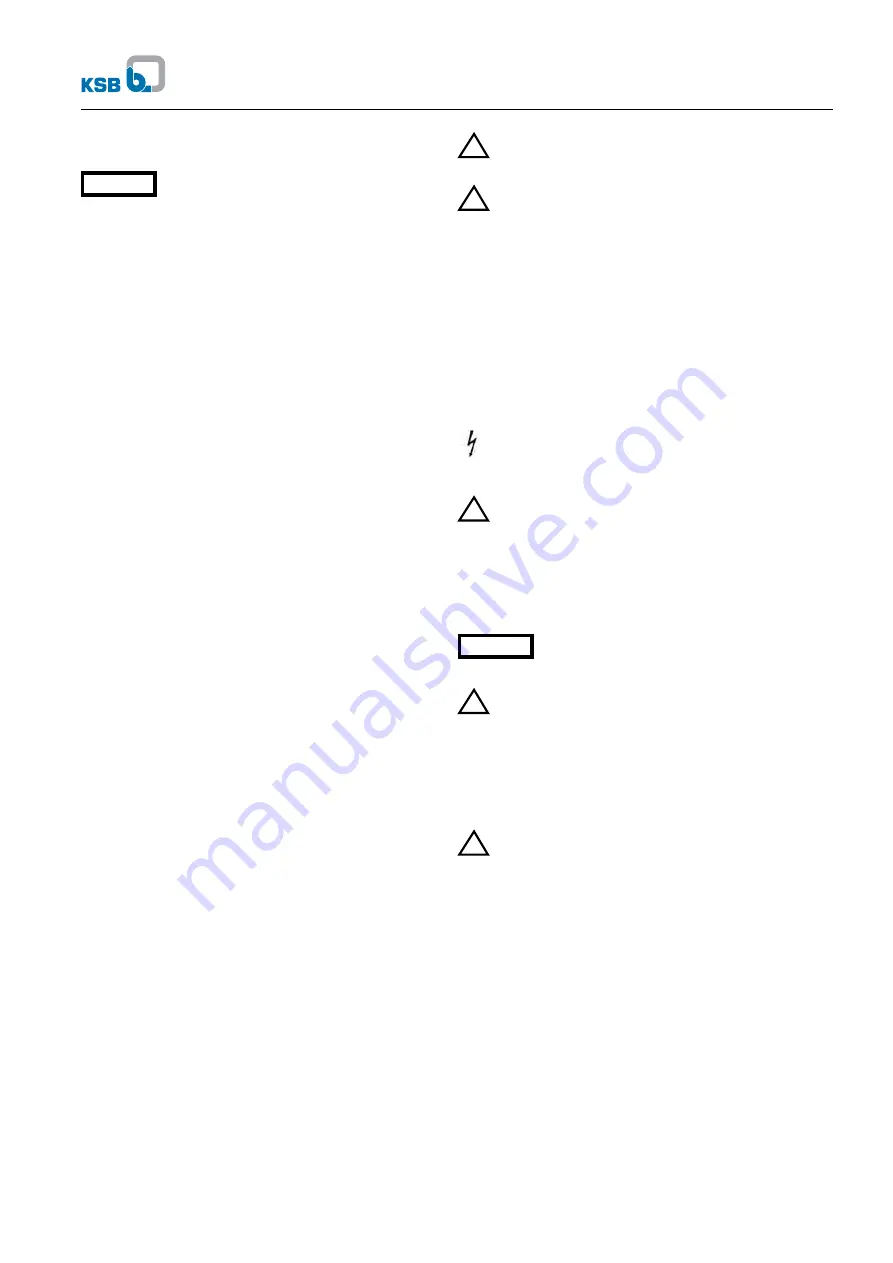
9
6.2 Operating limits
6.2.1 Temperature of the medium handled
Do not operate the pump at product tempera-
tures exceeding those specified on the data
sheet or the name plate.
6.2.2 Switching frequency
To prevent high temperature increases in the motor and
excessive loads on the pump, motor, seals and bearings, the
switching frequency shall not exceed the following number of
start-ups per hour (h).
Etabloc G, M: 15 start-ups/h
Etabloc GN, MN, SN: 15 start-ups/h
Etabloc BN, CN: 6 start-ups/h
6.2.3 Minimum flow
If the plant configuration is such that the pump might be
operated against a closed discharge side valve, a minimum
flow of
t -30to+ 70C ≈ 15 % of Qopt.
t >70 to +140 C ≈ 25 % of Qopt.
must be ensured during this period.
6.2.4 Density of medium handled
The power input of the pump will increase in proportion to
the density of the medium handled. To avoid overloading of
the motor and pump, the density of the medium must comply
with the data specified on the purchase order.
6.3 Shutdown / storage / preservation
Each KSB pump leaves the factory carefully assembled. If
commissioning is to take place some time after delivery, we
recommend that the following measures be taken for pump
storage.
6.3.1 Storage of new pumps
- New pumps are supplied by our factory duly prepared for
storage.
Maximum protection for up to 12 months, if the pump is
properly stored indoors.
- Store the pump in a dry location.
6.3.2 Measures to be taken for prolonged shutdown
1.The pump remains installed; periodic check of operation
In order to make sure that the pump is always ready for
instant start-up and to prevent the formation of deposits
within the pump and the pump intake area, start up the
pump set regularly once a month or once every 3 months
for a short time (approx. 5minutes) during prolonged shut-
down periods.
Prior to an operation check run ensure that there is suffi-
cient liquid available for operating the pump.
2.The pump is removed from the pipe and stored
Before putting the pump into storage, carry out all checks
specified in sections 7.1 to 7.4. Then apply appropriate
preservatives:
Spray-coat the inside wall of the pump casing, and in par-
ticular the impeller clearance areas,with a preservative.
Spray the preservative through the suction and discharge
nozzles. It is advisable to close the pump nozzles (e.g.with
plastic caps or similar).
6.4 Returning to service after storage
Before returning the pump to service, carry out all checks
and maintenance work specified in sections 7.1 and 7.2.
In addition, the instructions laid down in the sections
on “Commissioning” (6.1) and ”Operating limits” (6.2)
must be observed.
Immediately following completion of the work, all safe-
ty-relevant and protective devices must be re-installed
and/or re-activated.
7 Servicing / maintenance
7.1 General instructions
The operator is responsible for ensuring that all mainte-
nance, inspection and installation work be performed by
authorized, qualified specialist personnel who are thorough-
ly familiar with the manual.
A regular maintenance schedule will help avoid expensive
repairs and contribute to trouble-free, reliable operation of
the pump with a minimum of maintenance expenditure and
work.
Work on the unit must only be carried out with the
electrical connections disconnected. Make sure
that the pump set cannot be switched on accidentally
(danger to life!).
Pumps handling liquids posing health hazards
must be decontaminated. When draining the medi
um see to it that there is no risk to persons or the envi-
ronment. All relevant laws must be adhered to (danger to
life)!
7.2 Servicing / inspection
7.2.1 Supervision of operation
The pump must run quietly and free from vibra-
tions at all times.
The pump must never be allowed to run dry.
Do not run the pump against a closed shut-off valve for
prolonged periods of time so as to avoid heating up of
the fluid pumped.
Max. permissible room temperature 40
º
C.
Bearing temperature may exceed room temperature by up to
50
º
C but must never rise above +90
º
C (measured external-
ly on the motor housing).
For required minimum flows please refer to section 6.2.3.
During pump operation the shut-off valve in the suction
line must not be closed.
The mechanical seal shows only slight or invisible (vapour)
leakage during operation. It is maintenance-free.
Any stand-by pumps installed shall be switched on and then
immediately off again once a week to keep them operational.
Attention shall be paid to the correct functioning of the auxil-
iary connections.
7.2.2 Lubrication and lubricant change
7.2.2.1 Lubrication
The rolling element bearings in the KSB IEC motor are
grease-lubricated. The lubricant change intervals as well as
the required quantity and quality are specified below.
!
!
!
!
!
Etabloc
Caution
Caution