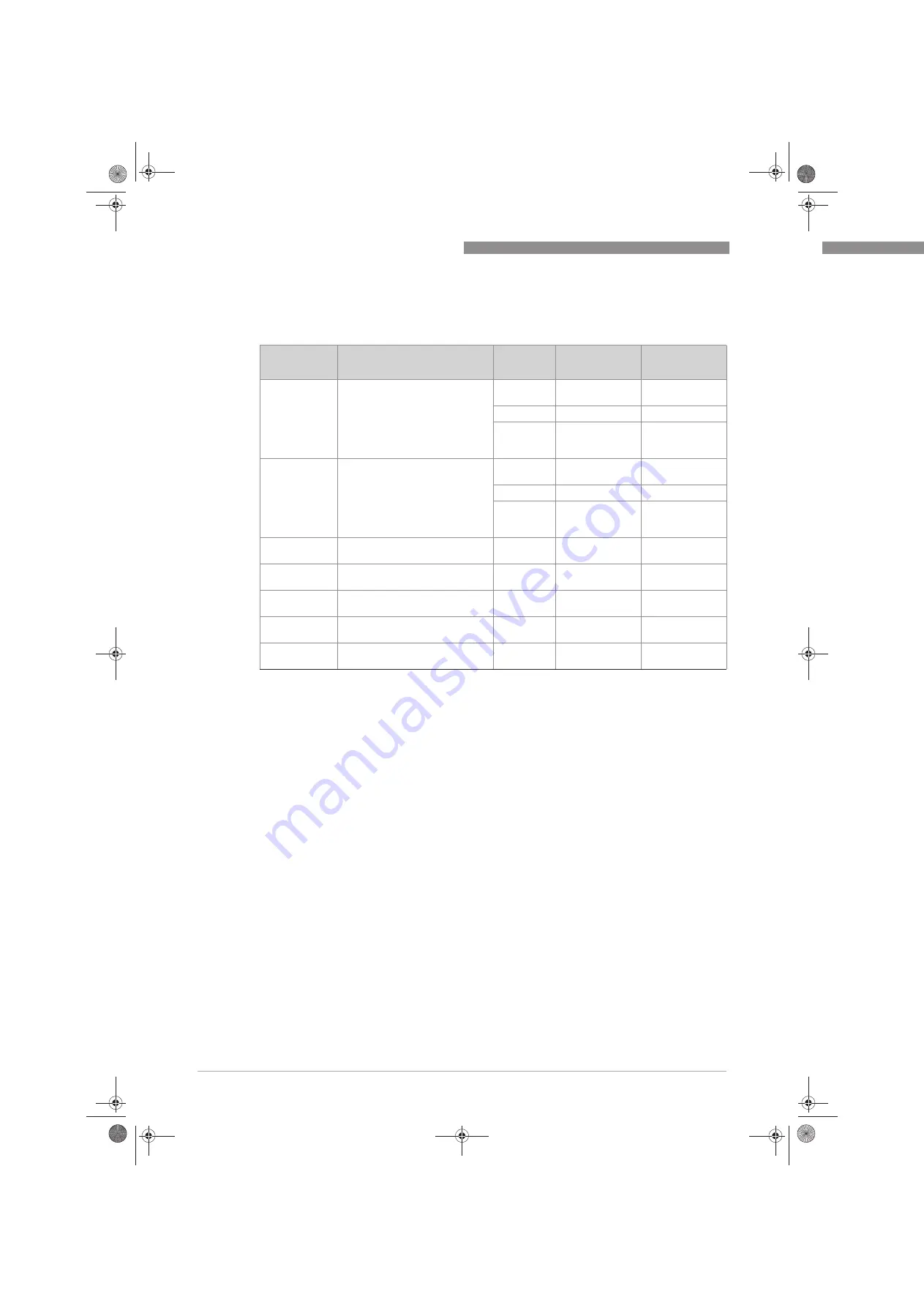
4
COMMISSIONING / OPERATION
16
H250 M40 ESK4
www.krohne.com
03/2014 - 4002251801 - AD H250/M40 PROFIBUS R01 en
4.4 Summary
The following table shows a summary of the supported combinations:
4.5 Configuration of cyclic data transfer
During network configuration the user has to select which function block input/output data shall
be transferred between the PROFIBUS master and the PROFIBUS slave. The GSD file described
above contains several types of modules for this purpose. During configuration a module has to
be assigned to each slot of the device in order to select which data has to be transferred for the
corresponding function blocks. The cyclic layout (see section Ident. Number selector) shows
which module types are valid for each slot. The order of transmission of the data always remains
the same. If an
“
Empty Module
”
is assigned to a slot no data will be sent for the corresponding
function block and all function block data following this empty module will move up one position.
Calibration
Ident. Number Selector
Ident.
Number
GSD File
Status
Flow
Automatic adaptation mode
4531
KR014531.GSD
classic
condensed
9740
PA139740.GSD
1
classic
F201
KROHF201.GSD
YP01F201.GSD
classic
Level
Automatic adaptation mode
4531
KR014531.GSD
classic
condensed
9700
PA139700.GSD
1
classic
F201
KROHF201.GSD
YP01F201.GSD
classic
Flow/Level
Manufacturer specific Ident.
Number (4531hex)
4531
KR014531.GSD
classic
condensed
Flow
Profile specific Ident. Number
(9740hex)
9740
PA139740.GSD
1
classic
Level
Profile specific Ident. Number
(9700hex)
9700
PA139700.GSD
1
classic
Flow/Level
Compatibility mode (ESK3-PA:
F201hex)
F201
KROHF201.GSD
YP01F201.GSD
classic
Flow/Level
Compatibility mode (Profile:
9740hex)
9740
PA139740.GSD
1
classic
1
This file is provided by PROFIBUS International (see www.profibus.com)
AD_H250_M40_PB_PA_R01_en_4002251801_PRT.book Page 16 Friday, March 21, 2014 1:14 PM