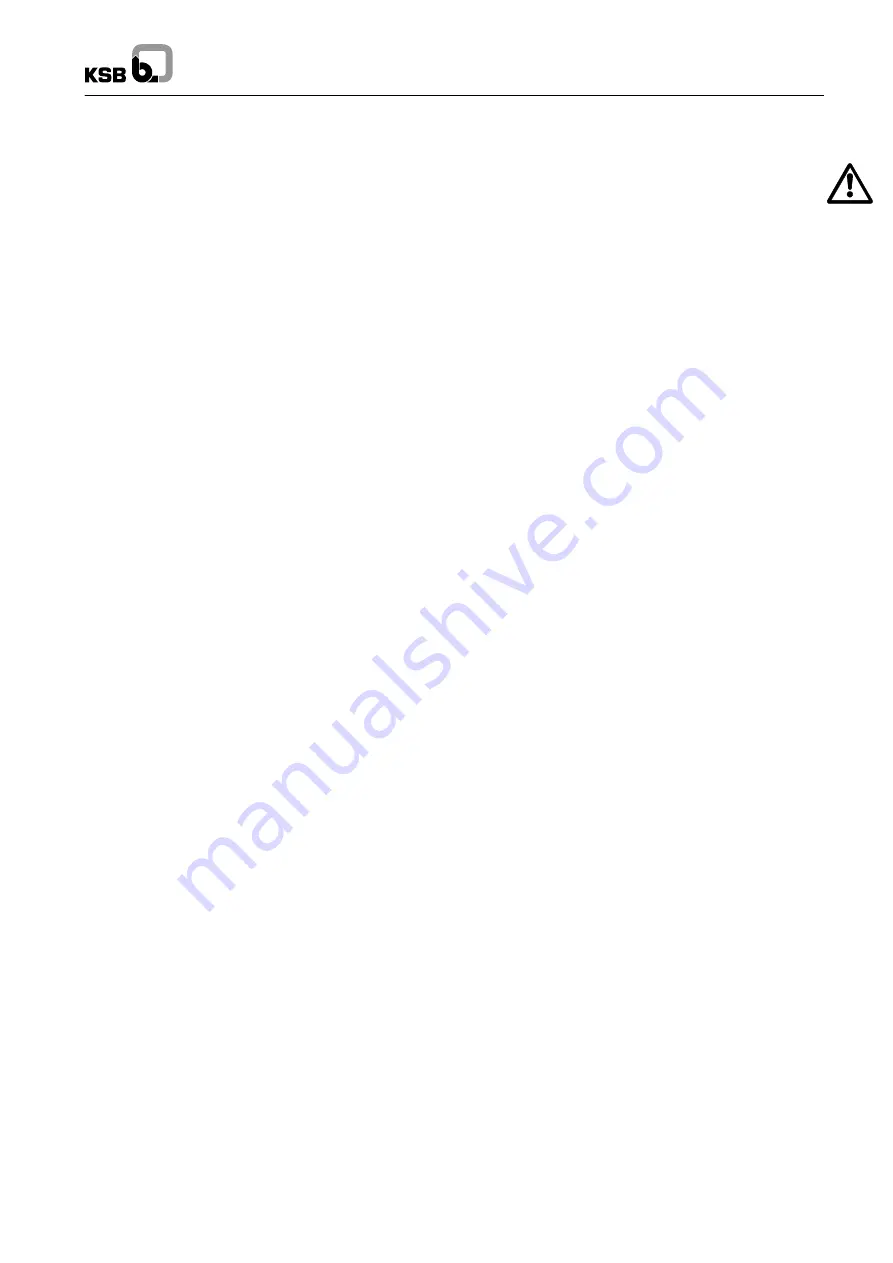
Ixo RW / Ixo RWS
12
8
Dismantling
8.1
Checking the Pump for a Jammed Shaft
Remove the pump from the PE casing by unscrewing the three
screws (900.05) and lifting it out of the casing in upward direc-
tion.
Dismantle the pump in accordance with the sectional drawing
(see page 13).
While the pump is positioned horizontally, remove the screws
(900.04), the square nuts (920) and suction strainer (106).
Hold the first stage casing (109.01) tightly with one hand so
that it does not rotate and, with a wrench on the nut (921), turn
the shaft anti-clockwise.
If the shaft is blocked and cannot be freed, continue dismantl-
ing until the cause has been found and removed.
8.2
Inspection of the Hydraulic Parts
First remove the O-ring (412.06) and then the complete motor
assembly with all internal pump parts from the discharge cas-
ing (107). The first impeller can be inspected by removing the
first stage casing (109.01). Once the nuts (921) and washer
(554.01) have been removed, the spacer sleeves (525.01), im-
pellers (230) and the other stage casings (109.02 and 109.03)
can be dismantled one after the other.
Other parts should not be dismantled.
Work on the electrical parts of the installation should only be
carried out by a licensed electrical repair shop.
8.3
Oil Chamber
If the oil chamber has to be inspected, follow these instruc-
tions:
CAUTION: The oil in the oil chamber may be pressurised.
Therefore, do not open the oil chamber unless you are
wearing protective goggles.
Care must be taken to avoid a sudden spurting-out of oil. Wait
until the oil chamber cover (160) has cooled down.
Before removing the mechanical seal (433.02), loosen the
screws (900.03) and raise the cover applying force simulta-
neously on two opposite points of the cover rim, to relieve the
pressure in the oil chamber. Carry out this operation while hold-
ing the motor in the upturned vertical position.
To refill the chamber, only use white oil suitable for food ma-
chinery and pharmaceutical use (quantity = 35 g).
To re-assemble, first mount the stationary part of the seal
(433.02) on the oil chamber cover (160) and then the oil
chamber cover (160) on the motor housing cover (812.02) with
the O-ring (412.05).
9
Spare Parts
When ordering spare parts, please quote their designation, the
part number as indicated in the sectional drawing and the data
from the pump name plate (type, date and serial number).
10
List of components
Sectional drawings see following page
Part No
Designation of parts
101
Pump casing
106
Suction strainer
107
Discharge casing
109.01
Stage casing, first stage
109.02
Stage casing
109.03
Stage casing, last stage
160
Oil chamber cover
230
Impeller
321.01
Rolling element bearing
321.02
Rolling element bearing, pump end
411.01
Joint ring (pump)
411.02
Joint ring (filler plug)
412.01
O-ring
412.02/.03 O-ring
412.04
O-ring
412.05
O-ring
412.06
O-ring
433.01
Upper mechanical seal
433.02
Mechanical seal
45-4
Spacer
50-3
Backing ring
501
Segmental ring
512
Wear ring (1)
525.01
Spacer sleeve
525.02
Washer for missing impeller (not illustrated)
Part No
Designation of parts
554.01/.02 Washer
732
Holder
733
Pipe clamp
81-42
Switch box
81-59
Stator
812.01
Motor housing cover (non-drive end)
812.02
Motor housing cover (pump end)
818
Rotor
824
Cable
829.01
Cable gland
829.02
Rubber ring for cable gland
900.01
Screw
900.02
Screw
900.03
Screw
900.04
Screw
900.05
Screw (EYOT)
903
Screwed plug
905
Tie bolt
920
Square nut
921
Shaft nut
931
Spring washer
932
Circlip
99-9
Set of sealing elements
(1) Inserted in the stage casing, cannot be supplied separately.
(2) Oil