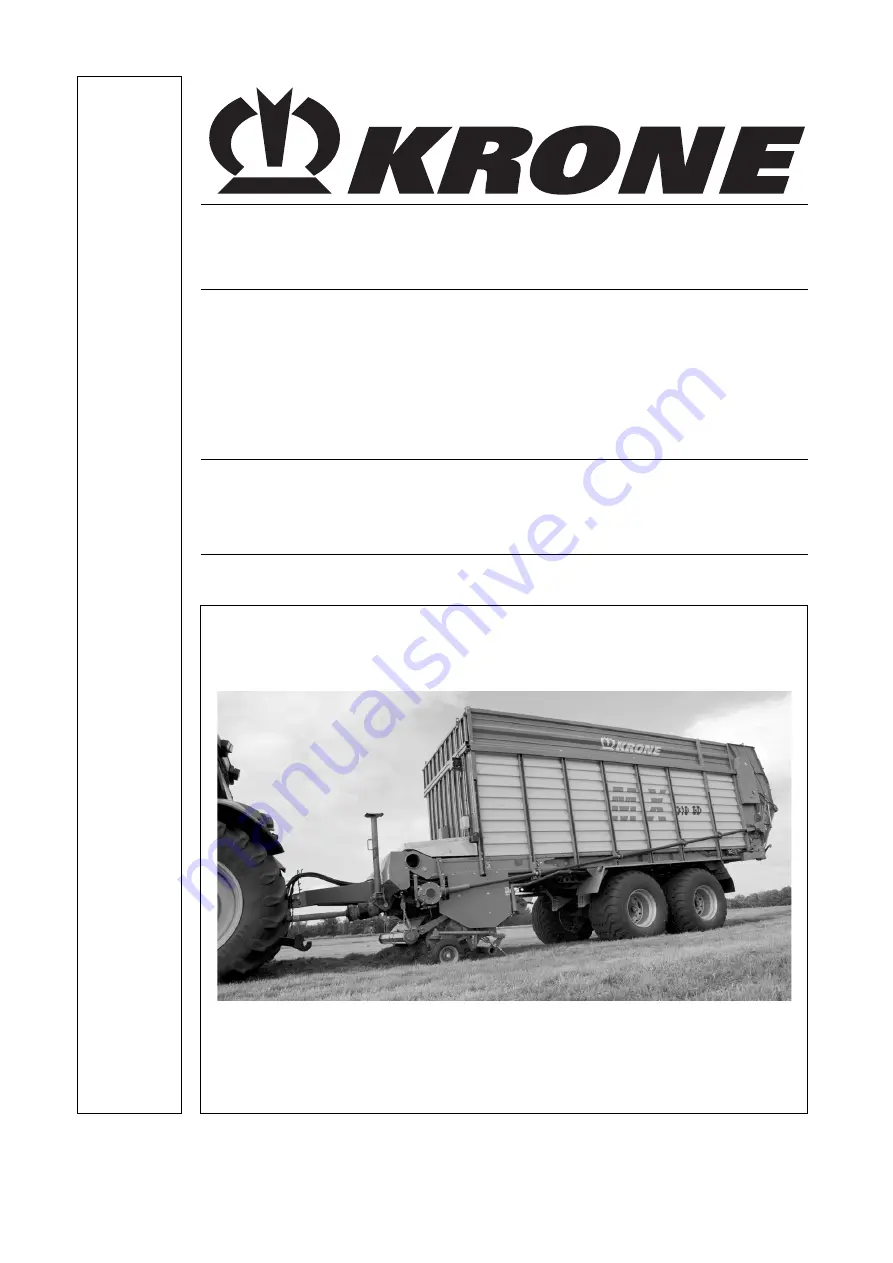
O
r
ig
in
a
l
o
p
e
r
a
t
in
g
i
n
s
t
r
u
c
t
io
n
s
Short-cut loading wagon / Short-cut
feeder wagon
<v>T - Typ1</v>
MX 310 GL
</v>
<v>T - Typ2</v>
MX 350 GL
</v>
<v>T - Typ3</v>
MX 310 GD
</v>
<v>T - Typ4</v>
MX 350 GD
</v>
<v>T - Typ5</v> </v>
<v>T - Typ6</v> </v>
<v>T - Typ7</v> </v>
<v>T - Typ8</v> </v>
<v>T - Typ9</v> </v>
<v>T - Typ10</v> </v>
(
<v>T - ab Masch.-Nr.</v>
from serial no.
</v>
: 785 000)
<v>T - Bestell-Nr.</v>
Order no.
</v>
: 150 000 122 02 en
<v>B - Titelbild</v>
</v>
18.03.2010
Summary of Contents for MX 310 GD
Page 20: ...Safety 20 MX000003 7 8 9 7 7 1 2 5 6 6 8 11 4 4 11 9 4 5 3 3 9 4 5 9 GL GD 10 GD GL Fig 3 ...
Page 52: ...Driving and Transport 52 Pos 18 BA Sei tenumbruch 0 mod_1196175311226_0 doc 4165 ...
Page 213: ...Maintenance 213 ...
Page 218: ...Maintenance lubrication chart 218 14 5 Lubrication chart GD MX000006 Fig 148 ...
Page 243: ......