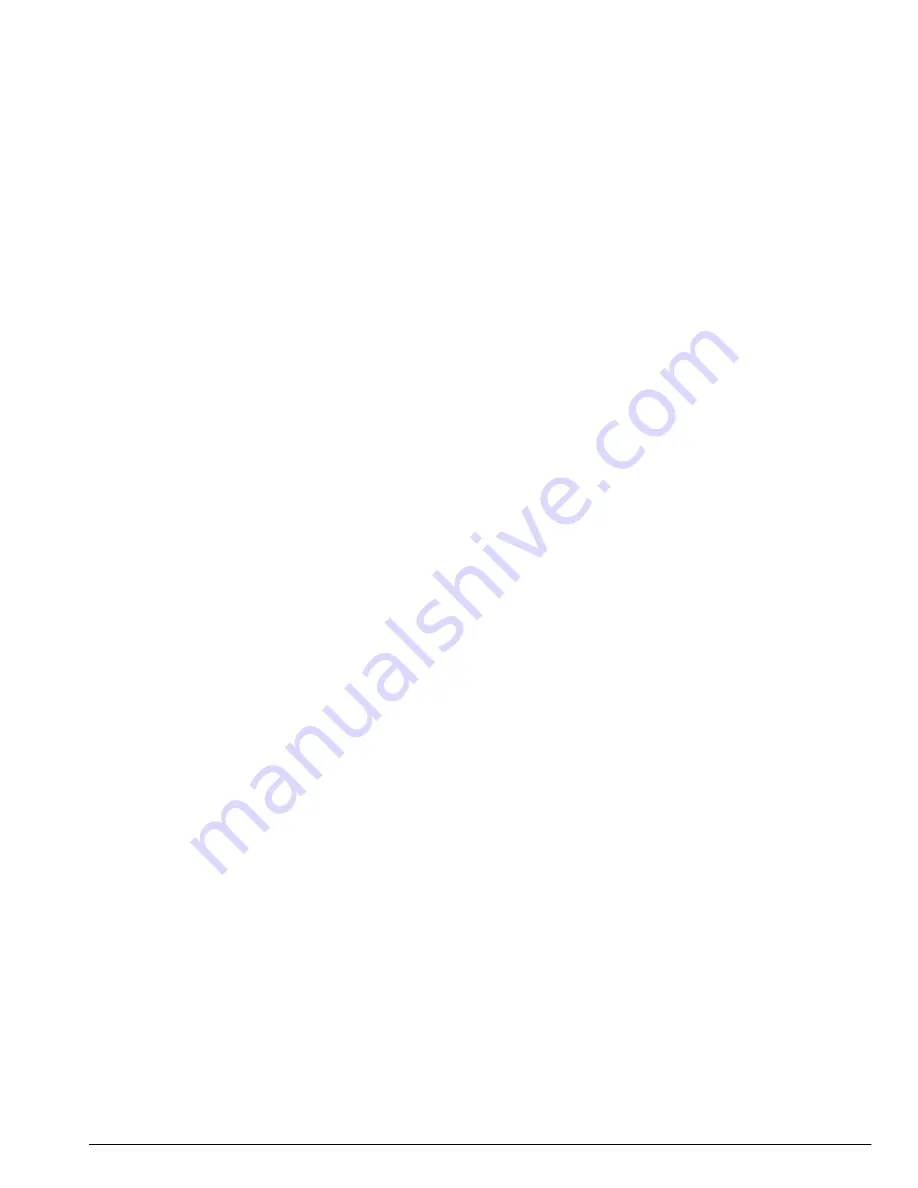
TAKING CARE OF MACHINE AFTER OPERATION IN COLD WEATHER ....................................................... 60
MAINTENANCE .........................................................................................................................61
PRECAUTIONS FOR MAINTENANCE .............................................................................................................. 61
MAINTENANCE INTERVALS ............................................................................................................................. 63
PERIODIC SERVICE .................................................................................................................66
1. Precautions for opening and closing the covers........................................................................................ 66
2. Opening and closing the engine cover ...................................................................................................... 66
3. Opening the document folder and the magazine rack............................................................................... 66
4. Opening the grease gun holder to store the grease gun ........................................................................... 66
DAILY CHECK .................................................................................................................................................... 66
1. Checking and replenishing the engine oil.................................................................................................. 67
2. Checking and replenishing the hydraulic oil .............................................................................................. 67
3. Checking and replenishing the fuel ........................................................................................................... 67
4. Checking and replenishing the coolant...................................................................................................... 68
5. Checking and replenishing the oil in the brake fluid reservoir ................................................................... 69
6. Applying the grease to the grease fittings ................................................................................................. 69
7. Checking the pressure and wear of tire and the wheel bolts..................................................................... 71
8. Checking and cleaning the radiator, the oil cooler, and the inter cooler .................................................... 71
9. Checking the steering................................................................................................................................ 71
10. Checking the gear locked parking brake ................................................................................................. 72
11. Checking the disc brake........................................................................................................................... 72
12. Checking and cleaning the engine and the electrical wiring.................................................................... 72
13. Checking the V-belt ................................................................................................................................. 72
14. Washing the whole machine.................................................................................................................... 72
15. Draining the water separator ................................................................................................................... 72
16. Cleaning the evacuator valve .................................................................................................................. 73
17. Checking the dust indicator ..................................................................................................................... 73
18. Checking and tightening the loose bolts and the nuts ............................................................................. 74
19. Checking the electrical wiring for short-circuits and loose terminals ....................................................... 74
20. Checking the lamps and the instruments ................................................................................................ 74
21. Testing the horn ....................................................................................................................................... 74
22. Checking the machine for leaks .............................................................................................................. 74
23. Checking and cleaning after operating in muddy areas .......................................................................... 74
24. Cleaning the pre-cleaner ......................................................................................................................... 74
SERVICE EVERY 50 HOURS ............................................................................................................................ 74
1. Draining water from the fuel tank............................................................................................................... 74
2. Checking the battery condition .................................................................................................................. 74
2.1 Charging the battery........................................................................................................................... 75
2.2 Storing the battery.............................................................................................................................. 76
SERVICE EVERY 200 HOURS .......................................................................................................................... 76
1. Checking the fan belt tension .................................................................................................................... 76
1.1 Checking and adjusting the V-belt tension ......................................................................................... 76
2. Checking the radiator hoses and the clips................................................................................................. 77
3. Cleaning and checking the air cleaner element......................................................................................... 77
4. Checking the fuel line and the intake air line ............................................................................................. 78
5. Checking the wheel bolts........................................................................................................................... 78
6. Cleaning the air cleaner element............................................................................................................... 78
SERVICE EVERY 250 HOURS .......................................................................................................................... 79
1. Replacing the water separator filter element ............................................................................................. 79
2. Changing the engine oil............................................................................................................................. 80
3. Replacing the engine oil filter cartridge ..................................................................................................... 80
SERVICE EVERY 500 HOURS .......................................................................................................................... 81
1. Checking and replenishing the oil in the front and the rear axle case ....................................................... 81
2. Replacing the LST oil filter......................................................................................................................... 81
3. Replacing the return filter .......................................................................................................................... 82
R430
3
Summary of Contents for R430
Page 9: ...INDEX 105 R430 5 ...
Page 10: ...6 R430 ...
Page 19: ...SAFETY LABELS SAFE OPERATION R430 15 ...
Page 20: ...SAFE OPERATION 16 R430 ...
Page 21: ...SAFE OPERATION R430 17 ...
Page 22: ...SAFE OPERATION 18 R430 ...
Page 23: ...SAFE OPERATION R430 19 ...