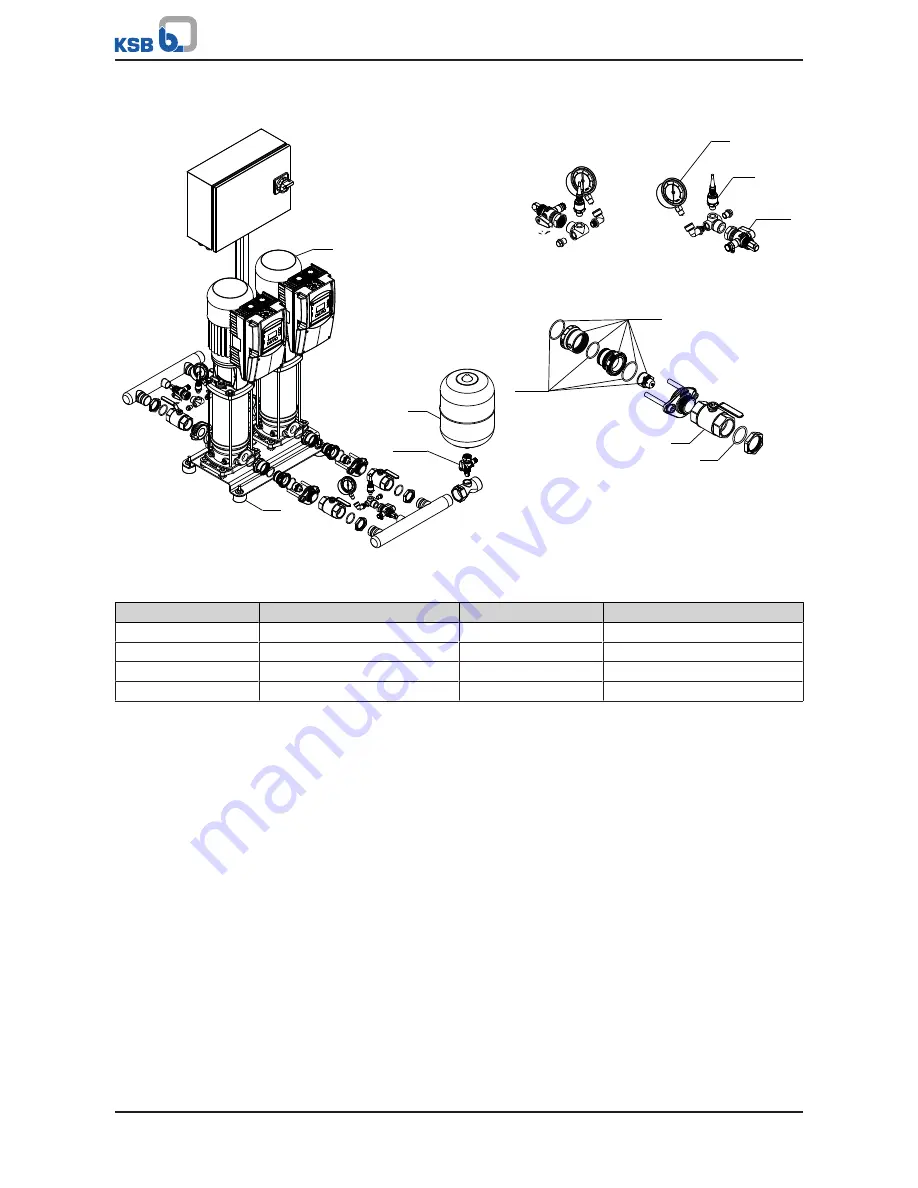
11 Related Documents
61 of 68
KSB Delta Solo / KSB Delta Eco
11.1.2 KSB Delta Eco SVP
591
655
595
743.90
743.90
79-2
691
742.02
742.01
743
412
Fig. 44:
KSB Delta Eco SVP
Table 27:
List of components
Part No.
Description
Part No.
Description
79-2
Measuring transducer
655
Pump
412
O-ring
691
Pressure gauge
591
Accumulator
742.01/.02
Check valve
595
Anti-vibration pad
743/.90
Ball/plug valve
The individual parts of the pump set are shown in the product literature of the pump
set.
Summary of Contents for Delta Eco SVP
Page 66: ......
Page 67: ......
Page 68: ...KSB B V Kalkovenweg 13 2401 LJ Alphen aan den Rijn Netherlands 1983 821 01 EN ...