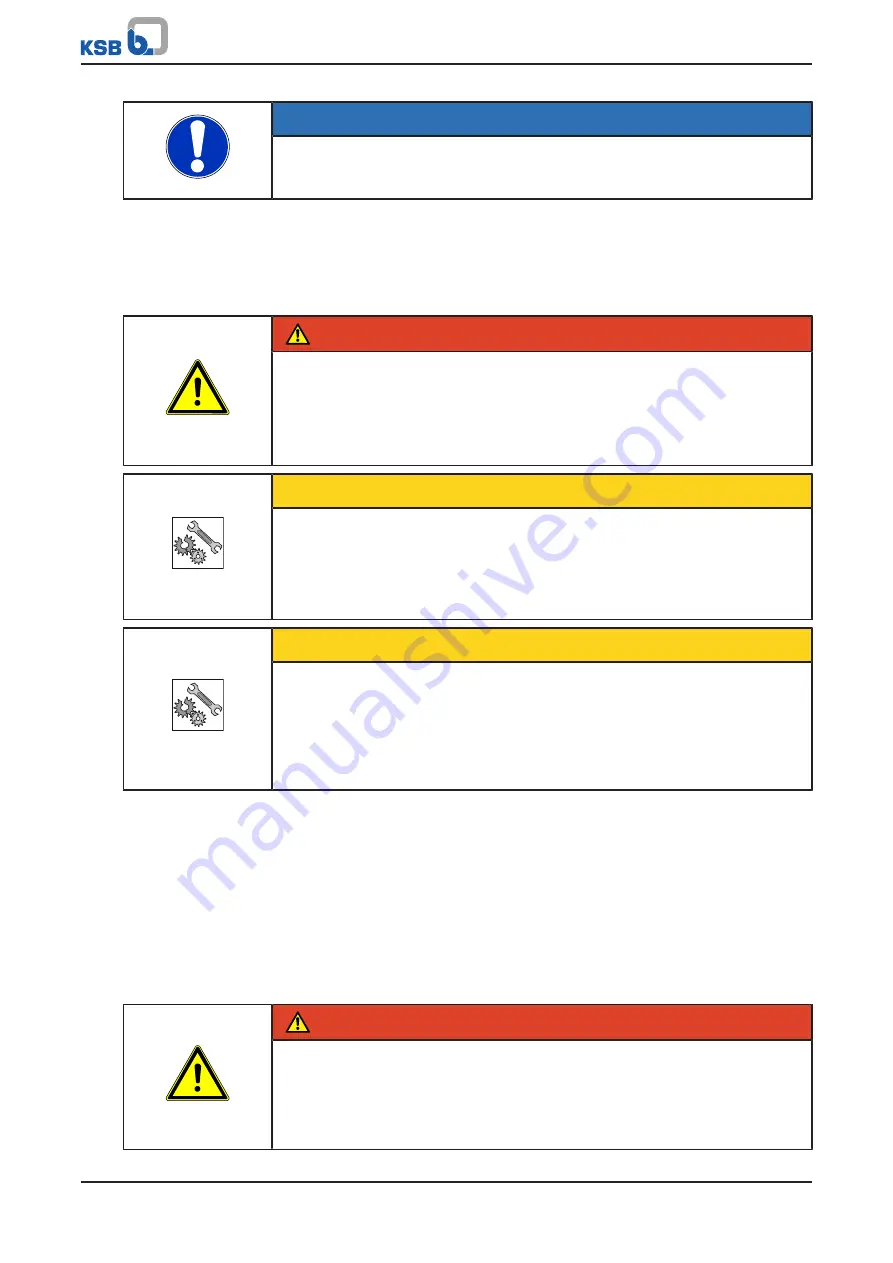
7 Servicing/Maintenance
31 of 44
Vitastage
NOTE
All maintenance work, service work and installation work can be carried out by KSB
Service or authorised workshops. For contact details please refer to the enclosed
"Addresses" booklet or visit "
Never use force when dismantling and reassembling the pump set.
7.2 Servicing/inspection
7.2.1 Supervision of operation
DANGER
Incorrectly serviced shaft seal
Fire hazard!
Hot fluids escaping!
Damage to the pump set!
▷
Regularly service the shaft seal.
CAUTION
Increased wear due to dry running
Damage to the pump set!
▷
Never operate the pump set without liquid fill.
▷
Never close the shut-off element in the suction line and/or supply line during
pump operation.
CAUTION
Impermissibly high temperature of fluid handled
Damage to the pump!
▷
Prolonged operation against a closed shut-off element is not permitted
(heating up of the fluid).
▷
Observe the temperature limits in the data sheet and in the section on
operating limits.
While the pump is in operation, observe and check the following:
▪
The pump must run quietly and free from vibrations at all times.
▪
▪
Check the static seals for leakage.
▪
Monitor the stand-by pump.
To make sure that the stand-by pumps are ready for operation, start them up
once a week.
7.2.2 Inspection work
DANGER
Excessive temperatures caused by friction, impact sparking or frictional sparking
Fire hazard!
Damage to the pump set!
▷
Regularly check the cover plates, plastic components and other guards of
rotating parts for deformation and sufficient distance from rotating parts.
Summary of Contents for Vitastage
Page 1: ...Hygienic Pump Vitastage Installation Operating Manual ...
Page 43: ......