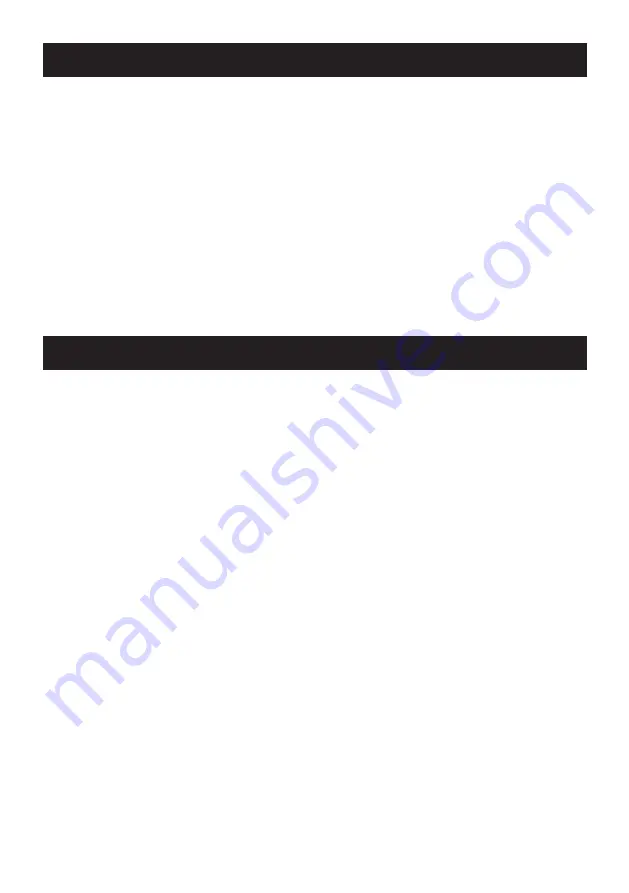
3
1058907-W2-J
The function of this thermostatic mixing tap is to deliver water consistently at a safe
temperature. This requires that:
1.
It is installed, commissioned, operated and maintained in accordance with the
recommendations given in this Manual.
2.
For Type 3 installations, valves are only to be used for applications covered by
their approved designations, refer to the TMV3 Requirements Manual.
3.
Periodic attention is given, as necessary, to maintain the product in good functional
order. Recommended guidelines are given in section:
'Maintenance
'.
4.
Continued use of this product in conditions outside the specification limits given
in this Manual can present potential risk to users.
SAFETY : WARNINGS
The use of the word ‘failsafe’ to describe the function of a thermostatic mixing valve
is both incorrect and misleading. In keeping with every other mechanism it cannot
be considered as being functionally infallible.
Provided that the thermostatic mixing valve is installed, commissioned, operated
within the specification limits and maintained according to this Manual, the risk of
malfunction, if not eliminated, is considerably reduced.
Malfunction of thermostatic mixing valves is almost always progressive in nature
and will be detected by the use of proper temperature checking and maintenance
routines.
Certain types of system can result in the thermostatic mixing valve having excessive
‘dead-legs’ of pipework. Others allow an auxiliary cold water supply to be added
to the mixed water from the mixing valve. Such systems can disguise the onset of
thermostatic mixing valve malfunction.
Ultimately, the user or attendant must exercise due diligence to make sure that the
delivery of warm water is at a stable, safe temperature. This is particularly important
in such healthcare procedures as supervised bathing of patients unable to respond
immediately to unsafe temperatures.
SAFETY : WARNINGS
ADVICE