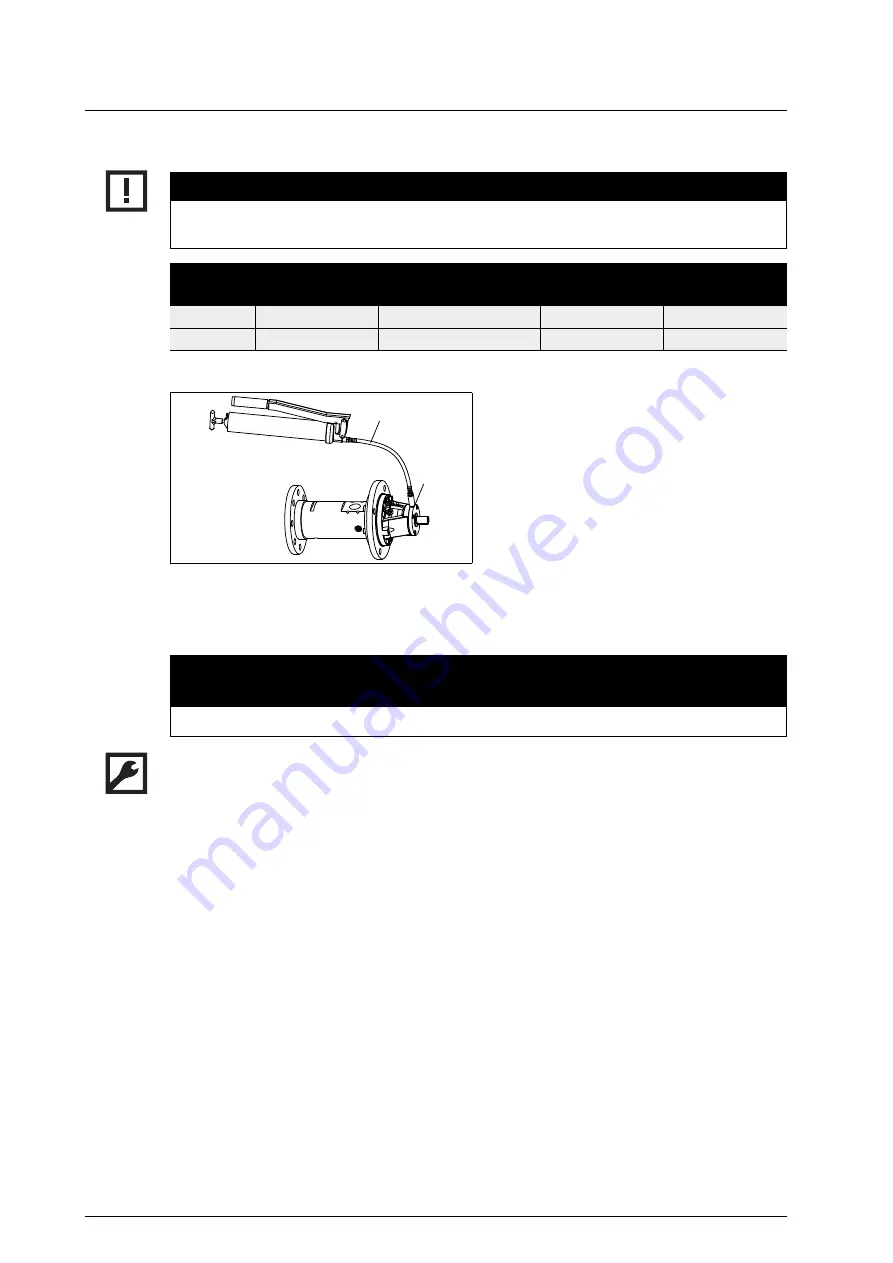
Operating Instructions
OIC 12en Edition 08/2016
29
Lubricating the ball bearings
Servicing
Lubricating the ball bearings
Tab. 4 Lubricating intervals of ball bearings
Aids:
□
Grease gun
► Re-lubricate the ball bearing with the recommended amount of grease via the grease nipple
B
.
Be sure to observe the following instructions:
► Re-lubrication may only be carried out while the pump is running.
► First re-lubrication after an hour running time.
Size
Temperature [°C]
Lubricate interval [h] with
speed 1450 min
-1
Grease amount
[cm
3
]
Recommended
grease
CLC 55
100
7500
6
SKF LGWA 2
CLC 550
100
6000
16
SKF LGWA 2
A
Grease gun
B
Grease nipple of ball bearings
Fig. 6
Lubricating the ball bearings
A
B
CAUTION
Damage to bearing because of lack of lubrication.
► It is imperative that the lubrication intervals be observed.