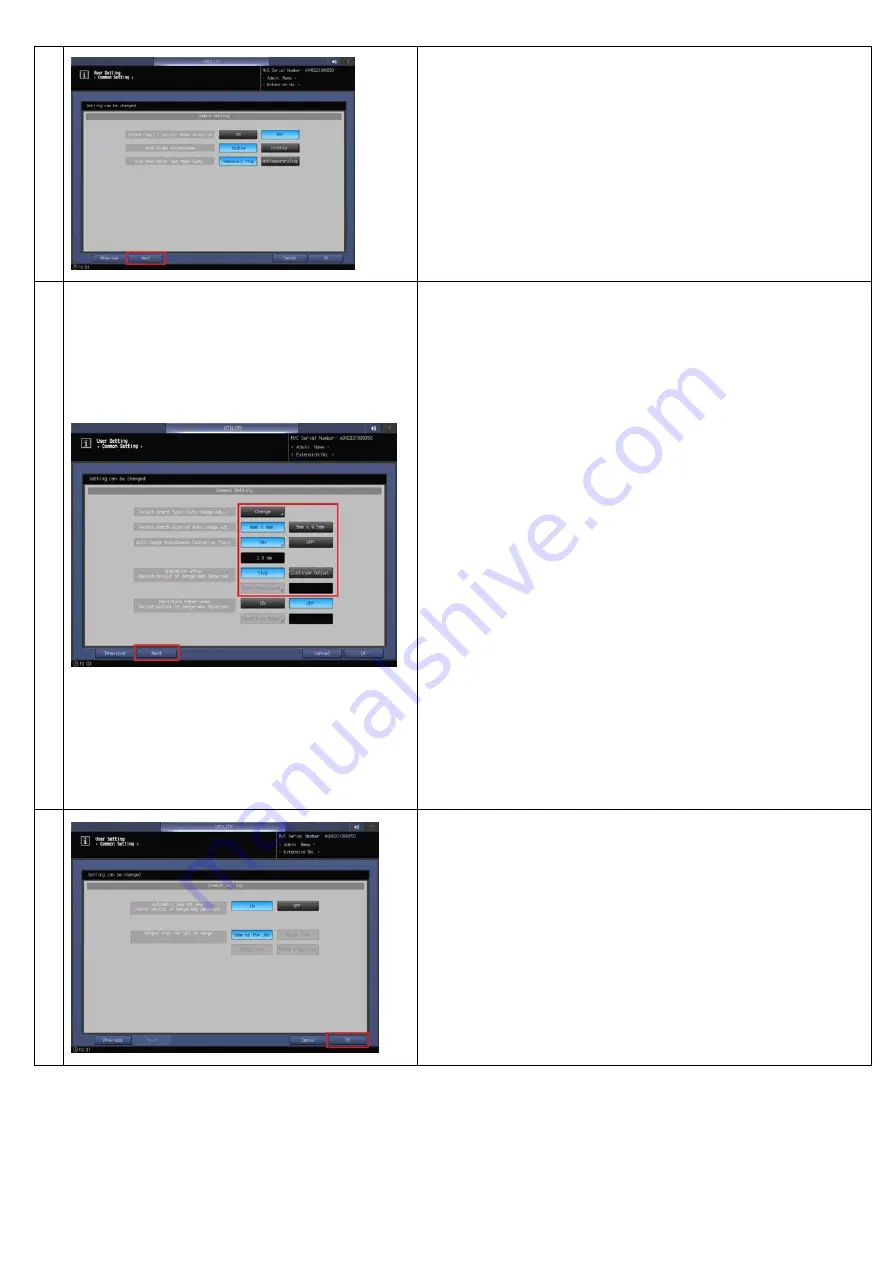
2/27/2020 5:45 PM
/
D11
40
9
Press [Next].
10
Select each item as follows
- [Select Chart Type(Auto Image Adj.)]
[62-74g/m2]/[16-19 lb Bond]:
[Type1]
[75-80g/m2]/[20-21 lb Bond]:
[Type1]
[81-91g/m2]/[22-24 lb Bond]:
[Type1]
[92-105g/m2]/[25-28 lb Bond]:
[Type1]
[106-135g/m2]/[29-36 lb Bond]:
[Type1]
[136-176g/m2]/[37-47 lb Bond]:
[Type1]
[177-216g/m2]/[48-57 lb Bond]:
[Type2]
[217-256g/m2]/[58-68 lb Bond]:
[Type2]
[257-300g/m2]/[69-81 lb Bond]:
[Type2]
[301-350g/m2]/[82-93 lb Bond]:
[Type2]
- [Switch Patch Size of Auto Image Adj.]
> [
6mm x 8 mm
]
- [Auto Image Adjustment Deviation
Check] > [
ON/2.0 mm
]
- [Operation after Deviation of Range was
Detected] > [
Stop
]
Press [Next].
11
Press [OK].