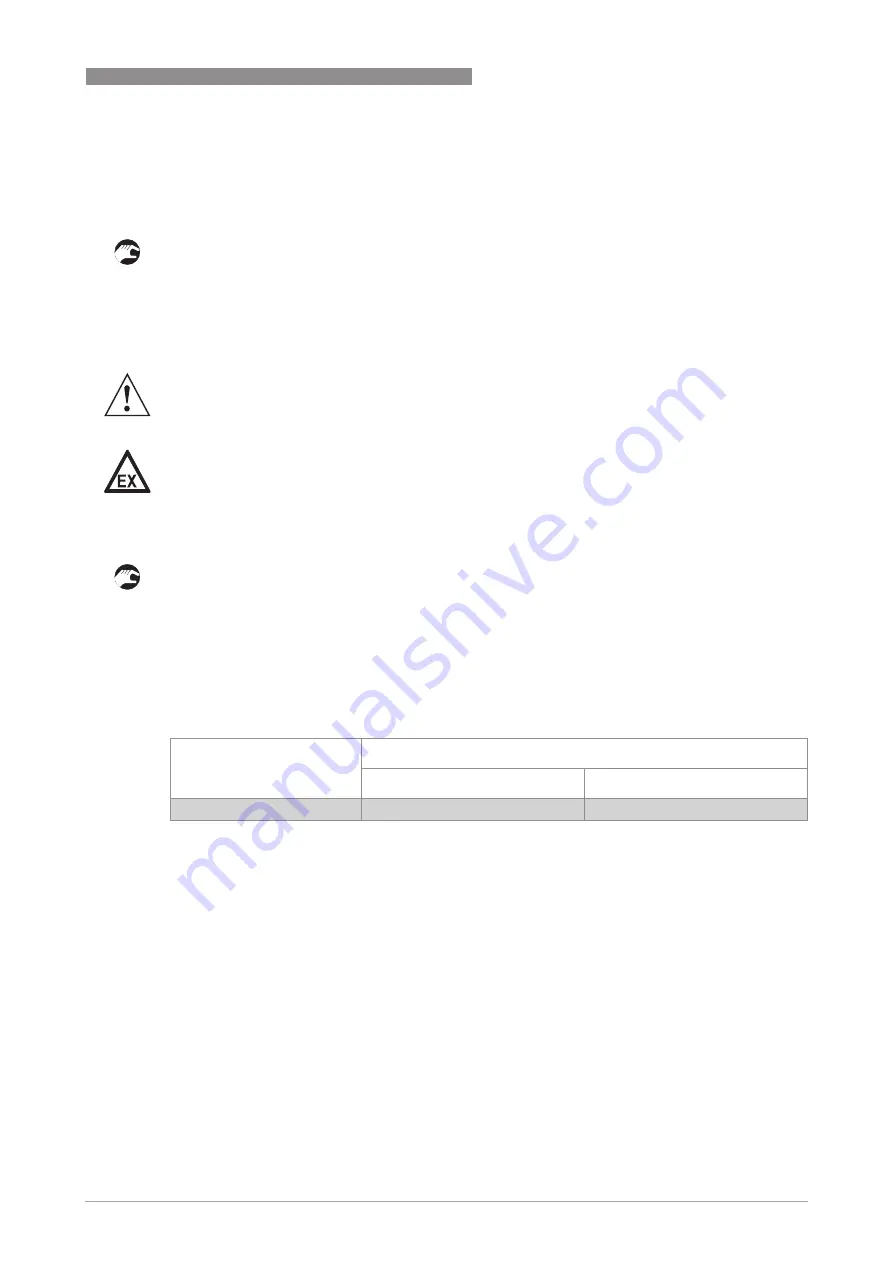
ELECTRICAL CONNECTIONS
3
19
OPTIWAVE X400
www.krohne.com
10/2017 - 4006413501 - AD NEPSI OPTIWAVE x400 R01 en
Equipment needed
•
Wrench (supplied)
•
3 mm Allen wrench (not supplied)
•
Use the 3 mm Allen wrench to remove the cover stop.
•
Use the wrench to remove the cover.
For more data about the procedure, refer to the handbook.
3.2.2 How to close the terminal compartment
•
Attach the cover. Make sure that a slot on the top of the cover is correctly aligned with the hole
for the cover stop.
•
Attach the cover stop (make sure that there is also a spring washer and a socket head screw).
Tighten the screw with a 3 mm Allen wrench.
3.3 Terminal tightening capacity
The terminal tightening capacity for current output terminals is:
WARNING!
If dirt collects on the terminal compartment gasket, clean it before you attach the terminal
compartment cover. Lubricate the gasket with a mutli-purpose grease (e.g. UNIMOLY
®
C 220).
DANGER!
Ex d applications
Ex d applications
Ex d applications
Ex d applications
Make sure that the terminal compartment is sealed and its cover is fully engaged. An explosion
can cause death or injury to personnel and/or damage to equipment. Obey the instructions that
follow:
Type of wire
Terminal tightening capacity
[mm
²
]
[AWG]
Flexible
3.3
12