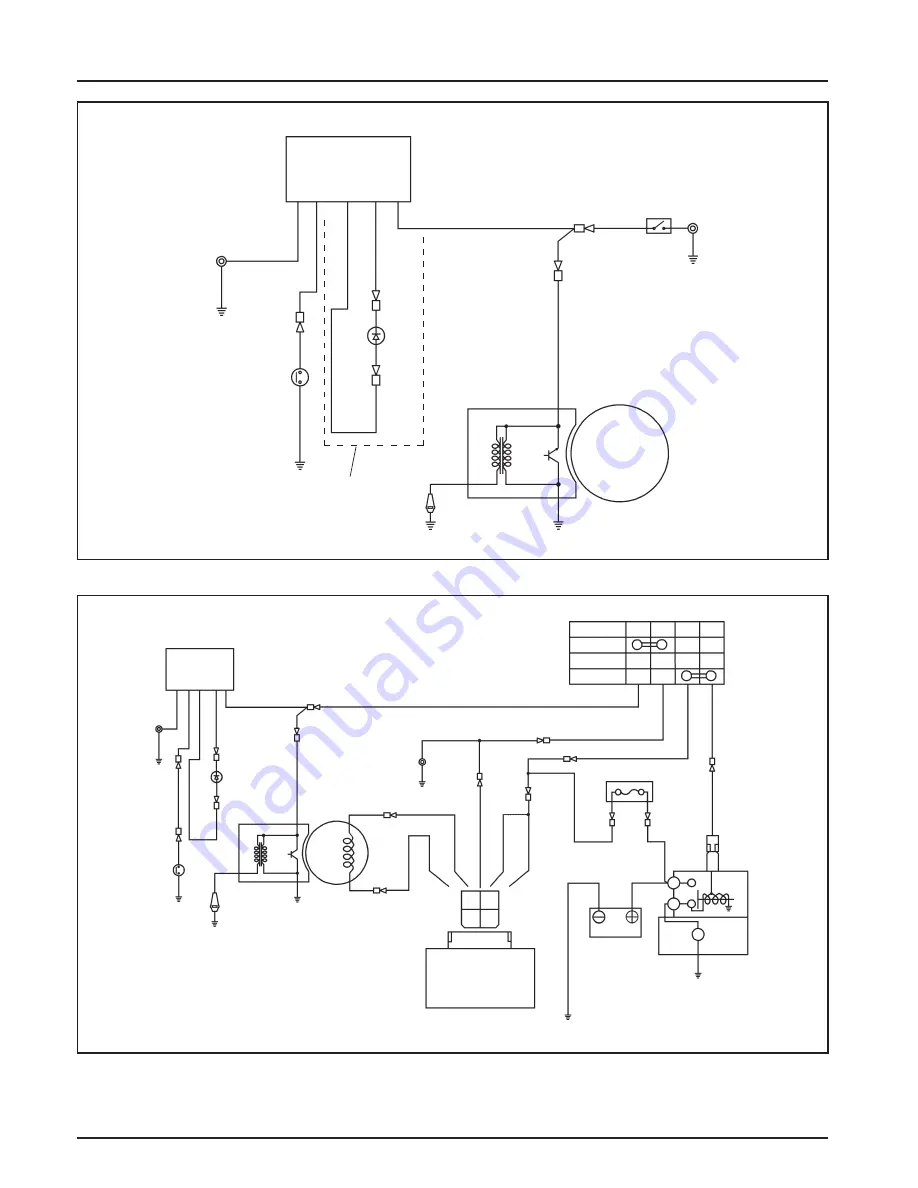
8.12
Section 8
Electrical System and Components
Figure 8-12.
Figure 8-13.
Oil
Warning
Unit
Spark
Plug
Stator
Ignition Module
Stop Switch
Oil Sentry™
Light
Ground
Ground
Ground
Ground
Ground
Ground
Ground
Ground
Ground
Ground
Ground
Ground
Oil
Warning
Unit
Stator
Ignition
Module
B
L
BW
BW
Y
Y
R
BW
R
BW
B
Oil
Sentry™
Gauge
B
L
B
Wire Lead
B
Oil
Sentry™
Gauge
Y
Y
BW
BW
Oil
Sentry™
Light
BW
R
R
BW
Engine
Ground
Engine
Ground
G
G
G
G
G
G
B
R
R
B
B
BW
R RW
RW
RW
Fuse (10 A)
R
R
R
R
Battery
Starting Motor
Rectifier
G
G
R
B
BW
B
R
RW
Wire Color
Off
On
Start
Spark
Plug
Main Switch
B
R
R
R
R
M
Not on All
Models
B
B
B
B
Electronic Ignition System Oil
Sentry™ System, with Indicator Light
(Some Models), Recoil Start.
Electronic Ignition System, 3 Amp
Charging System, Rectified Only. Oil
Sentry™ System. Electric Start
(Solenoid Shift Starter).
Summary of Contents for Command PRO CS
Page 1: ...6 59 0 18 25 217 5 1 6 7 200 1 352 6 3...
Page 2: ......
Page 4: ......
Page 11: ...6HFWLRQ 6DIHW DQG HQHUDO QIRUPDWLRQ 6WRUDJH...
Page 15: ...6HFWLRQ 6DIHW DQG HQHUDO QIRUPDWLRQ HQHUDO 6SHFL FDWLRQV...
Page 17: ...6HFWLRQ 6DIHW DQG HQHUDO QIRUPDWLRQ RQQHFWLQJ 5RG FRQW UDQNFDVH UDQNVKDIW...
Page 18: ...6HFWLRQ 6DIHW DQG HQHUDO QIRUPDWLRQ UDQNVKDIW FRQW OLQGHU RUH OLQGHU HDG OHFWULF 6WDUWHU...
Page 20: ...6HFWLRQ 6DIHW DQG HQHUDO QIRUPDWLRQ 3LVWRQ 3LVWRQ 5LQJV DQG 3LVWRQ 3LQ FRQW...
Page 50: ...6HFWLRQ XEULFDWLRQ 6 VWHP...
Page 56: ...7 6 Section 7 Retractable Starter...
Page 92: ...8 36 Section 8 Electrical System and Components...
Page 128: ...10 16 Section 10 Internal Components...
Page 161: ......