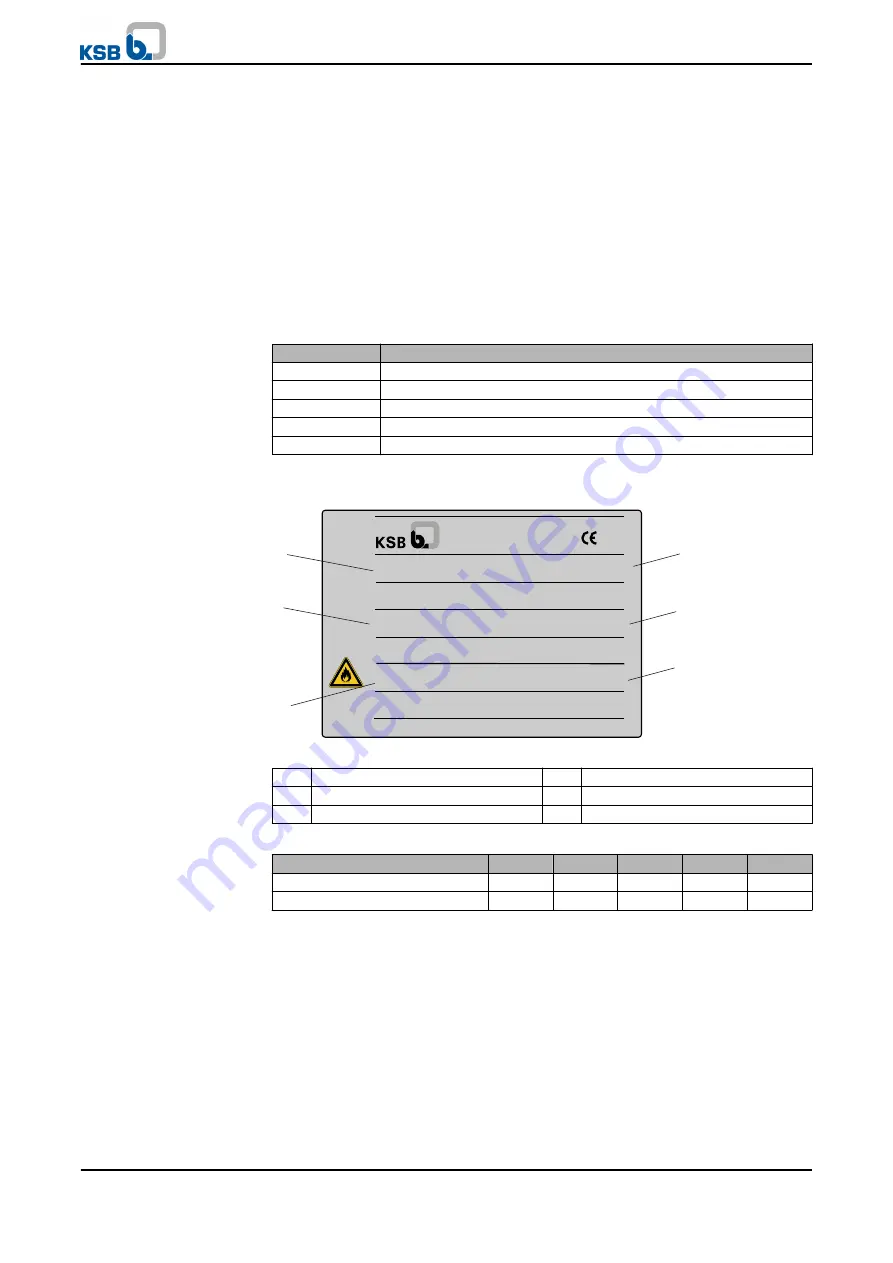
4
Description of the Pump (Set)
4.1
General
▪
Non-self-priming in-line pump
Pump for handling clean or aggressive fluids not chemically and mechanically
aggressive to the pump materials.
4.2
Designation
Example: Trialine 40 - 100 / 052
Table 4: Key to the designation
Code
Description
Trialine
Type series
40
Nominal suction/discharge nozzle diameter [mm]
100
Nominal impeller diameter [mm]
05
Motor rating: kW x 10 (example 0.55 kW)
2
Number of motor poles
4.3
Name plate
Trialine 40-100/032 S - W
Qmax: 22 m
3
/h Hmax: 6,6 m
PN 10
Aktiengesellschaft
D-67225 Frankenthal
01058780 Made by KSB ZNI 1448L
max. 120°C
1
2
5
4
3
6
Fig. 2: Name plate
1
Type series, size
2
Flow rate
3
Maximum fluid temperature
4
Series number
5
Maximum head
6
Maximum operating pressure
Table 5: Key to the series number
Calendar year
2009
2010
2011
2012
2013
1st half of the year
S-U
S-W
S-Y
S-A
S-C
2nd half of the year
S-V
S-X
S-Z
S-B
S-D
4.4
Design details
▪
Close-coupled design/in-line design
▪
Single-stage
▪
Horizontal/vertical installation
▪
Back pull-out design
▪
Rigid connection between pump and motor
▪
Pump and motor on a common shaft
▪
Closed radial impeller
▪
Mechanical seal
Key to the series number
Trialine/Trialine Z
Impeller type
Shaft seal
4 Description of the Pump (Set)
12 of 36
Trialine / Trialine Z