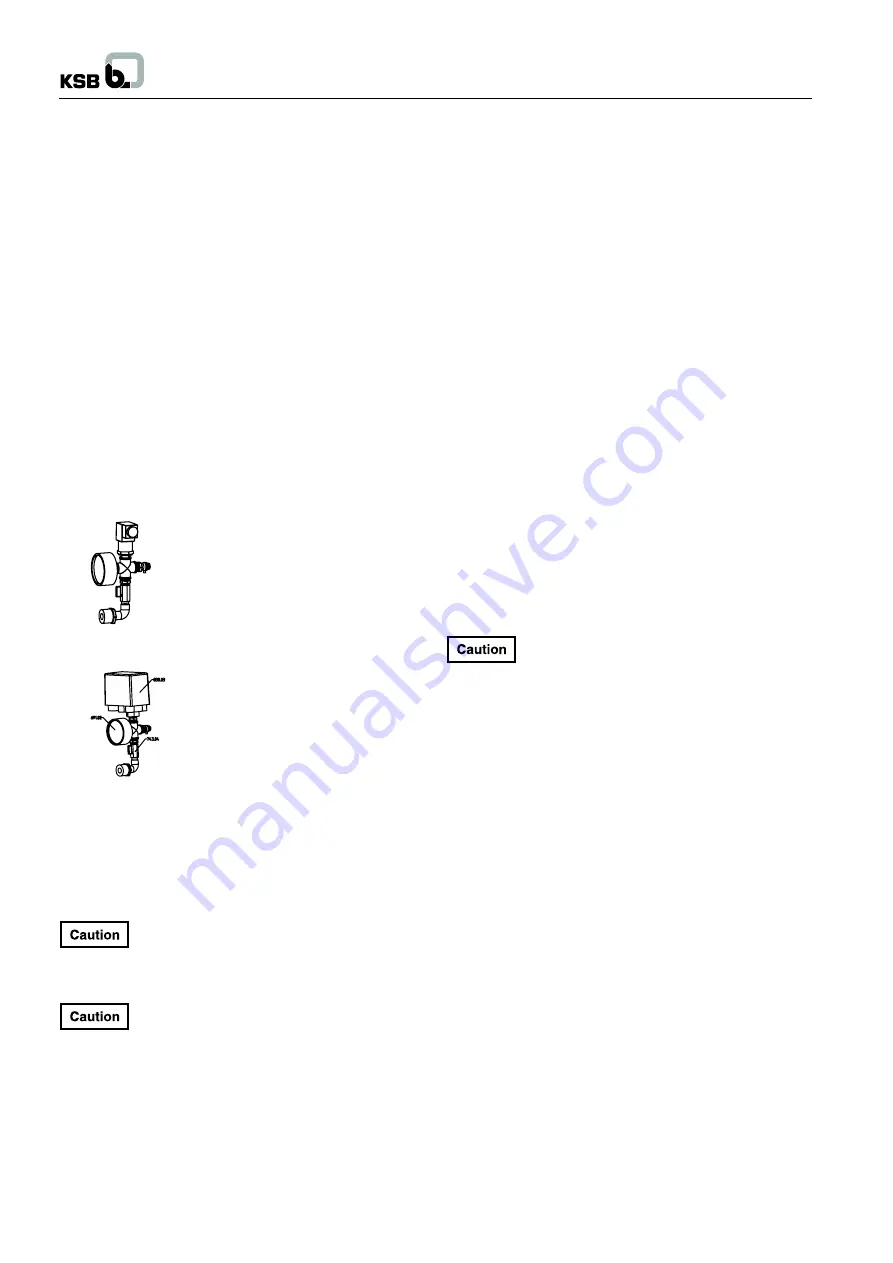
moviBOOST Vt
As demand decreases, the pumps are automatically sequenced
out by the control unit. Pressure differences are equalized by
the speed-controlled pump. The control unit will recognized when
demand has dropped to zero and stop the speed-controlled pump
last.
For an equal distribution of operating hours, the pumps which
have been started up first will be stopped first. After the base
load pump has been stopped, the frequency inverter changes to
the next pump available.
In automatic mode, the transmitter is continuously monitored. If
the output current of the transmitter drops below 3.5 mA, the
control unit considers this to be an alert condition and stops the
pumps. The alert is displayed and output to the relevant terminal.
In the event of a frequency inverter failure the control unit
automatically switches to cascade operation.
4.3
Dry running protection (supplementary
equipment)
A pressure transmitter or manometric switch may be fitted in the
suction-side header.
Pressure transmitter :
Set with parameters 3-4-1-1 and 3-4-1-2
Manometric switch :
The inlet pressure is set by means of a
manometric switch.
If the pressure drops below the set inlet pressure, the unit stops
after 7 seconds due to lack of water. The unit is automatically
started up again as soon as the lack-of-water condition has been
remedied or sufficient inlet pressure is available again.
For indirect connection to an inlet tank and an inlet pressure below
0.5 bar, the inlet must be monitored by level monitoring (for
example with a dry running protection set, see Accessories).
If other dry running protection devices are
retrofitted (see Accessories), the instructions
in the circuit diagram must be observed.
Inadequate connection may damage the unit.
On pressure boosting units ordered without
dry running protection the terminal intended for
the dry running device is open.
If no dry running protection device is connected when
commissioning takes place, the unit will be stopped after 7
seconds.
If the dry running protection terminal is deactivated by means
of a bridge, the operator shall assume responsibility for any
dry running that might occur.
4.4
Manual mode
Each pump can be started up in manual mode for 10 seconds
via the control unit (parameter 1-2-1). If fitted with manual-0-
automatic switches (supplementary equipment), the pumps can
also be started up in manual mode by means of the manual-0-
automatic switches. The pumps are then connected
directly
to
the mains, independently of the control unit.
For this mode of operation no pressure control and no lack-of-
water monitoring will be effected.
Furthermore, in manual mode a minimum flow rate is required for
each pump in order to ensure sufficient cooling of the pumps.
Example :
An open tap means a water consumption of approx. 800 to 1200
l/h.
Minimum flow rate per pump :
Pump
Min Flow (m
3
/h)
Movitec 2B
0.2
Movitec 4B
0.4
Movitec 6B
0.6
Movitec 10B
1.1
Movitec 15B
1.6
Movitec 25B
2.8
Movitec 40B
4
Movitec 60B
6
Movitec 90B
8.5
It is recommended to always keep system in
Automatic mode. In case manual mode is
necessary for shorter period, please note that the controller
will be bypassed. Continuous supervision during operation
is necessary and also ensure that pump does not operate in
shutoff / Low Head.
4.5
Control cabinet
The control cabinet is completely wired and connected to the
package unit. It is equipped with :
- a Booster Control Advanced control unit with multi-line display,
function and navigation keys and 3 LEDs signalling the
operating status
- 1 motor protection switch per pump
- 1 circuit breaker for mains and transformer
- 1 master switch (accessible from the outside)
- 1 printed circuit board
- 1 mains and control transformer
- 1 contactor/pump
- 2 volt-free changeover contacts for warning and alert (capacity
230 V
~
, 2 A)
- 1 connection for lack-of-water monitoring
- 1 frequency inverter
3
Summary of Contents for moviBOOST Vt
Page 23: ...moviBOOST Vt NOTES ...
Page 24: ...moviBOOST Vt NOTES ...