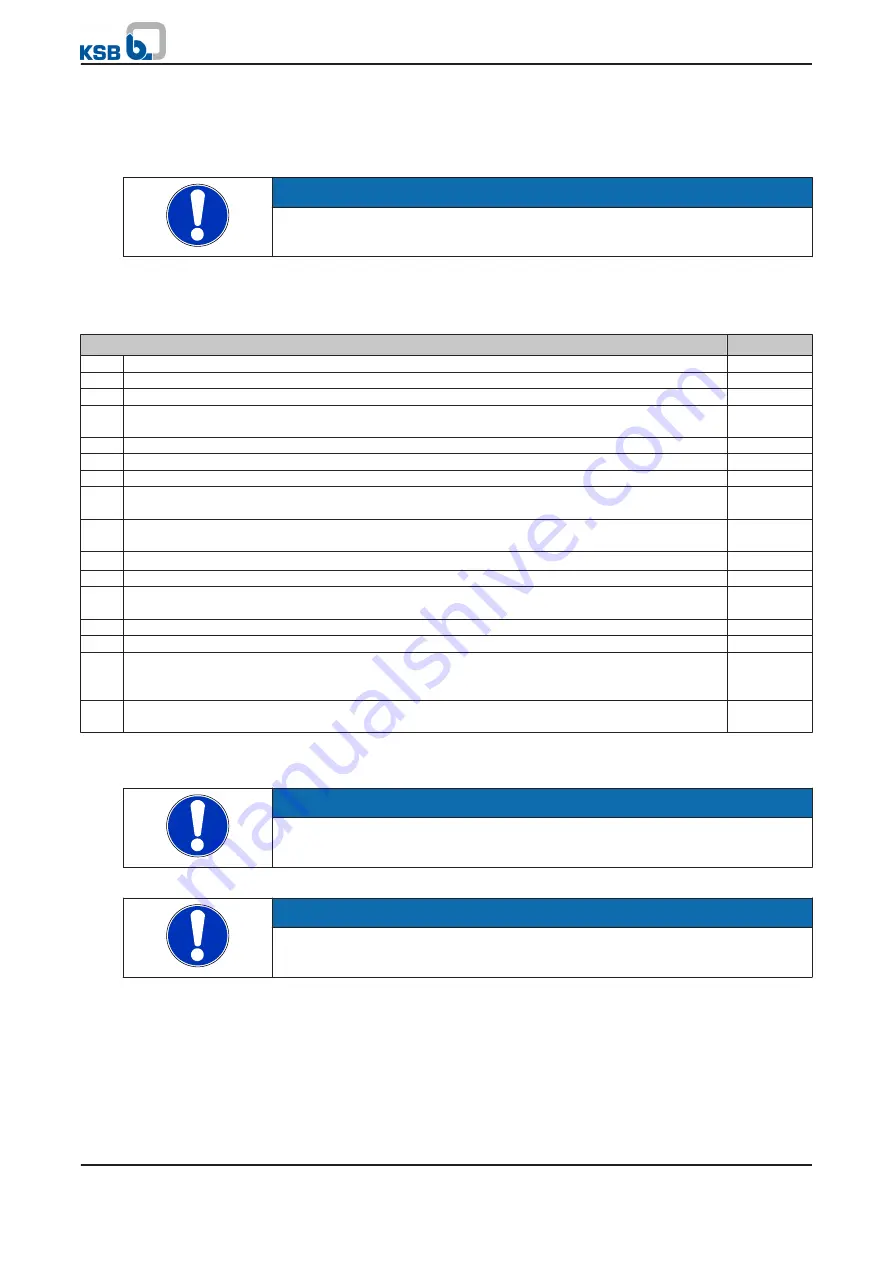
6.2 Switching on the system
Switch on the master switch to energise the system. Set the manual-0–automatic
selector switch to automatic. The green LED on the control panel lights up, indicating
the system's readiness for operation.
NOTE
The pressure booster system is pre-set at the factory. (
6.3 Checklist for commissioning/start-up
Table 7: Checklist
Operations
Done
1
Read the operating instructions.
2
Check power supply and compare against the name plate data.
3
Check the earthing system (by measuring).
4
Check the mechanical connection to the water mains.
Re-tighten the flange bolting and pipe unions.
5
Prime and vent the pressure booster system from the inlet side.
6
Check inlet pressure.
7
Check whether all cables are still firmly connected to the terminals inside the control unit.
8
Compare the settings of the motor protection switches with the name plate data; re-adjust, if
necessary.
9
Briefly start up one pump after the other in manual mode and compare the direction of
rotation at the fanwheel with the arrow indicating the direction of rotation.
10
Check the direction of rotation in automatic mode.
11
Check the start and stop pressure; re-adjust, if necessary.
12
Test the proper function of the lack-of-water and dry running protection equipment. If not
fitted, make a relevant note in the commissioning report.
13
Vent the pumps for a second time after they have been running for 5 to 10 minutes.
14
Check the pre-charge pressure.
15
Record all system conditions that do not correspond to our specifications or to the purchase
order in the commissioning report (i.e. no dry running protection or inlet pr max.
pressure of pressure booster system higher than 16 bar).
16
Complete the commissioning report together with the operator/user and instruct the operator/
user as to the function of the unit.
6.4 Shutdown
NOTE
As long as the pressure booster system is out of operation, water is supplied directly
at p
inl
through the pressure booster system.
Set the master switch to "0".
NOTE
Drain the pressure booster system for prolonged shutdown.
6 Commissioning/Start-up/Shutdown
22 of 40
Surpress Feu SFE.3