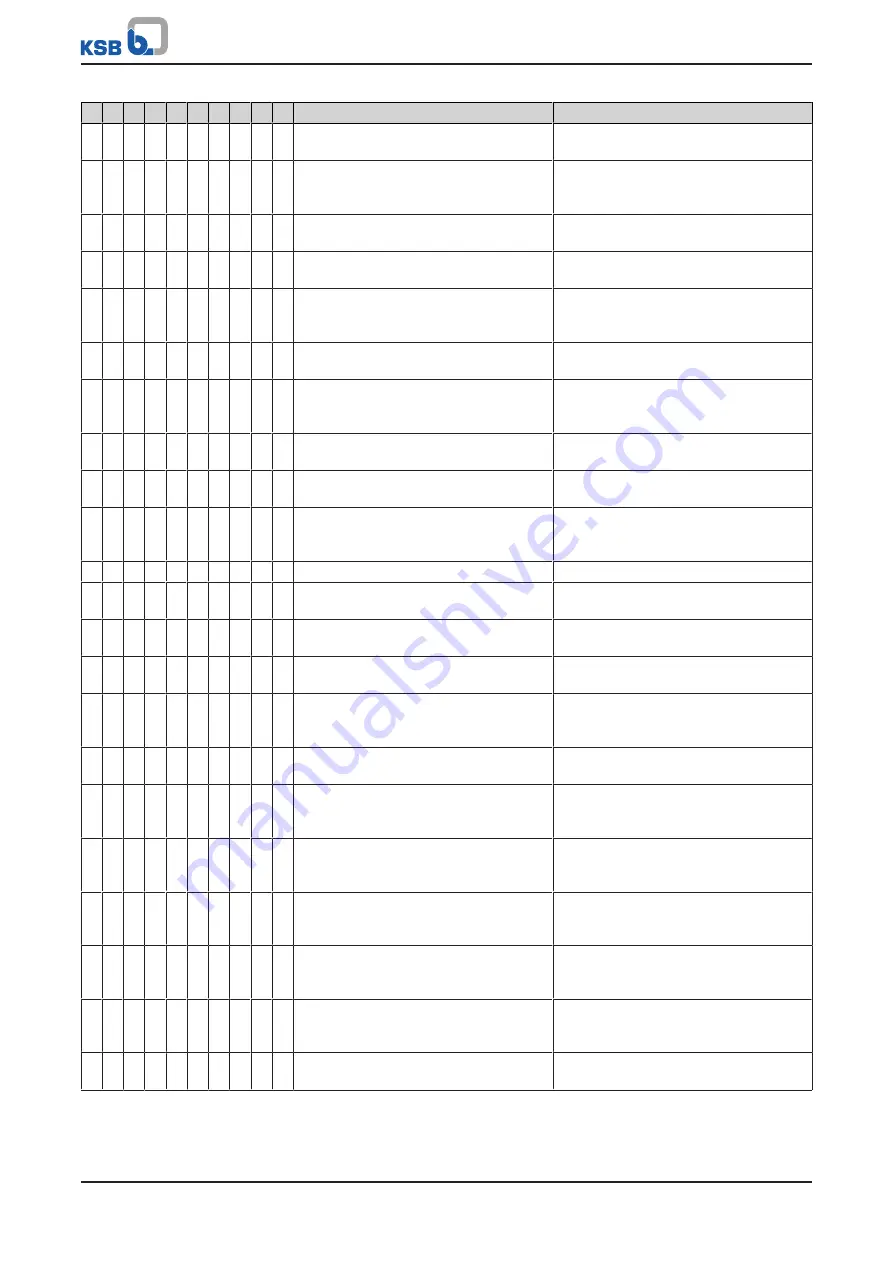
8 Trouble-shooting
68 of 80
Vitacast / Vitacast Bloc
A B C D E
F G H
I
J Possible cause
Remedy
19)
-
-
-
-
✘
-
-
-
-
- Fluid viscosity too high for centrifugal
pump
Check suitability of different pump.
-
-
-
-
✘
-
-
-
✘
- Flow rate too high
Reduce flow rate with discharge-side
control valve. Reduce impeller diameter
or fit orifice plate.
-
-
-
-
✘
-
-
-
-
- Speed too high (operation on a
frequency inverter)
Reduce speed.
-
-
-
-
✘
-
-
-
✘ ✘
Impermissible friction. Impeller touches
inner wall of casing.
Repair pump. Re-adjust.
-
-
-
-
✘ ✘ ✘
-
✘ ✘
Pump set not correctly aligned (radial or
angular shaft misalignment), or shaft
run-out
Re-align pump and motor or fit new
pump shaft.
-
-
-
-
✘
-
-
-
✘
- Rolling element bearings of pump and/
or motor worn
Replace bearings.
-
✘ ✘
-
✘
-
-
-
-
- Incorrect electrical installation.
Adjust electrical connection as required
(only to be performed by trained
specialist personnel).
-
✘ ✘
-
✘
-
-
-
-
- Electrical voltage does not match motor
used.
Use motor suitable for electric mains.
-
-
-
-
-
✘ ✘ ✘
-
- Fluid or fluid temperature unsuitable
for mechanical seal materials used
Select type and material of mechanical
seal as required.
-
-
-
-
-
✘ ✘ ✘
-
- Pump not cleaned sufficiently after it
was used for fluids that tend to
crystallise
Drain fluid immediately after pump
operation. Perform several cleaning
cycles.
-
-
-
-
-
✘ ✘
-
-
- Mechanical seal installed incorrectly
Re-install mechanical seal correctly.
-
-
-
-
-
✘
-
-
-
- Incorrect direction of rotation of pump
with non-reversible mechanical seal
Change the direction of rotation.
-
-
-
-
-
✘ ✘
-
-
- Outer mechanical seal flushed
insufficiently (for seal type Q)
Provide sufficient flushing liquid and
liquid pressure.
-
-
-
-
-
✘ ✘
-
-
- Dry running of pump
Monitor pump and system (flow meter,
pressure gauge) to prevent dry running.
-
-
-
-
-
✘ ✘
-
-
- Vibrations of pump shaft caused by
misalignment of pump set or worn
rolling element bearings
Re-align pump and motor. Replace
rolling element bearings.
-
-
-
-
-
-
✘
-
-
- Fluid contains solids.
Select type and material of mechanical
seal as required.
-
-
-
-
-
-
-
✘
-
- Excessive fluid temperature or thermal
shock
Observe permissible temperature limits,
increase fluid temperature slowly and
avoid abrupt temperature changes.
-
-
-
-
-
-
-
-
✘ ✘
Impeller out of balance
Remove any foreign matter from
impeller. Replace or clean impeller as
required.
-
-
-
-
-
-
-
-
✘
- Flow rate too low
Open discharge-side control valve
further to reduce flow losses in
discharge line.
-
-
-
-
-
-
-
-
✘
- Insufficiently secured pump and piping
system
Check anchoring of pump or pump set.
Support and fasten piping sufficiently,
use expansion joints if required.
-
-
-
-
-
-
-
-
-
✘
Rolling element bearings lubricated
insufficiently.
Replace bearings. Provide correct grease
or oil quantity. Observe maintenance
intervals.
-
-
-
-
-
-
-
-
-
✘
Water enters pump bearings.
Clean the bearings. Fill in new
lubricants. Replace joint rings.