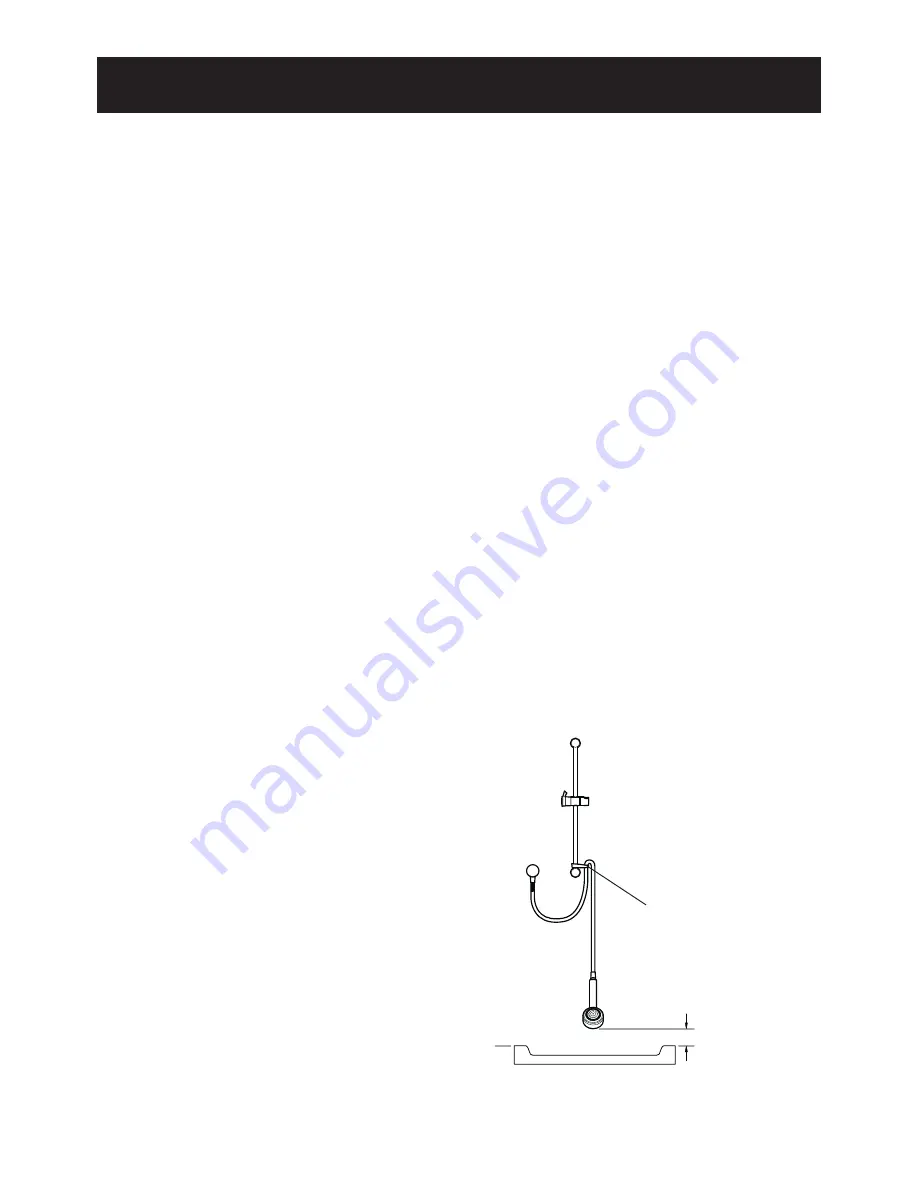
10
INSTALLATION
General
Installation must be carried out in accordance with these instructions, and must be
conducted by designated, qualified and competent personnel.
The installation must comply with the “Water Supply Regulations 1999 (Water Fittings)”
or any particular regulations and practices, specified by the local water company or
water undertakers.
Note!
Make sure that all site requirements correspond to the information given in the
section:
‘Specifications’.
Caution!
The shower must not be installed in an area where it may freeze.
For stud partitions alternative fixings may be required.
1.
Isolating valves must be installed close to the valve for ease of maintenance.
2.
Pipework must be rigidly supported and avoid any strain on the connections.
3.
Pipework dead-legs should be kept to a minimum.
4.
Supply pipework layout should be arranged to minimise the effect of other outlet
usage upon the dynamic pressures at the valve inlets.
5.
Inlet and outlet threaded joint connections should be made with PTFE tape or
liquid sealant. Do not use oil-based, non-setting joint compounds.
6.
To eliminate pipe debris it is essential that supply pipes are thoroughly flushed
through before final connection.
7.
Determine the route for the hot and cold supply pipework and for the outlet pipework.
When connecting to the biv shower fittings it is recommended that the outlet be
positioned above and to one side of the shower control. This is to prevent the
flexible hose from obstructing the temperature and flow knobs of the shower
control.
8.
Decide on a suitable position for the
shower control. The position of the
shower control and the shower fittings
must provide a minimum gap of
25 mm between the spill-over level of
the shower tray/bath and the handset.
This is to prevent back-siphonage. For
further information on the installation
of your shower fittings, refer to the
Discovery Fittings Installation and User
Guide.
Note!
Only use shower fittings
recommended by the manufacturer or
supplier.
Hose Retaining Ring
25 mm Minimum
Spill-over Level