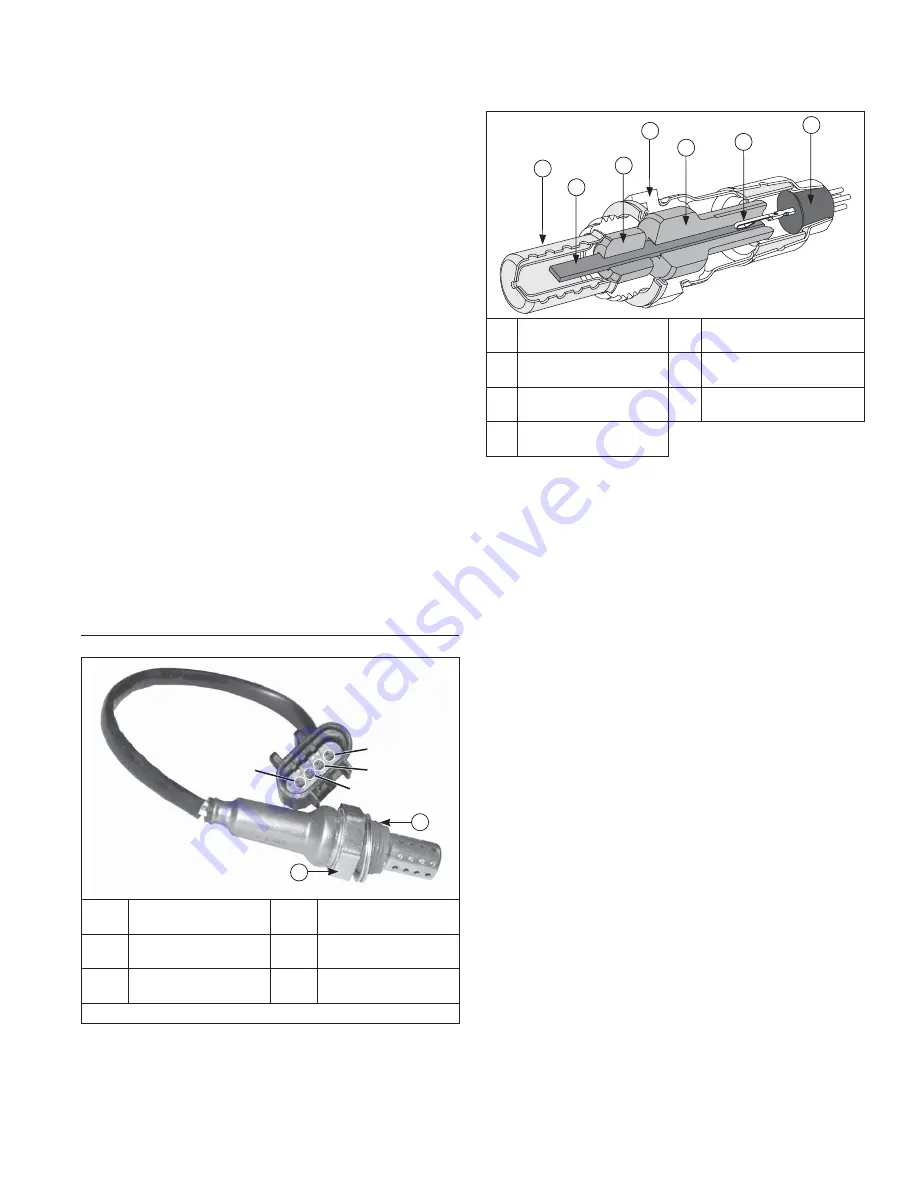
37
EFI SYSTEM
62 690 05 Rev. E
KohlerEngines.com
6. Check circuits (input, ground), from main harness
connector to sensor plug for continuity, damage, etc.
Connect one ohmmeter lead to Black pin 8 in main
harness connector (as in step 4). Connect other lead
to terminal #3 in sensor plug. Continuity should be
indicated. Repeat test between Black pin 10 and
terminal #4 in sensor plug.
7. Reinstall sensor.
If a blink code indicates a problem with Manifold
Absolute Pressure (TMAP) Sensor Circuit (P0107 or
P0108), it can be tested as follows:
1. Make sure all connections are making proper
contact and are free of dirt and debris. Slide locking
tab out and pull off TMAP connector. Turn key switch
to ON and check with a volt meter by contacting red
lead to pin 1 and black lead to pin 2. There should
be 5 volts present, indicating ECU and wiring
harness are functioning.
2. Check continuity in wire harness. Ohms between Pin
3 at sensor connector and Black pin 11 connector at
ECU should be near zero ohms. If no continuity is
measured or very high resistance, replace wire
harness.
3. Check to make sure intake manifold is not loose and
TMAP sensor is not loose. Loose parts would allow
a vacuum leak, making TMAP sensor report
misleading information to ECU.
a. Tighten all hardware and perform an ECU Reset
and a TPS Learn Procedure to see if MIL will
display a fault with sensor again. If MIL fi nds a
fault with TMAP sensor, replace it.
Oxygen Sensor (O2)
Detail
Pin D
Pin C
Pin B
Pin A
A
B
Pin A
Purple Wire,
Pin B
White Wire,
Heater -
Pin C
Black Wire, Sensor
Output
Pin D
Grey Wire, Sensor
Ground
A
22 mm or 7/8 in.
Wrench Size
B
18 mm x 1.5
Thread Size
Installation Torque 50.1 N·m (37 ft. lb.)
Cutaway Oxygen Sensor Components (02)
A
B
C
D
E
F
G
A
Protection Shield
B
Planar Element
and Heater
C
Lower Insulator
D
Stainless Steel
Housing
E
Upper Insulator
F
Terminal Connection
to Element
G
High Temp
Water Seal
Temperature must be controlled very accurately and gas
constituents measured to a high degree of accuracy for
absolute sensor measurements. This requires laboratory
equipment to determine a good or bad sensor in fi eld.
Furthermore, as with most devices, intermittent problems
are diffi cult to diagnose. Still, with a good understanding
of system and sensor, it is possible to diagnose many
sensor problems in fi eld.
Using diagnostic software connected to ECU is a useful
technique for observing sensor performance. However,
user must understand that such software reads a signal
generated by ECU. If there is an ECU or wiring problem,
readings could be misinterpreted as a sensor problem.
Digital nature of signal to software means that it is not
reading continuous output of sensor. A voltmeter can
also be used as an eff ective tool in diagnosing sensors.
It is advisable to use an electronic meter such as a
digital voltmeter. Simple mechanical meters may place
a heavy electrical load on sensor and cause inaccurate
readings. Since resistance of sensor is highest at
low temperatures, such meters will cause largest
inaccuracies when sensor is in a cool exhaust.