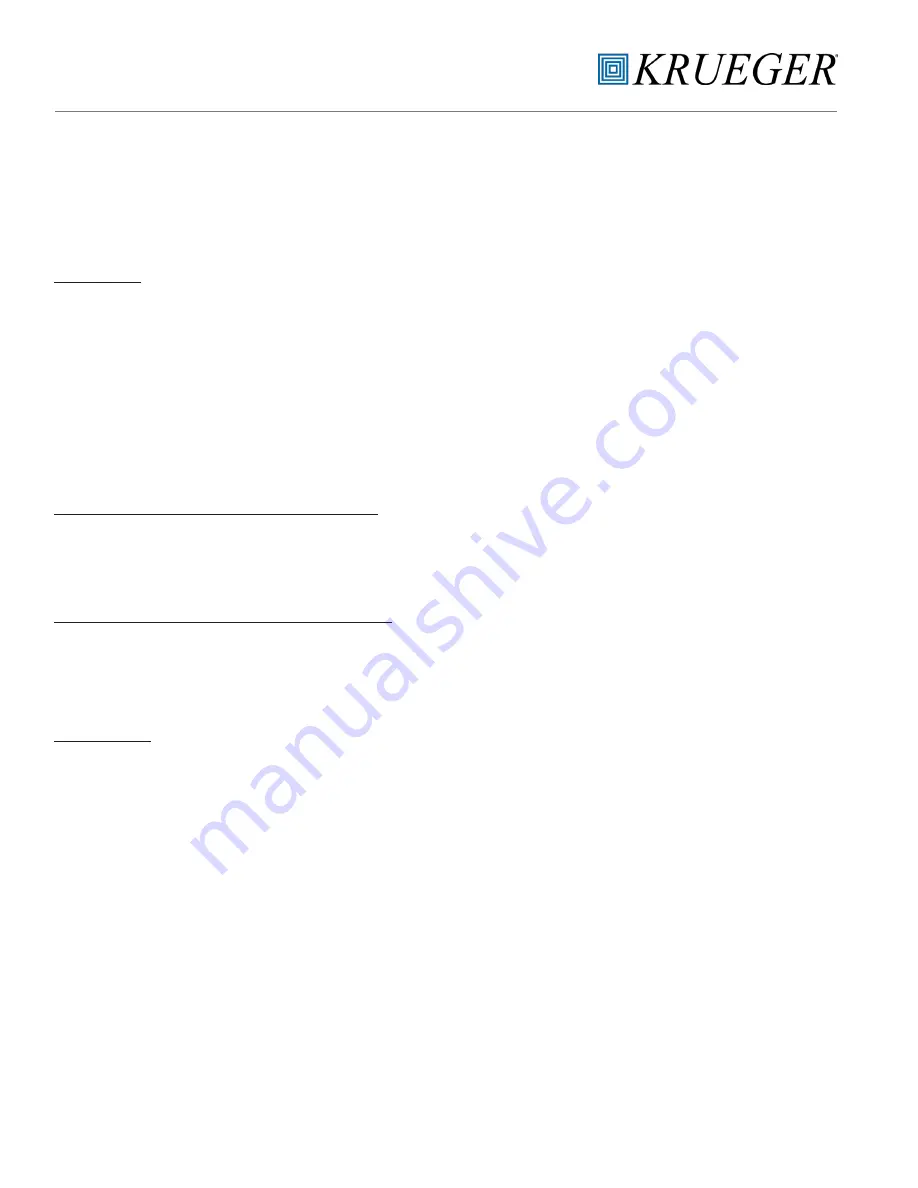
46
Fan Powered Terminal Units IOM
ANALOG CONTROL TROUBLESHOOTING
The following troubleshooting guide is directed towards
single duct cooling applications, the same concepts can be
applied to other configurations.
NOTE: For about 15 seconds after power is applied, no
rotation occurs and one or both of the LEDs will flash.
CONTROLLER
1. Check that the shaft moves freely. (Press and hold the
actuator release clutch and manually rotate the shaft.)
2. Check wiring. (See Wiring Issues section below.)
3.
Check for a tripped circuit breaker to the transformer, for
proper supply voltage from the transformer (or power
supply), and for enough capacity (VA) for all connected
devices.
4. Check that the direction jumper is in the proper position.
5.
Check the polarity and level of the input signal from the
thermostat.
WRONG ROTATION DIRECTION OR STROKE RANGE
1. Check the position of the direction jumper.
2.
Check the Min and Max flow limits on the thermostat
3.
Check the adjustable stop position.
NO PRESSURE OUTPUT SIGNAL FROM INLET SENSOR
1. Check the wiring.
2.
Check air flow and sensor. Tubing should be free of kinks
and restrictions. Sensor must be oriented in the correct
airflow direction.
WIRING ISSUES
1. Check for correct wiring at unit and thermostat.
2. At the Controller, verify 24 VAC at terminals “~” (phase)
and “-” (ground). Tolerance can be –15% to +20% (20.4 to
28.8 VAC).
3.
Verify 16 VDC at terminals “16 VDC” and “COM”
a.
Tolerance is 15.0 to 17.0 VDC power supply to
thermostat.
b. If not correct, disconnect thermostat and recheck.
c. If still incorrect, replace CSP controller.
4.
Check “Requested Flow” voltage on terminal “2-10 IN” and
“COM“.
e.
Use Table 7 to correlate into cubic feet per minute
(CFM)
f. If reading is not what is desired, see “calibration to
adjust thermostat.
NOTE: Never jumper terminal 16 VDC to “-” as this would
cause a short, and possibly damage the power supply
NOTE: When using the same transformer for more than
one control, the phase and ground must be consistent
with each device.
WATER VALVE INSTALLATION
WARNING: Disconnect power before wiring or electrical
shock and personal injury could result.
Water valves are field supplied. Most control manufacturers
offer three different hot water valve applications; on/off
and floating point, and proportional control. The controls
contractor should provide water valve specs used on
controls supplied by others. To connect the field-supplied
water valves to the controller, refer to the wiring labels for
the control package.
SERVICE
CONTROLS
No periodic preventive maintenance is necessary.
FAN MOTOR AND WHEEL
The fan motor and wheel are accessible from the bottom of
the unit. Remove the bottom panel to check the wiring or
remove the fan wheel or motor.
The PSC motors are equipped with long life sleeve bearings
with non-detergent SAE (Society of AutomotiveEngineers)20
oil. Do not add oil to motors.
NOTE: The EC motor has permanently lubricated ball
bearings that require NO maintenance.
TO CHECK WIRING (REFER TO FIG 14-16, NEXT PAGE)
The PSC motor is connected by quick-connect terminals to
the capacitor (brown wire), the housing wire (green ground
wire), and the control box (black wire and white wire). Verify
that the fan motor wiring is correct as shown in these figures.
Summary of Contents for KLPP
Page 49: ......