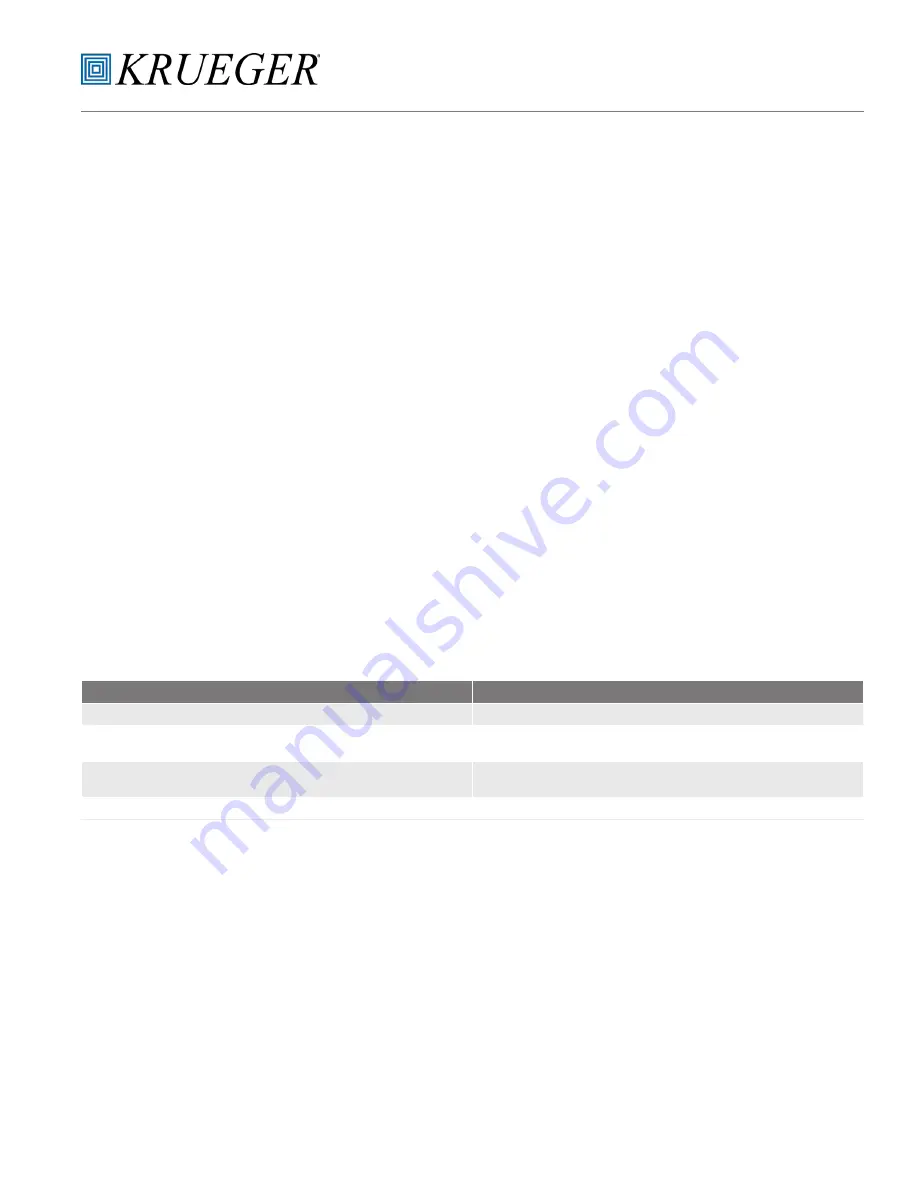
43
Fan Powered Terminal Units IOM
PROBLEM
LIKELY CAUSE
Controller does not reset to maximum minimum set point during balancing procedure
Thermostat signal is being used for control signal. An artificial signal must be used.
Controller does not reset to maximum or point during operation
Thermostat is not demanding minimum set maximum or minimum air volume. Main air pressure at the
controller is less than 15 psi.
Pneumatic actuator does not stroke fully
Leak in pneumatic tubing between the controller and the actuator. Main air pressure at the controller
is less than 15 psi. Leak in the actuator diaphragm.
Air valve stays in wide open position
Differential pressure sensor is blocked or obstructed. Insufficient supply air pressure in the unit inlet.
TABLE 33 – Troubleshooting Pneumatic Controls
inducing plenum air and mixing it with the cold primary
air. The KLPP, QFV & KQFP fan will not induce any plenum
air at this point.
3.
When the thermostat is modulating between maximum
heating demand and satisfied setpoint, the primary air
damper will be at the minimum air volume setting. A
maximum amount of plenum air is induced at this point.
In sequence, the first and second stages of electric reheat
will energize, if supplied. If hot water heating coils are
supplied, they will either open fully or modulate open.
4. During thermostat demand for maximum heating,
primary air will flow through the unit at the preset
minimum setting, maximum amount of plenum air will
be induced, and heating coils, if supplied, are full on. See
Table 33 for Pneumatic Control Troubleshooting.
5. Adjust the “HI STAT” knob, with a 15 psi thermostat signal,
to obtain the desired airflow setting. Depending on the
control sequence desired, the “HI STAT” knob will vary
either the minimum setting or the maximum setting as
follows:
DANC — “HI STAT” knob adjusts the maximum setting
RANC — “HI STAT” knob adjusts the minimum setting
DANO — “HI STAT” knob adjusts the maximum setting
RANO — “HI STAT” knob adjusts the minimum setting
6. To adjust the thermostat reset start point, remove gage
port (“G”) cap and attach a 0 to 30 psi pressure gage
and note the pressure reading. Adjust the thermostat
pressure to the controller, “T” port to the desired start
point. Adjust the “RESET START” knob until the gage
pressure begins to change slightly. Remove pressure
gage and replace cap.
7. To adjust the thermostat reset span from standard 5
psi, remove gage port (“G”) cap and attach a 0 to 30 psi
pressure gage and note the pressure reading. Adjust
the thermostat pressure to the controller “T” port to the
desired start point. Adjust the “RESET SPAN” knob until
the gage pressure equals the desired reset span. Remove
gage and replace cap.
8. To change logic from a given sequence to another, follow
the steps below:
a. To change from N.O. to N.C. or from N.C. to N.O.,
loosen the “damper” dial screw and rotate the dial
until the desired damper position indicator is aligned
with the arrow. The VAV damper must be physically
changed to desired position.
b. To change from DA to RA or from RA to DA, no
configuration changes are required — use the
appropriate calibration procedures from above.
9.
Reconnect the power to the blower motor on the KLPP,
QFV & KQFP units.
NOTES:
1. The multi-function control system uses a Krueter
CSC 3000 series velocity controller with a rated air
consumption of 1.00 SCFH at 20-psi main air pressure.
2. The maximum and minimum limits are both changed
when adjusting the center knob. The center knob should
always be set first.
Summary of Contents for KLPP
Page 49: ......