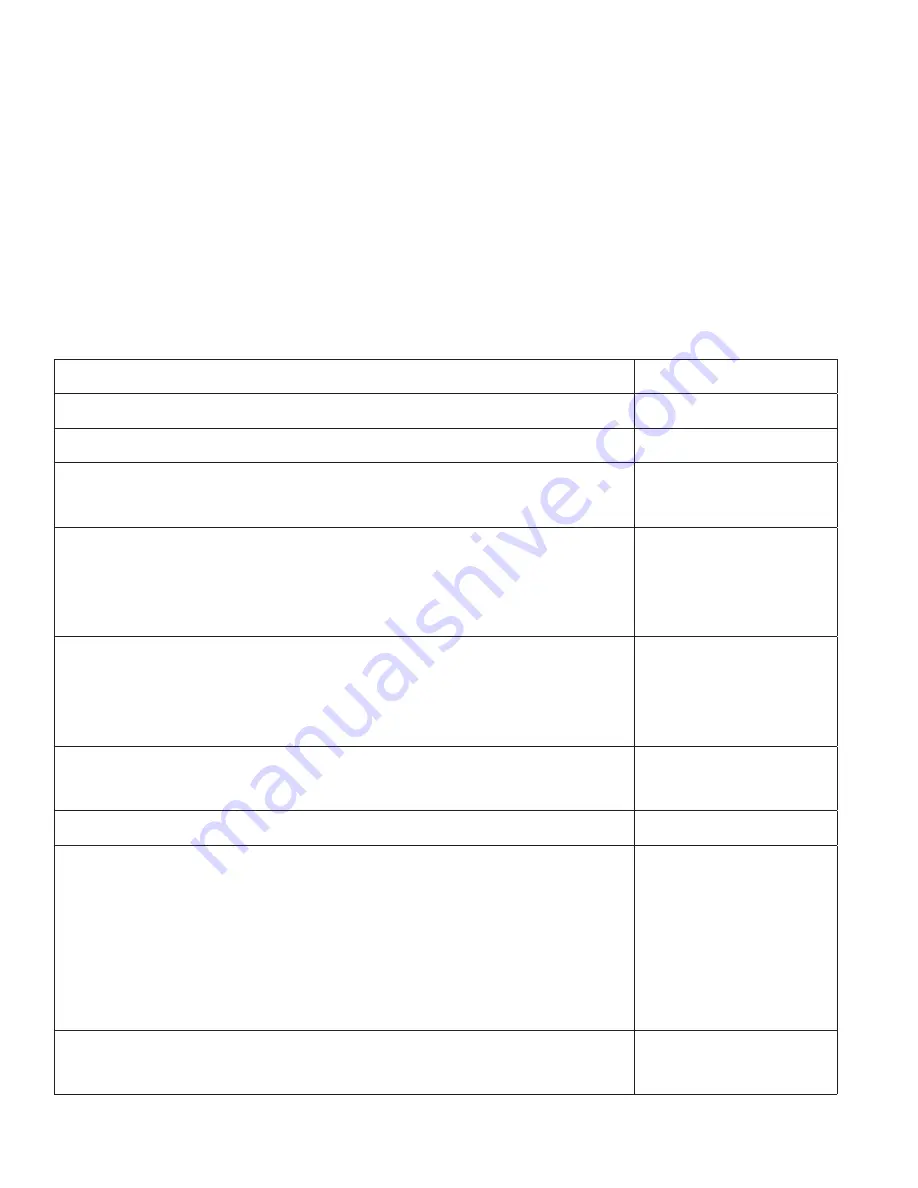
Tools and Aids
18
22 690 01 Rev. --
KohlerEngines.com
Certain quality tools are designed to help you perform specifi c disassembly, repair, and reassembly procedures. By
using these tools, you can properly service engines easier, faster, and safer! In addition, you’ll increase your service
capabilities and customer satisfaction by decreasing engine downtime.
Here is a list of tools and their source.
NOTE: Not all tools listed are required to service this engine.
SEPARATE TOOL SUPPLIERS
Kohler Tools
Contact your local Kohler source of
supply.
SE Tools
415 Howard St.
Lapeer, MI 48446
Phone 810-664-2981
Toll Free 800-664-2981
Fax 810-664-8181
Design Technology Inc.
768 Burr Oak Drive
Westmont, IL 60559
Phone 630-920-1300
Fax 630-920-0011
TOOLS
Description
Source/Part No.
Alcohol Content Tester
For testing alcohol content (%) in reformulated/oxygenated fuels.
Kohler 25 455 11-S
Camshaft Endplay Plate
For checking camshaft endplay.
SE Tools KLR-82405
Camshaft Seal Protector (Aegis)
For protecting seal during camshaft installation.
SE Tools KLR-82417
Cylinder Leakdown Tester
For checking combustion retention and if cylinder, piston, rings, or valves are worn.
Individual component available:
Adapter 12 mm x 14 mm (Required for leakdown test on XT-6 engines)
Kohler 25 761 05-S
Design Technology Inc.
DTI-731-03
Dealer Tool Kit (Domestic)
Complete kit of Kohler required tools.
Components of 25 761 39-S
Ignition System Tester
Cylinder Leakdown Tester
Oil Pressure Test Kit
Rectifi er-Regulator Tester (120 V AC/60Hz)
Kohler 25 761 39-S
Kohler 25 455 01-S
Kohler 25 761 05-S
Kohler 25 761 06-S
Kohler 25 761 20-S
Dealer Tool Kit (International)
Complete kit of Kohler required tools.
Components of 25 761 42-S
Ignition System Tester
Cylinder Leakdown Tester
Oil Pressure Test Kit
Rectifi er-Regulator Tester (240 V AC/50Hz)
Kohler 25 761 42-S
Kohler 25 455 01-S
Kohler 25 761 05-S
Kohler 25 761 06-S
Kohler 25 761 41-S
Digital Vacuum/Pressure Tester
For checking crankcase vacuum.
Individual component available:
Rubber Adapter Plug
Design Technology Inc.
DTI-721-01
Design Technology Inc.
DTI-721-10
Electronic Fuel Injection (EFI) Diagnostic Software
For Laptop or Desktop PC.
Kohler 25 761 23-S
EFI Service Kit
For troubleshooting and setting up an EFI engine.
Components of 24 761 01-S
Fuel Pressure Tester
Noid Light
90° Adapter
Code Plug, Red Wire
Code Plug, Blue Wire
Shrader Valve Adapter Hose
Wire Probe Set (2 pieces regular wire with clip; 1 piece fused wire)
Hose Removal Tool, Dual Size/End (also sold as individual Kohler tool)
K-Line Adapter Jumper Lead Wiring Harness
Kohler 24 761 01-S
Design Technology Inc.
DTI-019
DTI-021
DTI-023
DTI-027
DTI-029
DTI-037
DTI-031
DTI-033
Kohler 25 176 23-S
Kohler Wireless Diagnostic System Module (Bluetooth®)
For wireless Android EFI diagnostics.
Individual component available:
Wireless Diagnostic System Interface Cable
Kohler 25 761 45-S
Kohler 25 761 44-S