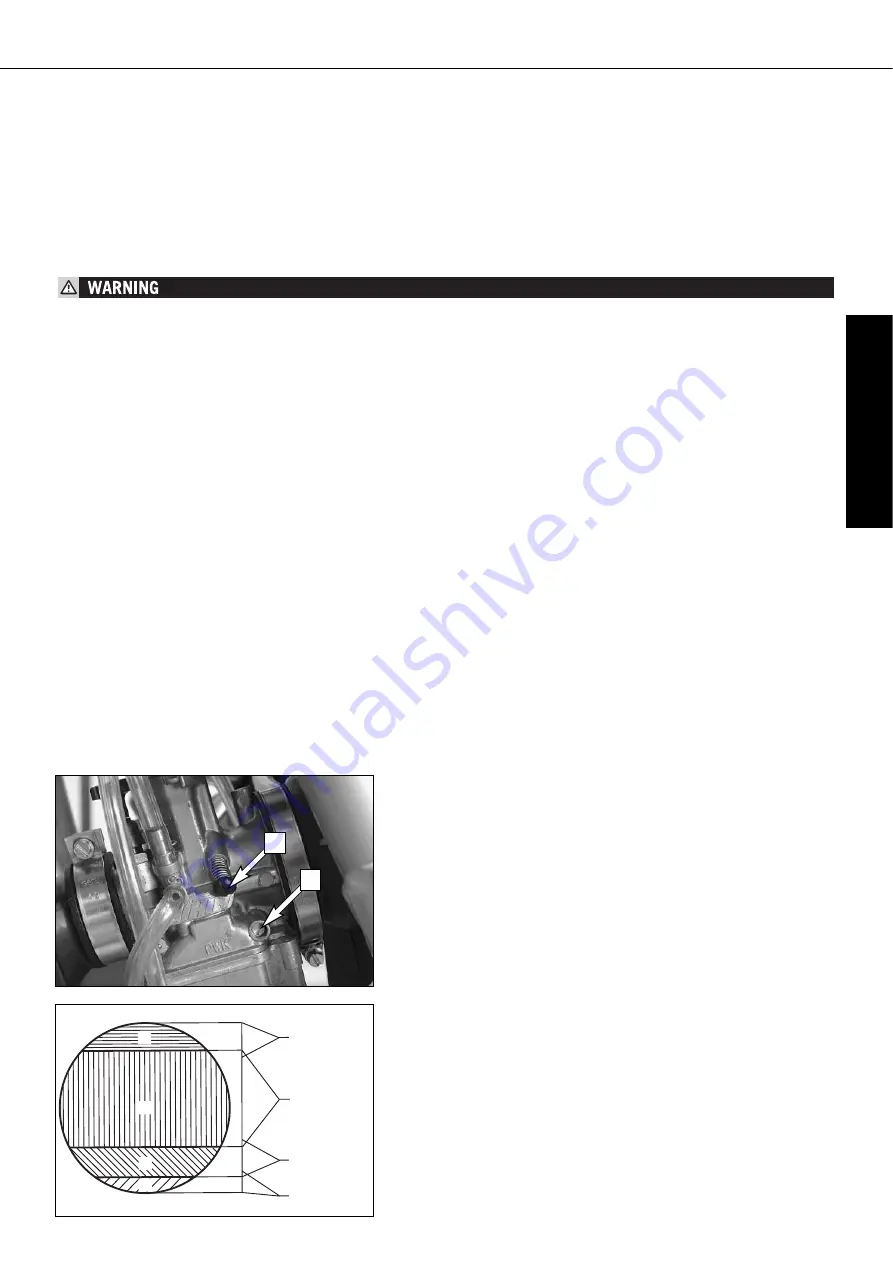
ENGLISH
29
MAINTENANCE WORK ON CHASSIS AND ENGINE
»
Idling range A
Operation with closed throttle valve. This range is influenced by the position
of the air control screw
[1]
and the air control screw
[2]
. Only make adjust-
ments when the engine is hot.
To this end, slightly increase the idling speed of the engine by means of the
air control screw. Turning it clockwise produces a higher idling speed and turn-
ing the screw counterclockwise produces a lower idling speed. Create a round
and stable engine speed using the air control screw (basic position of the air
control screw = open by 1.5 turns). Then adjust to the normal idling speed
by means of the air control screw.
Opening up – B
Engine behavior when the throttle opens. The idle jet and the shape of the
throttle valve influences this range. If, despite good idling-speed and
part-throttle setting, the engine sputters and smokes when the throttle is fully
opened and develops its full power not smoothly but suddenly at high
engine speeds, the mixture to the carburetor will be too rich, the fuel level
too high or the float needle is leaking.
Part-throttle range – C
Operation with partly open throttle valve. This range is only influenced by the
jet needle (shape and position). The optimum part-throttle setting is
controlled by the idling setting in the lower range and by the main jet in the
upper range. If the engine runs on a four-stroke cycle or with reduced power
when it is accelerated with the throttle partly open, the jet needle must be
lowered by one notch. If the engine pings, especially when accelerating under
full power at maximum engine revs, the jet needle should be raised.
If these faults should occur at the lower end of the part throttle range at a
four-stroke running, make the idling range leaner; if the engine pings, adjust
the idling range richer.
Full throttle range – D
Operation with the throttle fully open (flat out). This range is influenced by
the main jet and the jet needle. If the porcelain of the new spark plug is found
to have a very bright or white coating or if the engine rings, after a short dis-
tance of riding flat out, a larger main jet is required. If the porcelain is dark
brown or black with soot the main jet must be replaced by a smaller one.
1
2
Carburetor adjustment *
Basic information on the original carburetor setting
The original carburetor setting was adapted for an altitude of approx. 500 meters (1600 ft.) above sea level, and the ambient
temperature of approx. 20° C (68° F), mainly for off-road use and central European premium-grade fuel (ROZ 95).
Mixing ratio 2-stroke motor oil : super fuel 1:40 .
Basic information of changing the carburetor setting
Always start out from the original carburetor setting. Essential requirements are a clean air filter system, air-tight exhaust system and
an intact carburetor. Experience has shown that adjusting the main jet, the idling jet and the jet needle is sufficient and that changes
to other parts of the carburetor will not greatly affect engine performance.
RULE OF THUMB: high altitude or high temperatures
→
choose leaner carburetor adjustment
low altitude or low temperatures
→
choose richer carburetor adjustment
– Only use unleaded fuel with at least RON 95 (USA = Premium RON 91), mixed with high grade two-stroke oil. Other types of gaso-
line can cause engine failure, and their use will void your warranty.
– Only use high-grade 2-stroke engine oil of known brands (e. g. Motorex Cross Power 2T).
– Do not use premixed two-stroke oils, oils for outboard engines or normal engine oil to prepare the mixture.
– Not enough oil or low-grade oil can cause erosion of the piston. If you use too much oil, the engine can start smoking and foul the
spark plug.
– In the case of a leaner adjustment of the carburetor proceed cautiously. Always reduce the jet size in steps of one number to avoid
overheating and piston seizure.
NOTE: If the engine does not run properly, despite a changed adjustment look for mechanical faults and check the ignition system.
Basic information on carburetor wear:
Engine vibrations subject the throttle slide, jet needle, float needle valve and the needle jet to extreme wear. Wear leads to malfunctio-
ning of the carburetor (e.g. over-enrichment). These parts should be replaced after 100 operating hours. The carburetor body, main
jet holder and the float support should be replaced after 200 operating hours.
B
C
D
A
main jet
jet needle
jet needle
idling jet
idling jet
throttle valve
Summary of Contents for 85 SX 2007
Page 40: ...ENGLISH 39...
Page 41: ...ENGLISH 40...