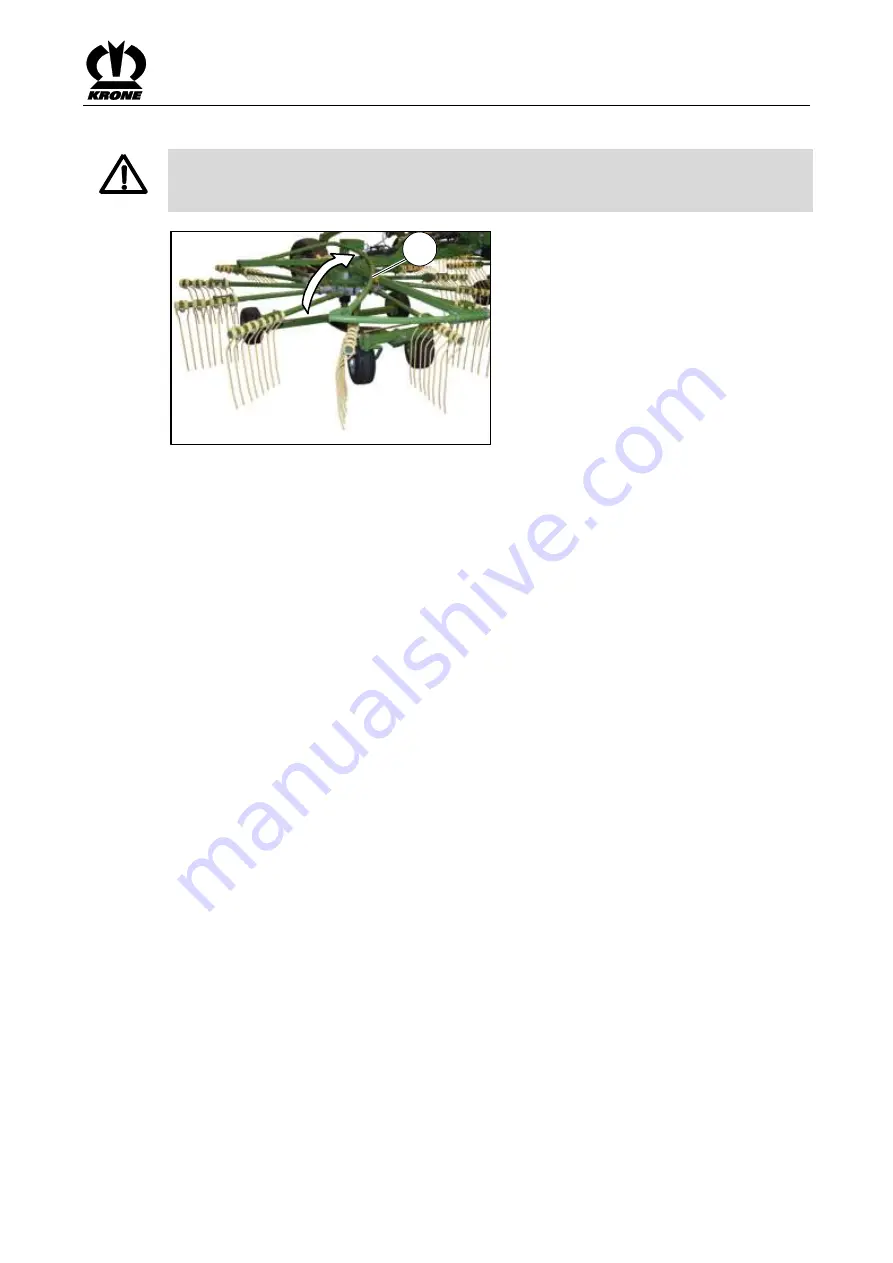
Operation
61
9.8
Move the hoop guards to transport position.
Warning - Crush hazard!
Effect: Injury to hands
Do not hold onto hoop guards to swivel within range of the rotating points.
SW700071_1
1
Fig. 29
• Lower rotor arms into working position.
• Turn off the tractor and secure it against the possibility of rolling back.
• Fold over the hoop guard (1) from working position to transport position.
Summary of Contents for 1 000 245
Page 53: ...Start up 53 1 SW9000042_1 Fig 21 Install the safety chain 1 on the machine ...
Page 75: ...Settings 75 Note If the forage is heavy adjust the inner running gear as low as possible ...
Page 78: ...Settings 78 This page has been left blank deliberately ...
Page 86: ...Maintenance 86 12 6 Replacing the tine arms in case of repair SW700041_1 6 3 1 2 Fig 45 ...
Page 104: ...150102179_00 1 2 2 1 2 ...
Page 107: ......