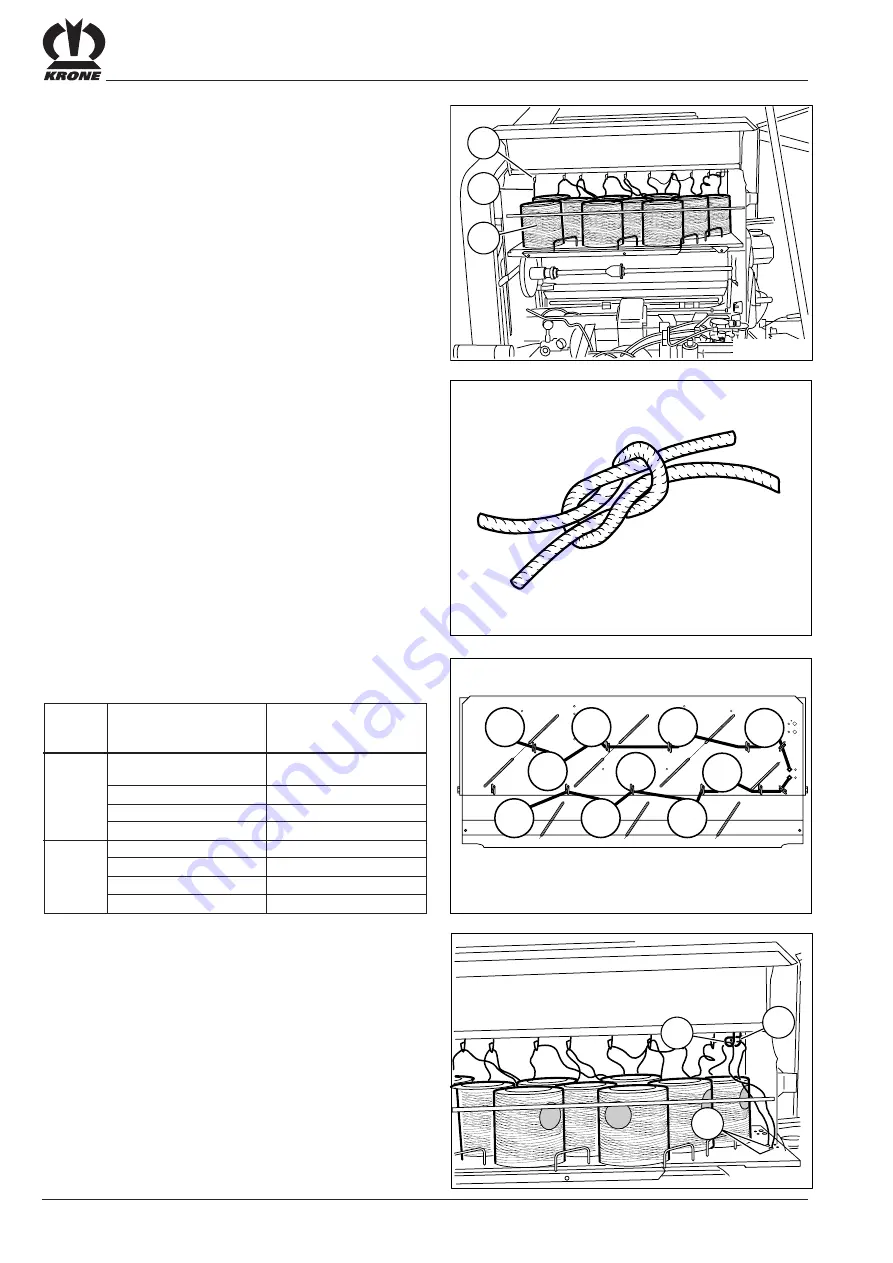
V - 8
Basic Settings and Operation
5.8.4 Inserting Twine
The twine box can hold up to 10 rolls of twine (1).
Threading the twine
Before knotting the roll of twine (1), thread the twine (3)
through the corresponding twine guide (2).
Knot the twine as shown in this example.
end of
with start of
roll
roll
1
4
4
7
7
8
8
10
2
3
3
5
5
6
6
9
The rolls of twine are connected as follows:
•
Thread the twine downwards through the twine guides
(1) and the front bore holes (2) inside the twine box.
•
Thread 1 through the back bore hole.
•
Thread 2 through the front bore hole.
thread 1
(back)
thread 2
(front)
KR-1-009
RBV04150
2
3
1
10
7
4
1
2
3
5
6
8
9
RBV00241
RBV04142
1
1
2
Summary of Contents for Vario Pack 1510
Page 8: ...I 4 General Information ...
Page 20: ...II 12 Safety ...
Page 75: ...VIII 17 Maintenance 942 357 1 8 10 2 Lubrication Points on the Round Baler right hand side ...
Page 78: ...IX 2 Winter Storage ...
Page 98: ...A 14 Appendix ...
Page 99: ...A 15 Appendix ...