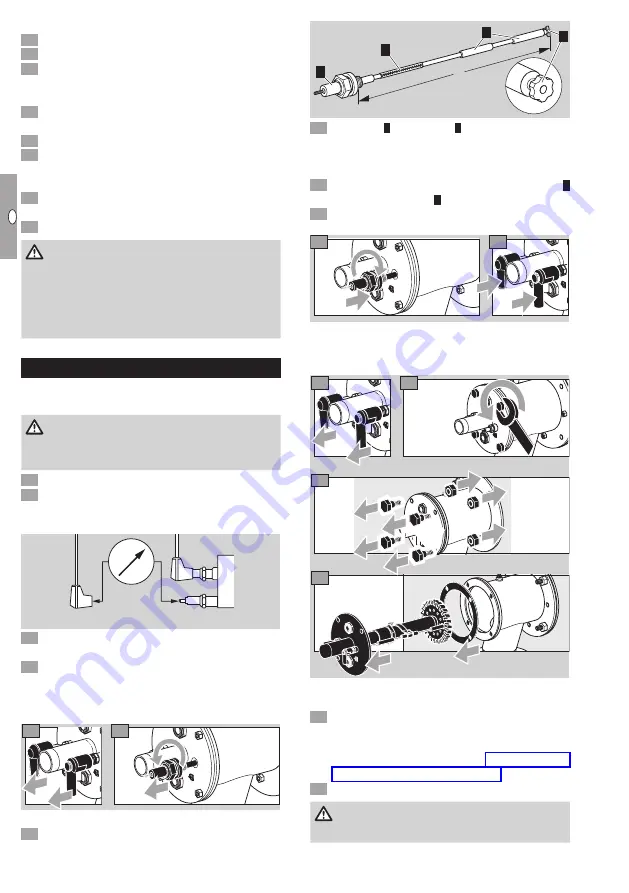
GB-10
D
GB
F
NL
I
E
Blocking and recording the settings
Produce a measurement report.
Set the burner to low fire and check the settings.
Set the burner to low and high fire several times
while monitoring the pressure settings, flue gas
values and flame patterns.
4
Remove the measuring devices and close off
the test nipples – tighten the grub screws.
5
Block and seal the adjusting elements.
6
Induce a flame failure, e.g. by pulling the plug off
the ionization electrode. The flame detector must
close the gas safety valve and signal a fault.
7
Switch the system on and off several times while
monitoring the automatic burner control unit.
8
Produce an acceptance report.
DANGER
An incorrect change of the burner settings may
change the gas/air ratio and lead to unsafe oper-
ating conditions. Risk of explosion in case of CO
being formed in the furnace chamber! CO is odour-
less and poisonous!
Maintenance
We recommend that a function check is carried out
every six months.
WARNING
Risk of burning! Outflowing flue gases and burner
components are hot.
Check the ionization and ignition cables.
Measure the ionization current.
▷
The ionization current must be at least 5 µA and
must not vary.
+
μ
A
–
Z
I
Disconnect the system from the electrical power
supply.
4
Shut off the gas and air supply – do not change
the restrictor settings.
Checking the ignition and ionization
electrodes
6
5
▷
Ensure that the electrode length does not change.
7
Remove dirt from electrodes or insulators.
L
1
2
3
4
8
If the star
4
or insulator
is damaged, replace
the electrode.
▷
Before changing the electrode, measure the
total length
L
.
9
Connect the new electrode with the spark plug
using the dowel pin
.
0
Adjust spark plug and electrode to the measured
total length
L
.
11
12
▷
Turning the spark plug makes it easier to feed
the electrode into the burner insert.
Checking the burner
16
13
14
15
▷
If the burner insert is dismantled, the gas housing
gasket will have to be renewed.
7
Place the burner insert in a safe place.
▷
Depending on the amount of dirt or wear: replace
the ignition/ionization electrode rod and dowel
pin during servicing – see page 10 (Checking the
ignition and ionization electrodes).
8
Check burner head for dirt and thermal cracks.
WARNING
Risk of injury! Burner heads have sharp edges.