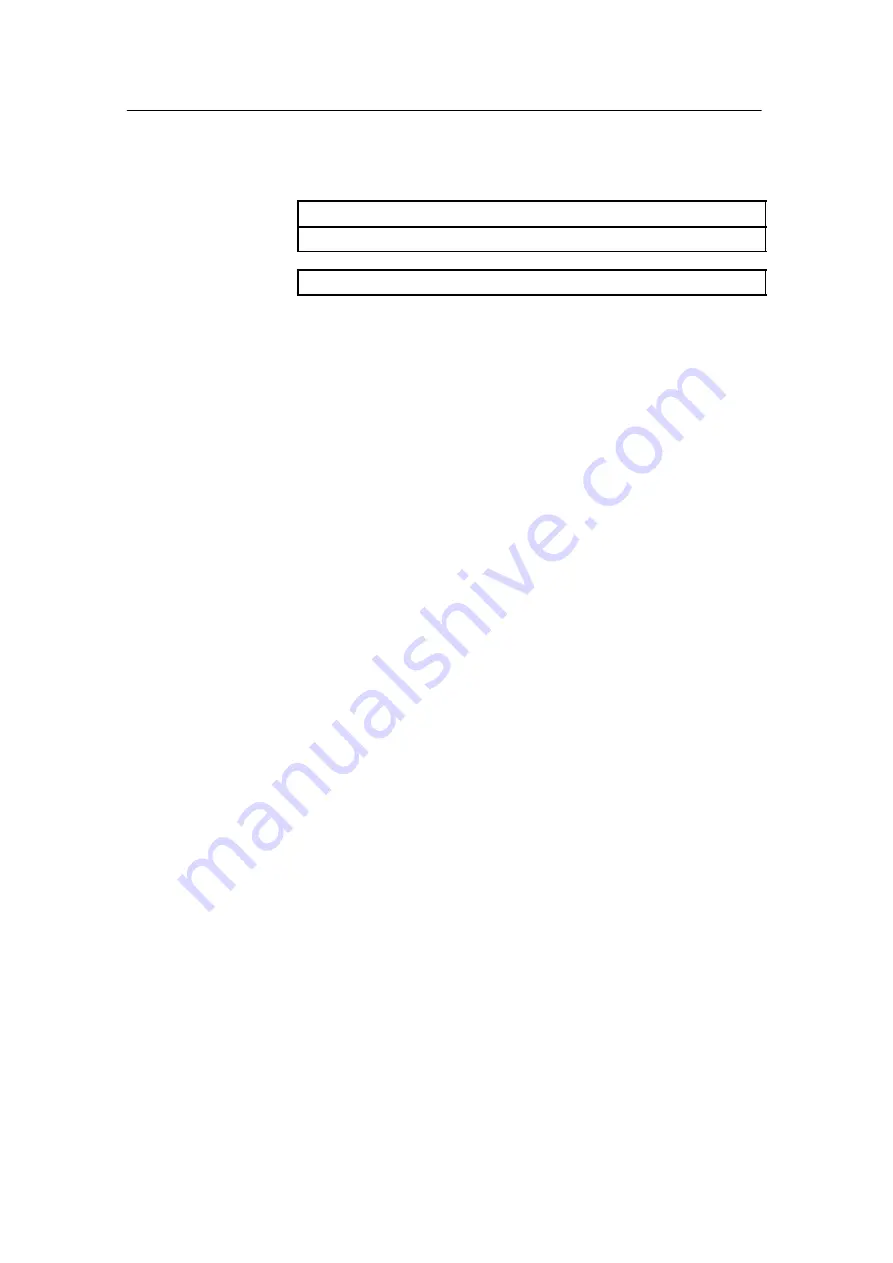
Installation Manual
3
130314 / F
Humidity:
Storage
90% relative
Operational
80% relative
Degree of protection (in cabinet)
IP 22
If the HPR 400 Transceiver Unit is mounted in a 19” rack, the
appropriate protection must be prepared by the installation
personnel.
The unit must be kept in an operational environment with the
room temperature and humidity within the specified limits, and
in a dust-free atmosphere.