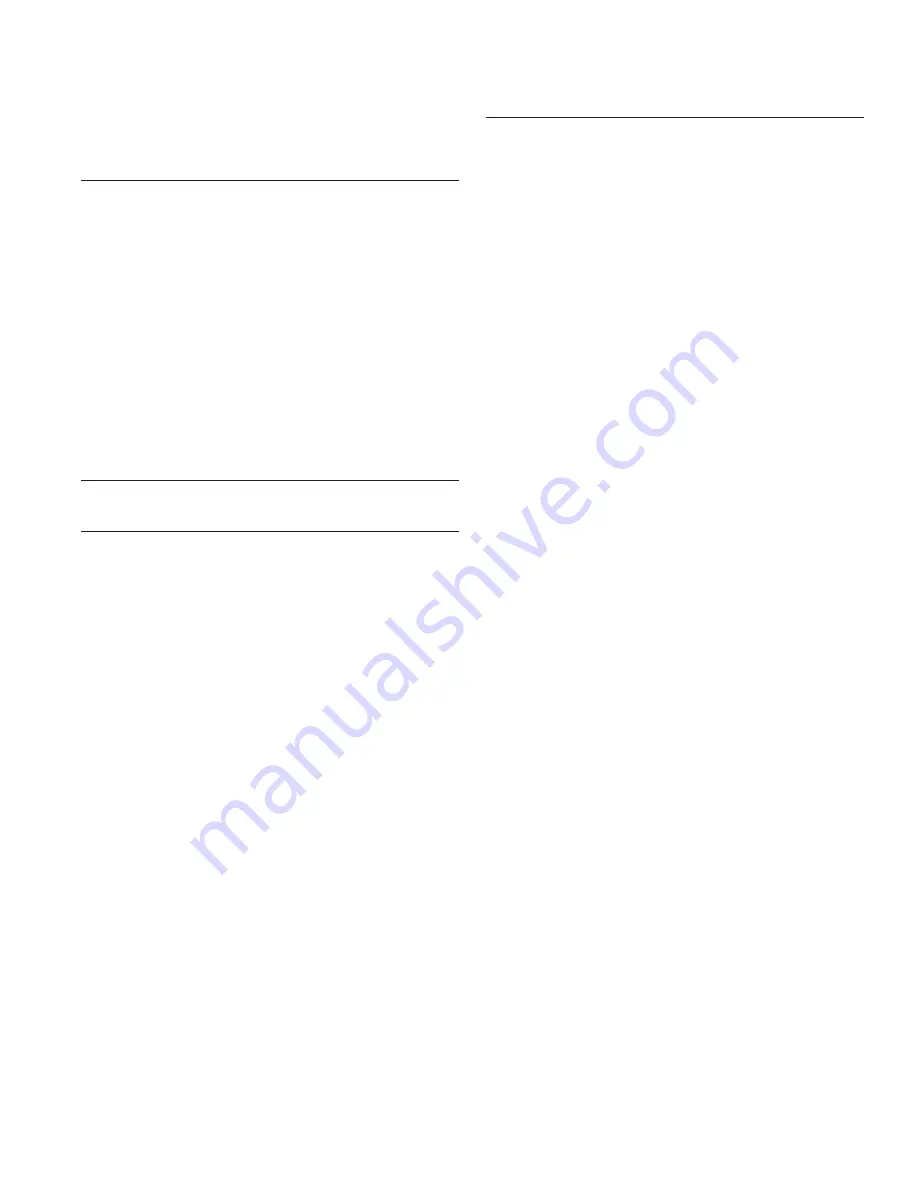
Reassembly
127
62 690 05 Rev. E
KohlerEngines.com
4. Install oxygen sensor, torque to 50.1 N·m (37 ft. lb.)
and connect to wire harness.
5. Install spark arrestor (if used).
Install Oil Filter and Add Oil to Crankcase
NOTE: Make sure both oil drain plugs are installed and
torqued to 21.4 N·m (16 ft. lb.). to prevent oil
leakage.
1. Install oil drain plugs. Torque plugs to 21.4 N·m
(16 ft. lb.).
2. Place new fi lter in shallow pan with open end up. Fill
with new oil until oil reaches bottom of threads. Allow
2 minutes for oil to be absorbed by fi lter material.
3. Apply a thin fi lm of clean oil to rubber gasket on new
fi lter.
4. Refer to instructions on oil fi lter for proper
installation.
5. Fill crankcase with new oil. Level should be at top of
indicator on dipstick.
6. Reinstall oil fi ll cap/dipstick and tighten securely.
Connect Spark Plug Leads
Connect leads to spark plugs.
Prepare Engine for Operation
NOTE: If ECU, throttle body, TPS, or fuel pump module
were replaced, an ECU Reset and TPS Learn is
required. Refer to Electronic Fuel Injection (EFI)
System section.
NOTE: If electronic governor and throttle body were
removed or replaced, refer to Governor section
for proper adjustment/assembly.
Engine is now completely reassembled. Before starting
or operating engine, follow proceeding steps.
1. Make sure all hardware is tightened securely.
2. Make sure oil drain plugs, Oil Sentry
™
pressure
switch, and a new oil fi lter are installed.
3. Verify crankcase has been fi lled with correct amount,
weight, and type of oil. Refer to oil recommendations
and procedures in Maintenance, Specifi cations, and
Lubrication System sections.
4. Turn on fuel supply.
Testing Engine
It is recommended engine be operated on a test stand or
bench prior to installation in equipment.
1. Set engine up on a test stand. Install an oil pressure
gauge. Start engine and check to be certain oil
pressure (20 psi or more) is present. Run engine at
idle for 2-3 minutes, then 5-6 minutes more between
idle and midrange.
2. Adjust idle speed screw located on throttle body as
necessary. Standard idle speed setting for EFI
engines is 1500 RPM, but certain applications might
require a diff erent setting.
3.
Mechanical Governor
: Adjust governed idle and
high speed (RPM) to required settings. Make sure
maximum engine speed does not exceed 3900 RPM
(no load).
Electronic Governor
: Identify design on engine
being serviced, refer to Electronic Governor System
Designs on page 56, and follow the appropriate
procedure below.
Engines with Original Design or Field Installed
Updated Design:
Attach 12 volt jumper wire to
speed control input red wire with yellow tracer.
Engine speed should increase to high. If engine
speed does not increase, refer to Governor section
for proper troubleshooting and diagnostics. Remove
jumper wire and engine speed should decrease and
return to idle speed.
Engines with New Updated Design:
Using E-Gov
Jumper Test Tool (refer to Tools and Aids) is
recommended to perform 12 volt power test. Using a
jumper wire (technician supplied) supply 12 volts (+)
to red w/yellow tracer bullet connector of tool.
Engine speed should increase to high with 12 volt
jumper wire in place. If engine speed does not
increase, refer to Governor section for proper
troubleshooting and diagnostics. Remove jumper 12
volt (+) wire from bullet connector and engine speed
should decrease and return to idle speed.